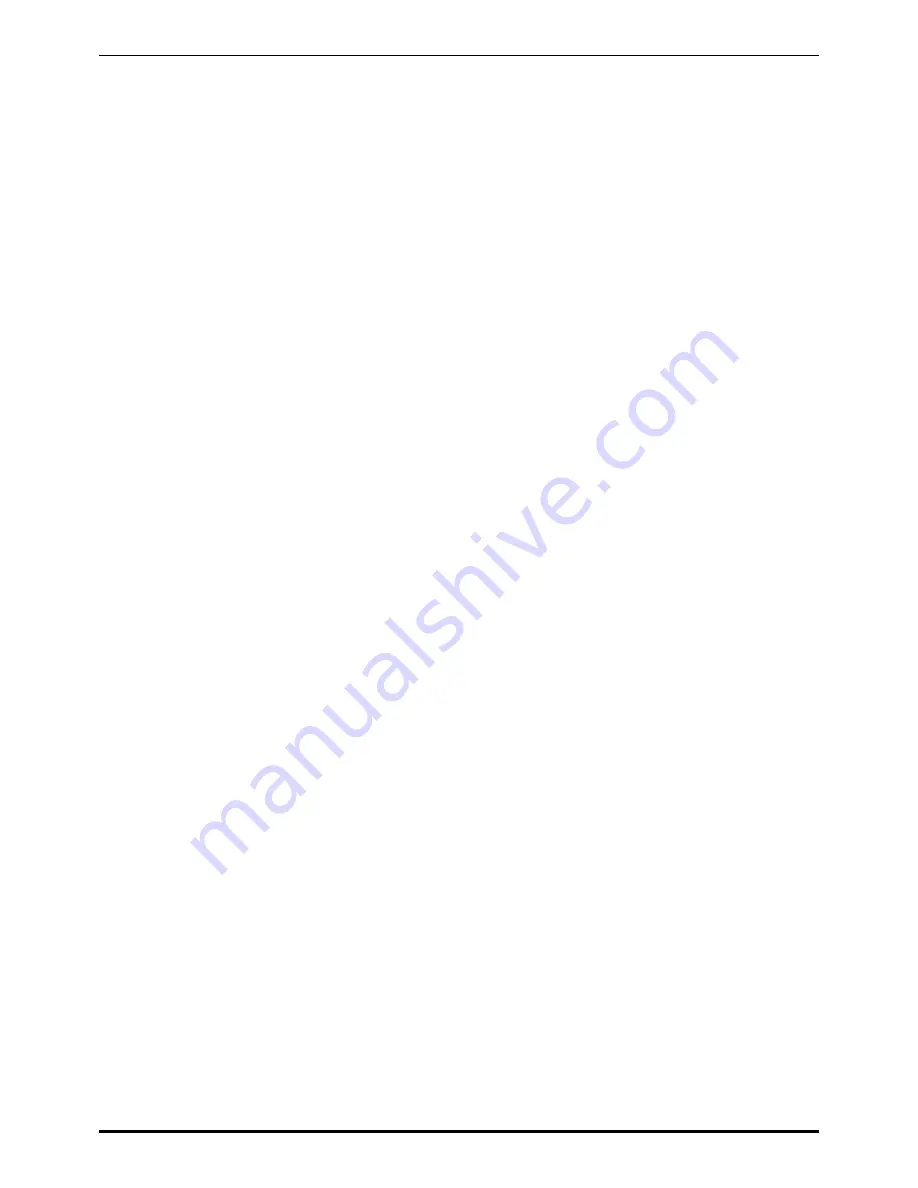
2
1 Safety
Information
Do not operate this equipment until the safety information and instructions in this user guide have been read and understood by all
personnel concerned.
USER RESPONSIBILITY
FAILURE OR IMPROPER SELECTION OR IMPROPER USE OF THE PRODUCTS DESCRIBED HEREIN OR RELATED ITEMS CAN CAUSE
DEATH, PERSONAL INJURY AND PROPERTY DAMAGE.
This document and other information from Parker Hannifin Corporation, its subsidiaries and authorised distributors provide product or system
options for further investigation by users having technical expertise.
The user, through its own analysis and testing, is solely responsible for making the final selection of the system and components and assuring
that all performance, endurance, maintenance, safety and warning requirements of the application are met. The user must analyse all aspects of
the application, follow applicable industry standards, and follow the information concerning the product in the current product catalogue and in
any other materials provided from Parker or its subsidiaries or authorised distributors.
To the extent that Parker or its subsidiaries or authorised distributors provide component or system options based upon data or specifications
provided by the user, the user is responsible for determining that such data and specifications are suitable and sufficient for all applications and
reasonably foreseeable uses of the components or systems.
This equipment is safe and will not present a risk to health when properly used in accordance with this user guide. It is essential that users
familiarise themselves with its contents and be fully conversant with this equipment and the correct operating procedures before use.
Breathing air equipment is by its very nature used in critical applications. It is therefore essential that only competent personnel trained, qualified,
and approved by Parker Hannifin should perform installation, commissioning, service and repair procedures.
Use of the equipment in a manner not specified within this user guide may result in an unplanned release of pressure, which may cause serious
personal injury or damage.
When handling, installing or operating this equipment, personnel must employ safe engineering practices and observe all related regulations,
health & safety procedures, and legal requirements for safety.
Compressed air must be delivered at a comfortable temperature for breathing.
Ensure that the equipment is depressurised prior to carrying out any maintenance.
Maintenance MUST be carried out regularly to ensure optimum performance. All maintenance, filter element changes and a record of working
hours usage, should be detailed in a maintenance and examination record.
Provision should be made to test the quality of delivered air. Use suitable test equipment, e.g. detection tubes and/or in-line monitoring equipment
and retain the appropriate records.
Parker Hannifin can not anticipate every possible circumstance which may represent a potential hazard. The warnings in this manual cover the
most known potential hazards, but by definition can not be all-inclusive. If the user employs an operating procedure, item of equipment or a
method of working which is not specifically recommended by Parker Hannifin the user must ensure that the equipment will not be damaged or
become hazardous to persons or property.
Should you require an extended warranty, tailored service contracts or training on this equipment, or any other equipment within the Parker
Hannifin range, please contact your local Parker Hannifin office.
Details of your nearest Parker Hannifin sales office can be found at www.parker.com/dhfns
Retain this user guide for future reference.