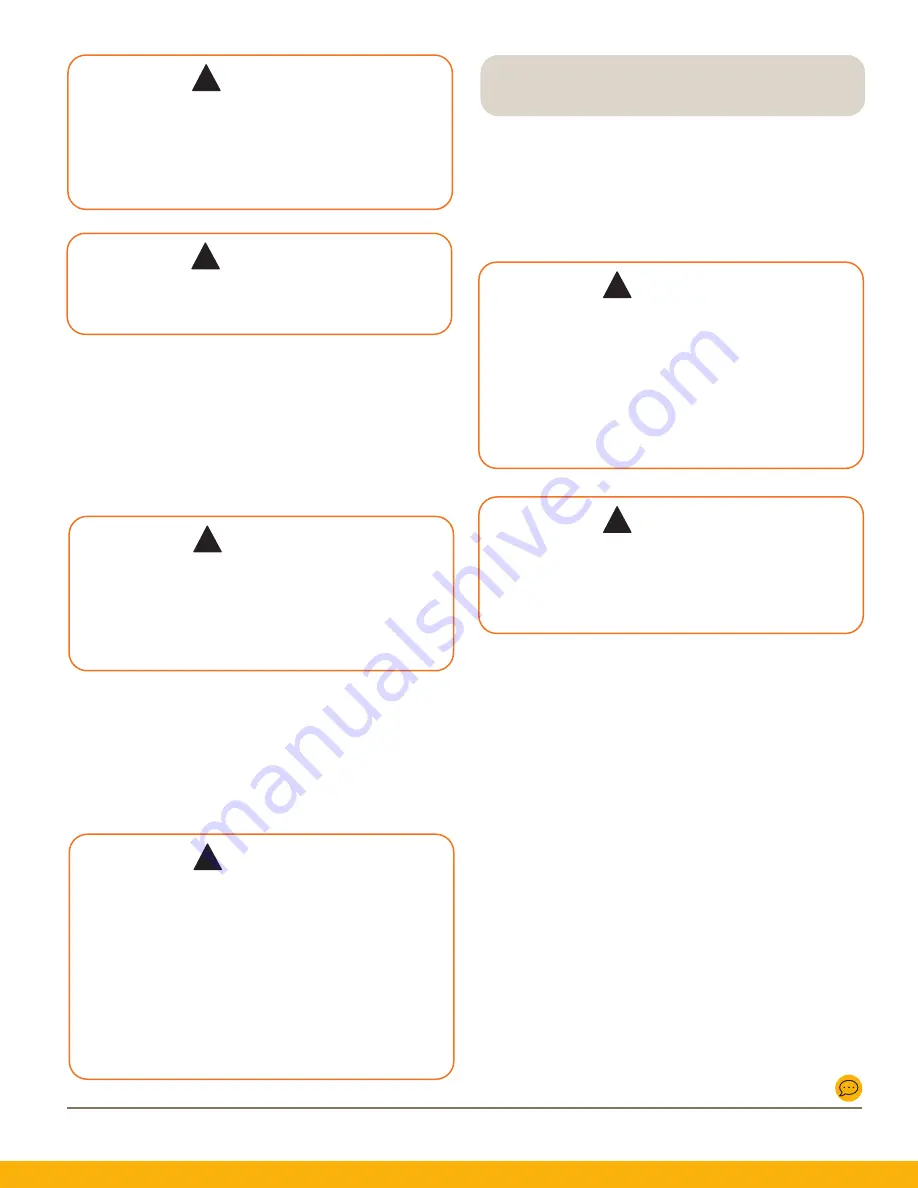
02-9242ME
: AHL Series Pump
Operation & Maintenance Manual | 04/22
9
Use an air pressure regulator to assure maximum air
drive pressure listed on the pump label is not
exceeded. An air pressure regulator must also be
used to assure the pump will not exceed maximum
liquid output pressure listed on the pump label.
!
WARNING
The pump and high pressure liquid system must be
vented prior to installation and start-up.
!
WARNING
The pumps unique design allows for self priming.
To prime, regulate the air pressure to between 5-15 psi
or use an air flow regulator to reduce to a slow stroke
frequency. With the high pressure side connected to a
vented system, allow the pump to cycle till a consistent
flow of liquid is achieved. Let the pump flow freely to
purge any air in the liquid system. Loosening the outlet
gland or pipe can also assist in priming the pump.
Be sure to securely tighten high pressure tube, pipe
or gland with the appropriate torque after the
priming has been achieved.
Reference Tools, Installation, Operation and
Maintenance Manual for tube gland torque value.
!
WARNING
Increase the air pressure using the air pressure regulator
until you achieve your desired output liquid pressure.
At this point the pump will stall. You can calculate the
output pressure by multiplying the input air supply by the
actual pressure ratio of the pump. The pump will
automatically restart if there is a drop in downstream
high pressure.
DO NOT
exceed the maximum liquid pressure and
temperature rating specified on the assembly
drawing and label for your pump.
It is recommended to use a liquid relief valve or
rupture disk to prevent over pressurization of your
high pressure system.
DO NOT
exceed the maximum air drive pressure
listed on your pump label.
!
WARNING
Section 4.0
Unpacking
Section 8.0
Process Media
Parker Autoclave Engineers pumps discussed in this
manual are used for pumping oil, water and oil/water
mixtures. Special seals are also available for chemical
service. Please contact Parker Autoclave Engineers to
discuss availability of special seals.
While testing has shown o-rings to provide
satisfactory service life, actual life will vary widely
with differing service conditions, properties of
reactants, pressure and temperature cycling and
age of the o-ring.
FREQUENT INSPECTIONS SHOULD BE MADE
to detect any deterioration and o-rings replaced
as required.
!
WARNING
The user is required to verify material compatibility
with fluid based on corrosion resistance. A material
list is provided on the assembly drawing to
aid you in the evaluation.
!
WARNING
Pumps are not designed to run for long periods of
time without liquid process media.
Short, dry
pumping cycles should not be a cause for concern.
However, pumps are built using lubricant in the seal areas
and
pumping without fluid will wear away lubricant
and compromise the seal
.
The operating temperatures of the pump are between
0°F to 140°F (18°F to 60°F).