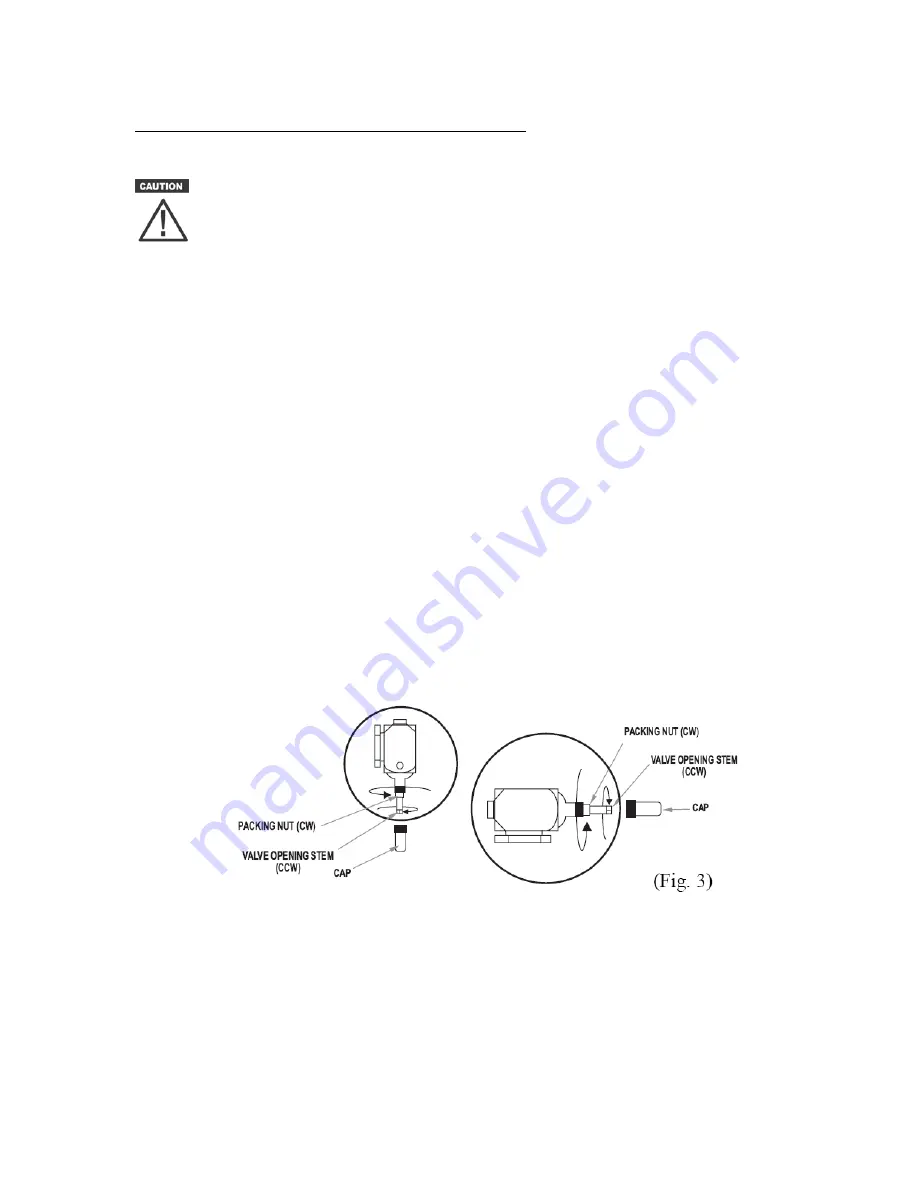
Section 6.0 – START UP PROCEDURE
There should be NO air flow through the dryer before or during start up. It
is recommended that the dryer be installed with bypass piping to better
service the unit.
SC/CT 80-100
1.
Plug in unit.
2.
Switch unit on. On / Off switch will light green when unit is running.
3.
Unit is ready for operation.
SC/CT 130 – 165
1.
After electrical connection (Section 3), apply power.
2.
Leave power on for 8 hours before proceeding any further.
3.
Remove side panel from unit.
4.
Some units are shipped with the refrigeration service valve tagged.
These tagged service valves must not be opened until the dryer is ready
to be started and the main power is permanently applied. Only tagged
service valves must be opened.
5.
Locate tagged service valves and remove end cap from valve stem. (Fig.
3)
6.
Using a refrigeration service or small crescent wrench, turn the valve stem
counterclockwise until it stops. Occasionally it may be necessary to re-
tighten the packing nut (turn clockwise) if a leak is noticed. The valve will
now be fully opened. (Fig. 3)
7.
Replace cap.
8.
Switch unit on. On / Off switch will light green when unit is running.
Summary of Contents for CT3000
Page 21: ...Section 11 0 MAINTENANCE CHARTS cont Element Replacement Log Part No Date Initials ...
Page 22: ...Section 12 0 ASSOCIATED DRAWINGS ...
Page 23: ......
Page 24: ......
Page 25: ......
Page 26: ......
Page 27: ......
Page 28: ......
Page 29: ......
Page 30: ......
Page 31: ......
Page 32: ......
Page 33: ......
Page 34: ......
Page 35: ......
Page 36: ......
Page 37: ......
Page 39: ......