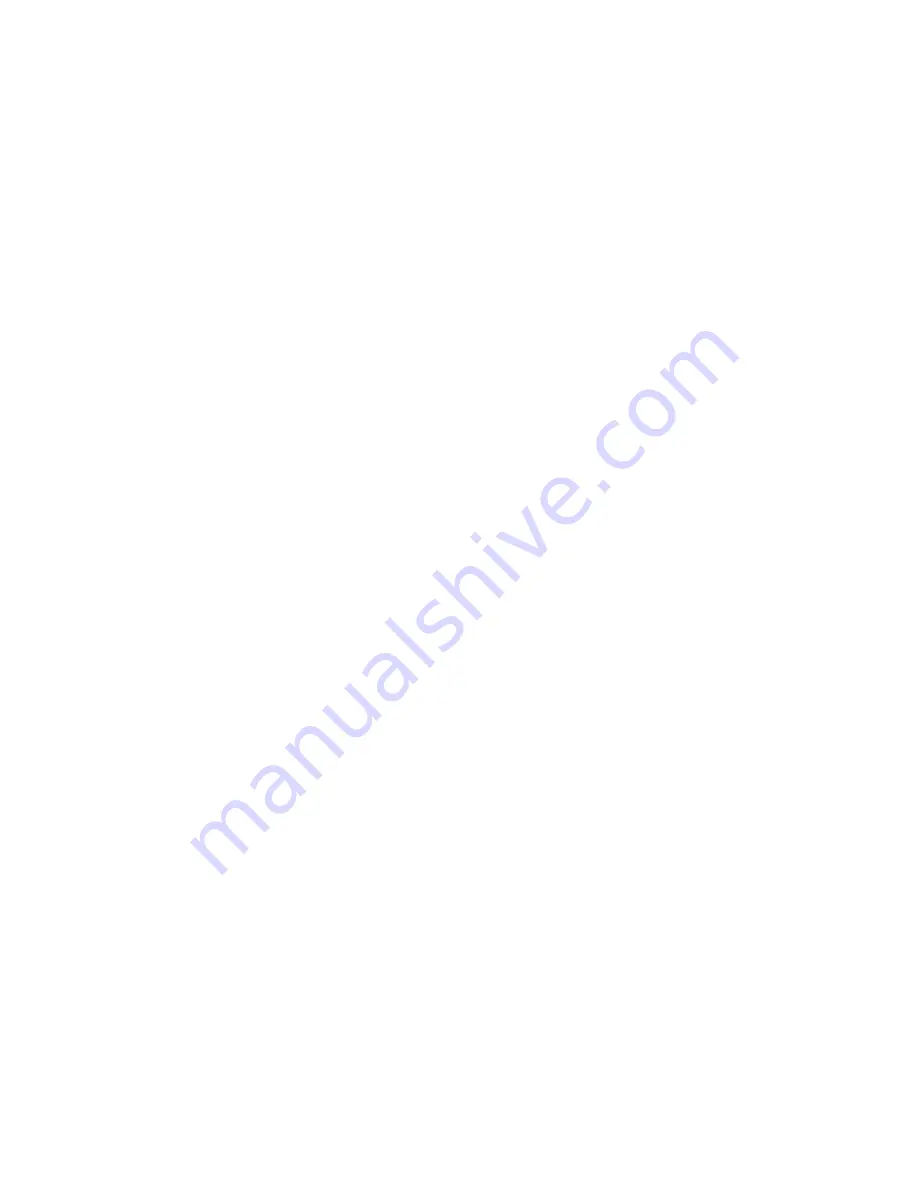
INTRODUCTION • OEM650/OEM650X
2
step motors. Operation of the OEM350/OEM350X is identical to that
of the OEM650/OEM650X. For clarity, instructions in this manual
use only the name OEM650/OEM650X. Except where differences are
specifically noted (resistor values for motor current settings, for
example), OEM650 instructions also apply to the OEM350, and
OEM650X instructions also apply to the OEM350X.
Features
The OEM650 requires an external power supply. It uses 24VDC -
75VDC for its power input. Compumotor’s motors are two-phase
hybrid motors (permanent magnet type). Four, six, or eight leaded
motors may be used with the internal phases connected for either
parallel or series operation. The motor’s inductance cannot drop
below 0.5 mH.
For best performance, motor inductance should be
between 1 mH and 10 mH, but motors with inductance ratings as low
as 0.5 mH may be used
.
Use the OEM350/OEM350X with motors
whose inductance is in the 10 mH to 80 mH range.
The OEM650/
OEM650X provides the following features:
❐
Microprocessor controlled microstepping provides smooth opera-
tion over a wide range of speeds
❐
Full short circuit protection for phase-to-phase and phase-to-
ground short circuits
❐
Motor regeneration protection
❐
Over-temperature protection
❐
Uses low-inductance motors for improved high-speed performance
(23, 34 frame size motors available with torques from 65 - 400 oz-
in)
❐
Three-state current control for reduced motor/drive heating
❐
LED status indicators:
POWER
and
FAULT
(latched)
❐
Optically coupled step, direction, and shutdown inputs are
compatible with all Compumotor indexers (25-pin D connector)
❐
A fault output to signal other equipment if a fault occurs
❐
24VDC - 75VDC single power input
❐
16 jumper selectable motor resolutions (200 - 50,800 steps/rev)
❐
2 Mhz step input
❐
Waveform correction and phase offset for improved smoothness
❐
Built-in indexer (position controller)
❐
-M2 option allows users to store programmed sequences in
nonvolatile memory
❐
I/O for motion and basic machine coordination