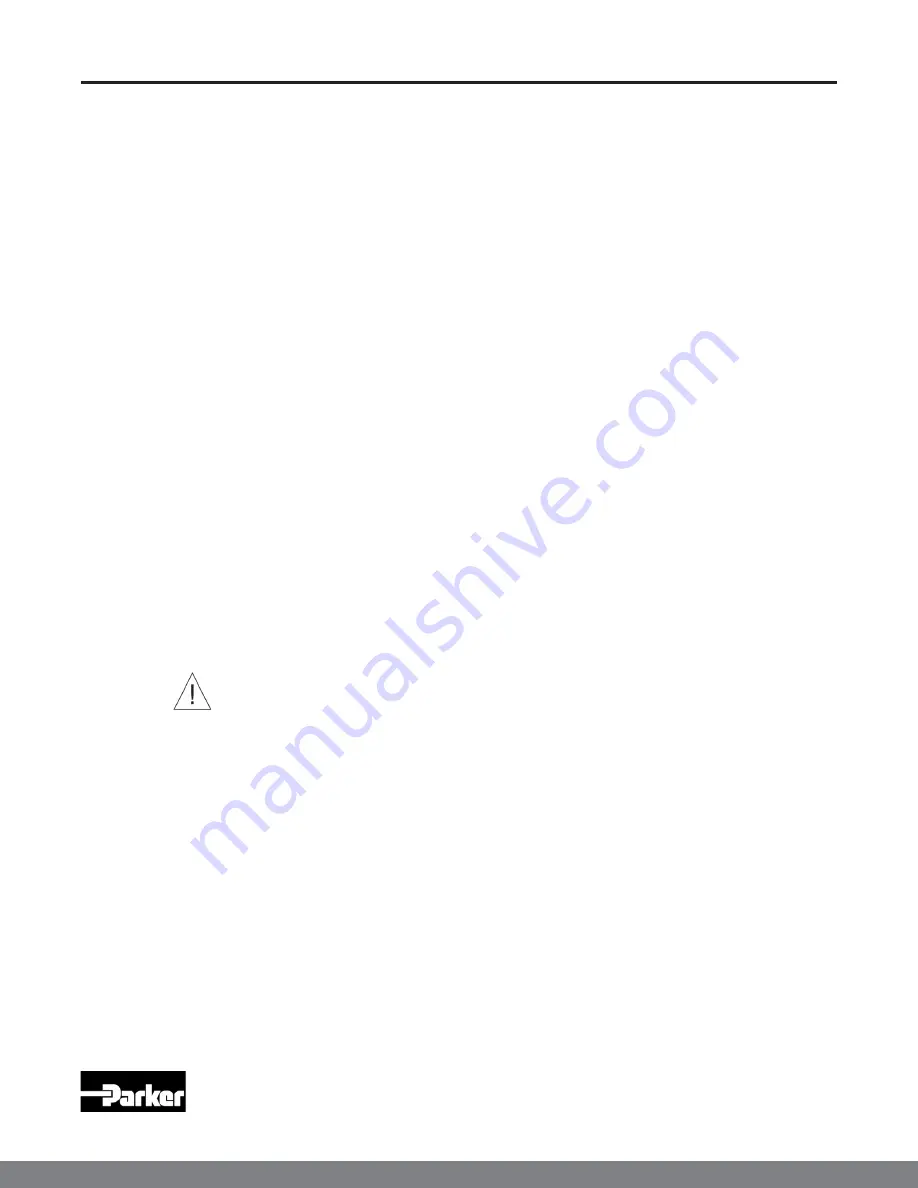
Parker Hannifin Corporation
Industrial Gas Filtration and Generation Division
Haverhill, MA
• 1-800-343-4048
Parker Zero Air Generators
Models HPZA-3500, HPZA-7000, HPZA-18000, HPZA-30000
Bulletin TI-HPZA-3500H
Installation
General
Location
Utilities
All installation procedures for Parker Zero Air Generators should be performed by suitable
personnel using reasonable care. See Figure 4 for Recommended Installation Schematic.
The Parker Zero Air Generator is a free-standing benchtop or wall mountable unit. When mounting the
generator on the wall, use mounting hardware which is adequately sized to support the weight of the
generator. The generator should be mounted to the wall (or similar mounting surface) in a vertical
position according to National Electrical Code (NEC) and local building code guidelines. The mounting
dimensions are shown in Figure 3.
A shut-off valve and a pressure regulator should be installed directly upstream from the Parker Zero Air
Generator. The shut-off valve isolates the unit from the air line for maintenance and troubleshooting
tasks. The pressure regulator controls the inlet air pressure and should be set to maintain a constant
pressure between 40 psig and 125 psig (2.8 barg and 8.6 barg). Maintaining a constant inlet air
pressure will minimize any system pressure fluctuations. Parker offers a pressure regulator, complete
with a pressure gauge, as an accessory (P/N 72-130-V883).
The Parker Zero Air Generator should be installed in an area relatively free from excessive dust and
dirt, where the ambient temperature is between 60°F and 100°F (16°C and 43°C).
Do not install the
generator outdoors.
There is no limit to the distance between the generator and the point of use as
long as tubing type, size, cleanliness, and pressure drop are taken into consideration. Approximately
6” of space should be allowed along the top and sides of the generator to ensure proper ventilation.
Compressed Air -
The Parker Zero Air Generator requires a source of clean, dry compressed
air (40 psig-
125 psig/2.8 barg-8.6 barg) for optimal operation. The air should be as close to instrument quality as
possible and supplied at a flow rate and pressure above those required at the point of use. The
temperature and/or dewpoint of the supply air should be at room temperature (or lower), and the air
should be relatively free of compressor oil, hydrocarbons, and particulate matter. Contamination of the
catalyst bed may occur if it is exposed to certain compounds (warning below). To prevent premature
contamination of the catalyst module, the inlet to the compressed air supply compressor should be vented
outdoors.
Chlorinated hydrocarbon compounds and chlorofluorocarbons (or freons) will permanently
contaminate the hydrocarbon catalyst module in the Zero Air Generator. Extreme care should
be taken when specifying an air supply for the generator to ensure that these compounds are
not present in the air supply nor likely to get into the compressor providing air to the
generator.
The hydrocarbon catalyst module can also be contaminated by high concentrations of lead,
sulfur, or phosphorous compounds, heavy metals, and long chain polymers. Care should be
taken to avoid introducing these compounds into the Zero Air Generator. Specifically, assure
that none of these compounds are stored near the inlet to the compressor supplying the
system with compressed air. The intake for the compressor should be vented to the outdoors.
If the compressed air supply source is subject to halogenated hydrocarbon exposure, an auxiliary
activated carbon scrubber (P/N 76080) should be installed directly upstream from the generator.
Connect the compressed air supply to the
1/4” NPT (female) inlet port on the right side of the generator
(see Figure 1).