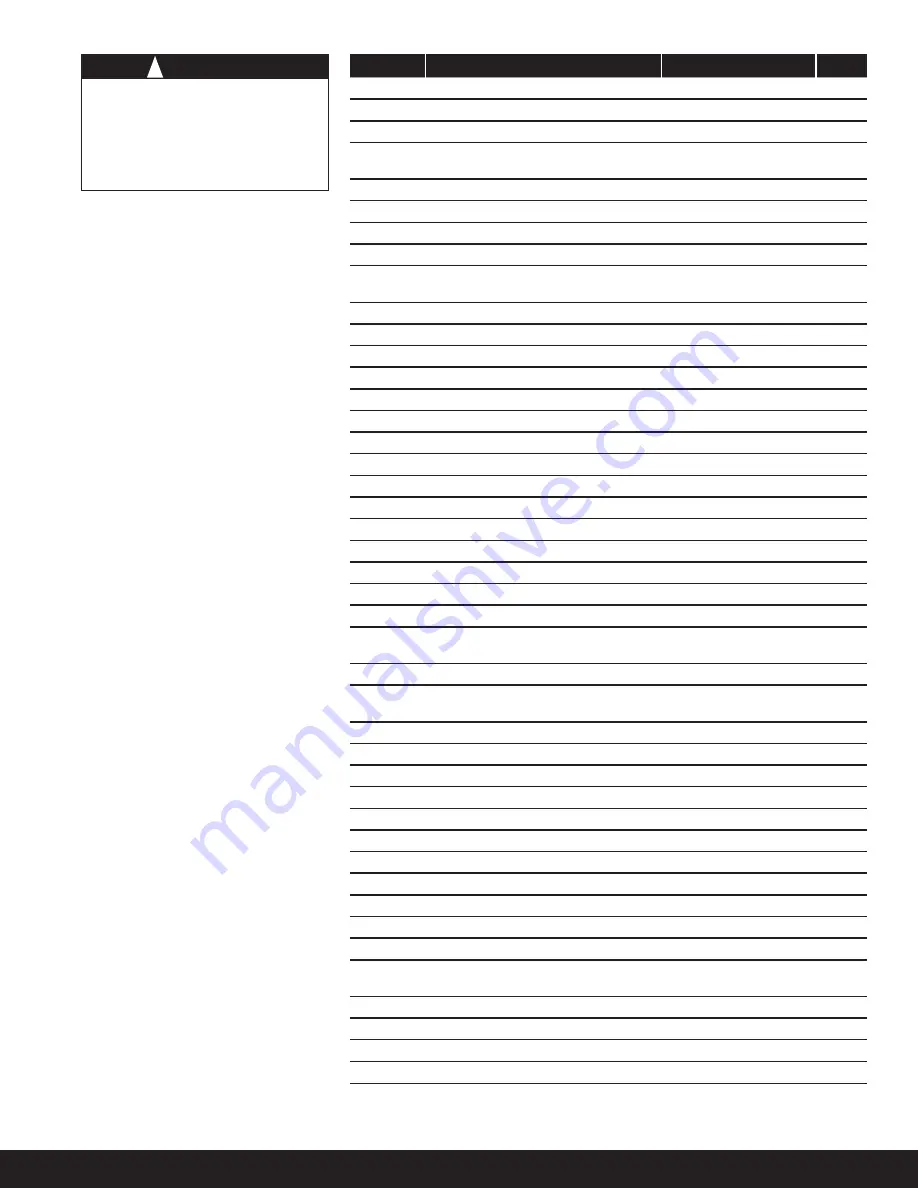
Bulletin 22-00 A / Page 7
Item No.
Description
Material
Qty
1
Seal Cap
6061 Al
1
2
O-Ring, 0.551 ID x 0.691 OD x 0.07
Neoprene
1
3
Bonnet
304L S.S.
4
4
M6 x 18MM Bolt
DIN-ISO
Standard 3506-1
1
5
O-Ring, 0.25 ID x 0.35 OD x 0.062
Neoprene
1
6
Washer, 0.39 ID x 0.625 OD x 0.031
Acetal
1
7
Stem
303 S.S.
1
8
Top Plate, Spring with Roll Pin
1215 Steel
1
9
Spring, Bonnet
Music Wire ASTM
A-228
1
10
Bottom Plate, Spring
1215 Steel
1
11
Ball, 0.281 DIA
440C S.S.
