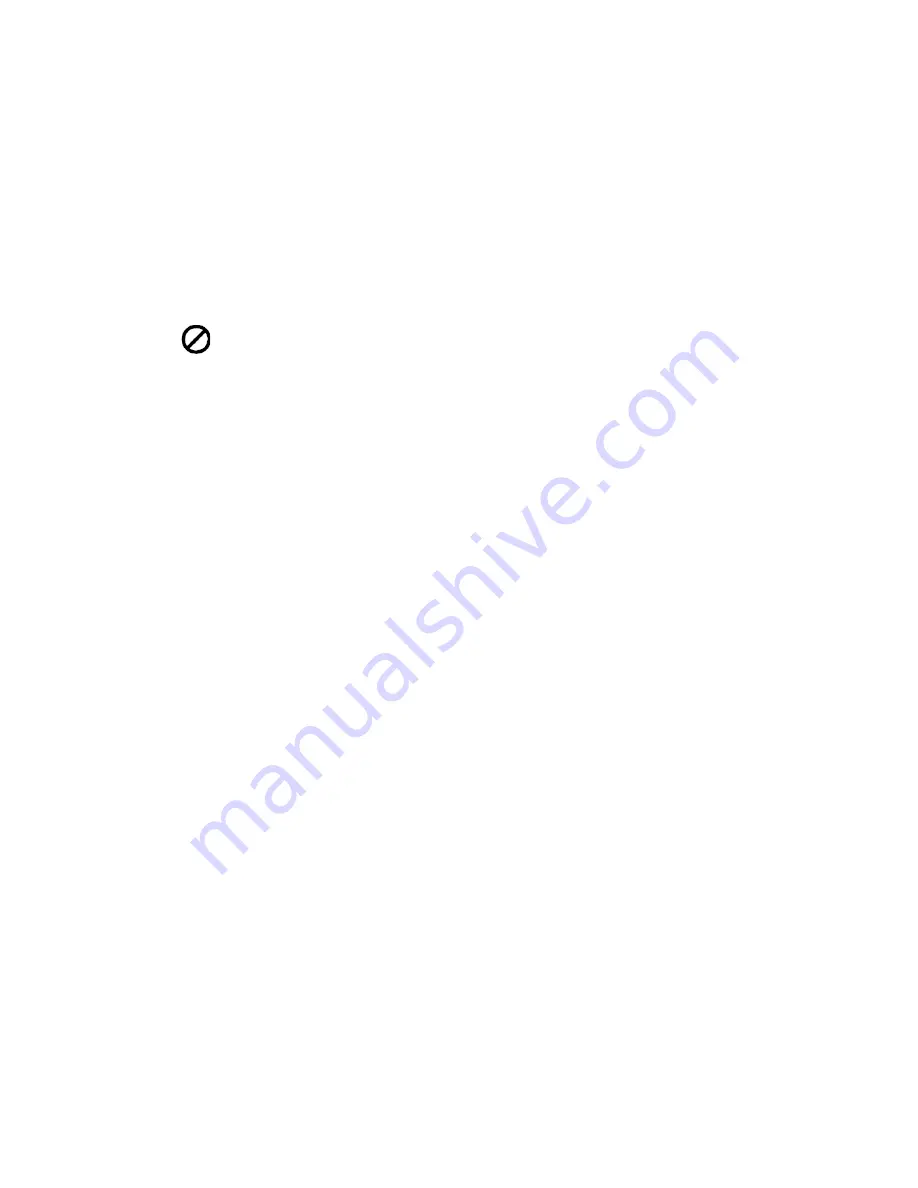
62
•
Mechanical knowledge and skills
Do not attempt troubleshooting and/or subsequent correction or repair if you are not familiar
with or are not proficient in the above fields of expertise.
USE CAUTION WHEN TROUBLESHOOTING. DO NOT PERFORM MAINTENANCE UNLESS:
1.
The system Feed Water Sea Cock Valve [2] is closed.
2.
The system main electrical disconnect switch is switched "OFF", LOCKED, and TAGGED
3.
The "EXPLODED PARTS VIEWS" of this manual is available.
Caution:
ELECTRICAL SHOCK HAZARD. A Volt / Ohm Meter will be necessary. The
following procedures expose the technician to High Voltage and electrical shock
hazard. Only attempt this if you are a qualified electrician and only if surrounding
conditions are safe.
7.7
Weekly Quick Check
The following steps ensure that potential problems are resolved preventing major repairs:
1.
Inspect all fasteners for tightness including brackets, screws, nuts, and bolts. Pay special
attention to the High- Pressure Pump and Electric Motor since they are subject to
increased vibration.
2.
Ensure that Sea Strainer, if installed, is clean and does not restrict flow.
3.
Check the level of the High-Pressure Pump crankcase oil. The minimum oil level is the
center of the sight glass, located at the side of the High-Pressure Pump; the maximum oil
level is at the top of the sight glass window. Use only Parker High Pressure Pump oil.
DO
NOT USE MOTOR OR OTHER HYDRAULIC OIL.
4.
Clean any salt water or salt deposits from the system with a wet rag.
5.
Check for fluid leaks; either oil from the High-Pressure Pump or water from anywhere in the
system.
6.
Check all tubing and high-pressure hoses for wear and friction against abrasive
surfaces. The hoses should not contact heated or abrasive surfaces.
7.
Check Inlet Pressure to the High-Pressure Pump. If pressure is below 10 psi after 5
minutes of operation, replace Pre-Filter element.
7.8
Operator Maintenance Intervals
The frequency of required maintenance is dependent on the regularity of usage, the
condition of the intake water (the location of use), the length of time the system is exposed
to water, the total running time and, in some cases, the manner in which the system is
installed or operated. Use Table 6 in chapter 6 as a general guideline for maintenance
timeline
Summary of Contents for AQUA DUO A455C-2800
Page 15: ...15 Figure 2 4 Piping and Instrumentation Diagram 2800 3600 GPD ...
Page 17: ...17 Figure 2 6 Piping and Instrumentation Diagram 4800 6200 GPD ...
Page 32: ...32 Figure 2 26 Hose Tube Connection Instructions Figure 2 27 Tubing Fitting Internals ...
Page 63: ...63 8 DRAWINGS DIAGRAMS ...
Page 64: ...64 1 P ID ...
Page 65: ...65 ...
Page 66: ...66 ...
Page 67: ...67 ...
Page 68: ...68 2 GA Drawing ...
Page 69: ...69 ...
Page 70: ...70 ...
Page 71: ...71 ...
Page 72: ...72 ...
Page 73: ...73 ...
Page 76: ...76 4 Wiring Diagrams ...
Page 77: ...77 ...
Page 78: ...78 ...
Page 79: ...79 ...
Page 80: ...80 ...
Page 81: ...81 ...
Page 82: ...82 ...