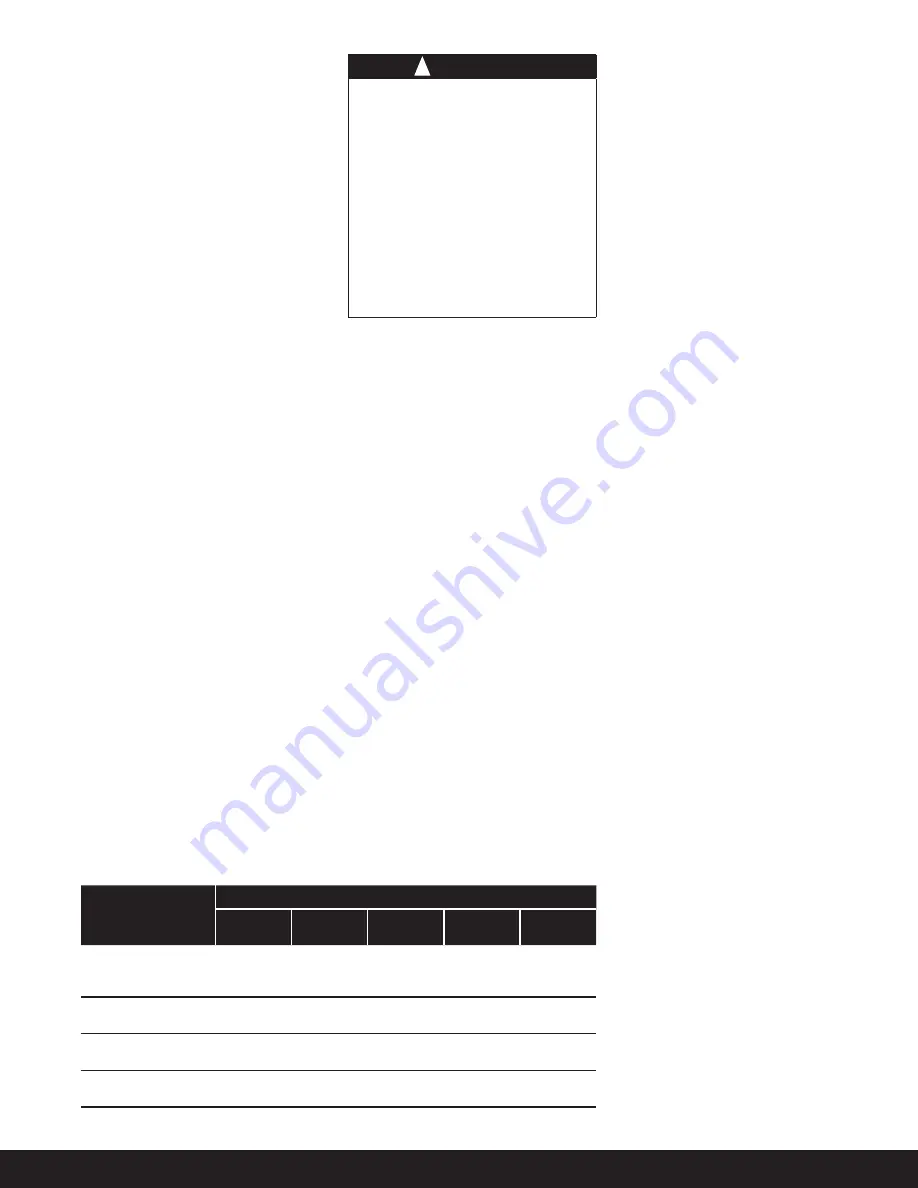
Bulletin 22-05 A / Page 11
corresponding gaskets be aligned
with the appropriate location. Ensure
that all access fi ttings, solenoid
features, and bypass plug are sealed
when re-installing the corresponding
parts. Prior to installing the port plate
inspect the piston, using your hand,
by pulling up and pushing down. Th
e
piston should move freely, without
dragging or hesitation. Adjust all
torques to the values indicated by
torque requirement table.
Tighten all bolts equally to draw the
assembly together evenly, to ensure
properly sealing of all joints. Replace
all seal caps as applicable. When
re-adjusting following servicing,
prevent excessive pressures by starting
with the adjustment stem at low
spring compression until the system
approaches the desired operating
pressures, then re-set as per “AD-
JUSTMENT”, above.
A4WOK and A4WOBK Disassembly
For disassembly and assembly
follow the general procedure
and the procedure for the A4WO.
Th
is regulator has a sealed wire
connection to keep the seal cap from
being removed. Th
is wire must be
removed before the regulator can be
disassembled.
Note:
breaking or removal of the seal
voids any Refrigerating Specialties
Division factory responsibility for the
regulator pressure set-point.
Electrical
Th
e Refrigerating Specialties Division
molded water resistant Class “H”
solenoid coil is designed for long
life and powerful opening force. Th
e
standard coil housing meets NEMA
3R and 4 requirements. Th
is sealed
construction can withstand direct
contact with moisture and ice. By
defi nition, Class “H” coil construction
will permit coil temperatures, as
mea sured by resistance method,
as high as 185°C. (366°F.) Final coil
temperatures are a function of both
fl uid and ambient temperatures. Th
e
higher fl uid temperatures require
lower ambient temperatures for the
maximum coil temperature not to
be exceeded. Conversely, low fl uid
tem peratures permit higher ambient
temperatures.
A solenoid coil should never be
energized except when mounted on its
corresponding solenoid tube.
Th
e molded Class “H” coil is available
from stock with most standard
voltages. However, coils are available
for other voltages and frequencies, as
well as for direct current.
Th
e solenoid coil must be connected
to electrical lines with volts and
Hertz same as stamped on coil. Th
e
supply circuits must be properly
sized to give adequate voltage at the
coil leads even when other electrical
equipment is operating. Th
e coil is
designed to operate with line voltage
from 85% to 110% of rated coil voltage.
Operating with a line voltage above
or below these limits may result
in coil burn-out. Also, operating
with line voltage below the limit
will defi nitely result in lowering the
valve’s maximum opening pressure
diff erential. Power consumption
during nor mal operation will be 18.2
watts or less.
Caution
All personnel working on valves
must be qualifi ed to work on
refrigeration systems. If there
are any question, contact
Refrigerating Specialties before
proceeding with the work.
Before doing any service work,
always be sure to disconnect
the power and isolate the valve.
Failure to do so will result in
venting of ammonia.
!
Valve
Port Size
20 mm
(3/4”)
25 mm
(1”)
32 mm
(1-1/4””)
40 mm
(1-1/2”)
50 mm
(2”)
A4WO,
A4AWOE,
A4WOK
5.0 kg
(11 lbs)
5.0 kg
(11 lbs)
6.1 kg
(13.3 lbs)
6.1 kg
(13.3 lbs)
6.8 kg
(15.1 lbs)
A4WOB,
A4WOBK
5.4 kg
(11.8 lbs)
5.4 kg
(11.8 lbs)
6.4 kg
(14.2 lbs)
6.4 kg
(14.2 lbs)
7.4 kg
(16.2 lbs)
A4WOS,
A4WOES
5.4 kg
(11.8 lbs)
5.4 kg
(11.8 lbs)
6.4 kg
(14.2 lbs)
6.4 kg
(14.2 lbs)
7.4 kg
(16.2 lbs)
A4WOBS
5.7 kg
(12.5 lbs)
5.7 kg
(12.5 lbs)
6.8 kg
(15.0 lbs)
6.8 kg
(15.0 lbs)
7.8 kg
(17.2 lbs)
Socket Weld (SW) and Butt Weld (BW) Valve Weights