1
12
Follower, Diaphragm
1215 Steel
1
13
O-Ring, 1.5 ID x 1.625 OD x 0.062
Neoprene
1
14
Gasket, 1.875 ID x 2.3 OD x 0.015
Klingersil C-4401
1
15
Diaphragm
301/302 S.S.
1
16
O-Ring, 2.0 ID x 2.125 OD x 0.062
Neoprene
1
17
O-Ring, 0.25 ID x 0.375 OD x 0.062
Neoprene
1
18
Plug, Pilot
303 S.S.
1
19
Seat, Pilot
1215 Steel
1
20
O-Ring, 0.437 ID x 0.563 OD x 0.062
Neoprene
1
21
Spring, Pilot
S.S. ASTM A-313
1
22
Seal Cap
6061-T6 Al
1
23
O-Ring, 0.813 ID x 0.938 OD x 0.062
Neoprene
1
24
Seat, Pilot Plug (“S” Only)
303 S.S.
1
25
Bolt, M10 x 45MM
DIN-ISO
Standard 3506-1
4
26
Plug, Gauge 1/4” NPT
PTFE Coated Steel
1
27
Plug, Pipe 1/16” NPT
Black Oxide
Finish Steel
1
28
O-Ring, 0.125 ID x 0.25 OD x 0.062
Neoprene
1
29
Stem, Manual Opening
303 S.S.
1
30
Nut, Retainer
416 S.S.
1
31
Plug Cap, Manual Opening 7/16-20
6061-T6 Al
1
32
Pin, Roll
420 S.S.
1
33
Seat, Solenoid
303 S.S.
1
34
Port Plate
6061-T6 Al
1
35
Gasket, Port Plate 0.031
MP 15
1
36
Ring, Retaining 2.174 Internal
302 S.S.
1
37
Ring, Backing
302/304 S.S.
1
38
Ring, Seal 2.528 ID x 2.706 OD
PTFE S.S.
1
39
Spring, Piston
Music Wire
ASTM A-228
1
40
Piston
303 S.S.
1
41
Ring, Seal
Tefl on (PTFE)
1
42
Ring, Wear
PTFE EMS-103
1
43
Body
304L S.S.
1
A4W, A4WB, A4WS, A4WBS Parts List
Caution
Regulators with ‘B’ features can only
be adjusted with the pilot solenoid
de-energized. Regulators with the
‘S’ feature can only be adjusted with
the solenoid energized.
!
A4W Disassembly
(See also Bulletin RSBCV)
All A4W series regulators can be
disassembled and all serviceable
and moving parts replaced without
disturbing the piping, but of course,
dis assembly will cause exposure of
some section of piping to atmosphere,
which should be addressed before
disassembly by evacuation and re-
claim of the refrigerant.
For the A4W series inlet regulators, the
seal cap (#1) should be loosened and
the adjustment stem (#7) backed out
until no further spring compression
is felt. If it is known that access to the
range spring (#9) and diaphragm (#14)
is not required, the sub-assembly from
the port plate up can remain intact
and the regulator set point can thus
be preserved, avoiding the need for
gross adjustments when the valve is
put back in service. If access to the
pilot assembly (#17 – 21) on an A4W
is required, then the compression
must be taken off the range spring as
described above, and the bonnet bolts
(#4) removed. If a solenoid fea ture is
incorporated, the solenoid coil (#45)
should now be removed by removing
the coil clip (#44). Never energize a
solenoid coil that is not mounted and
secured on its solenoid actuator (#46).
After removing the bonnet assembly
bolts, the bonnet can be easily
lifted off , and will usually leave the
diaphragm resting on top of the gasket
(#15) and o-ring (#16). Th
e bolts (#25)
retaining the lower sub-assembly can
now be removed. Th
e wear aspects of
the port plate (#34) are the diaphragm
and the pilot assembly, which is
pressed into the top of the port plate.
Remove the diaphragm and inspect
carefully for cracks, or scarring around
the pilot seat area. Th
is is most easily
done by looking down a piece of
large tubing, through the diaphragm,
at a safety lamp or similar light