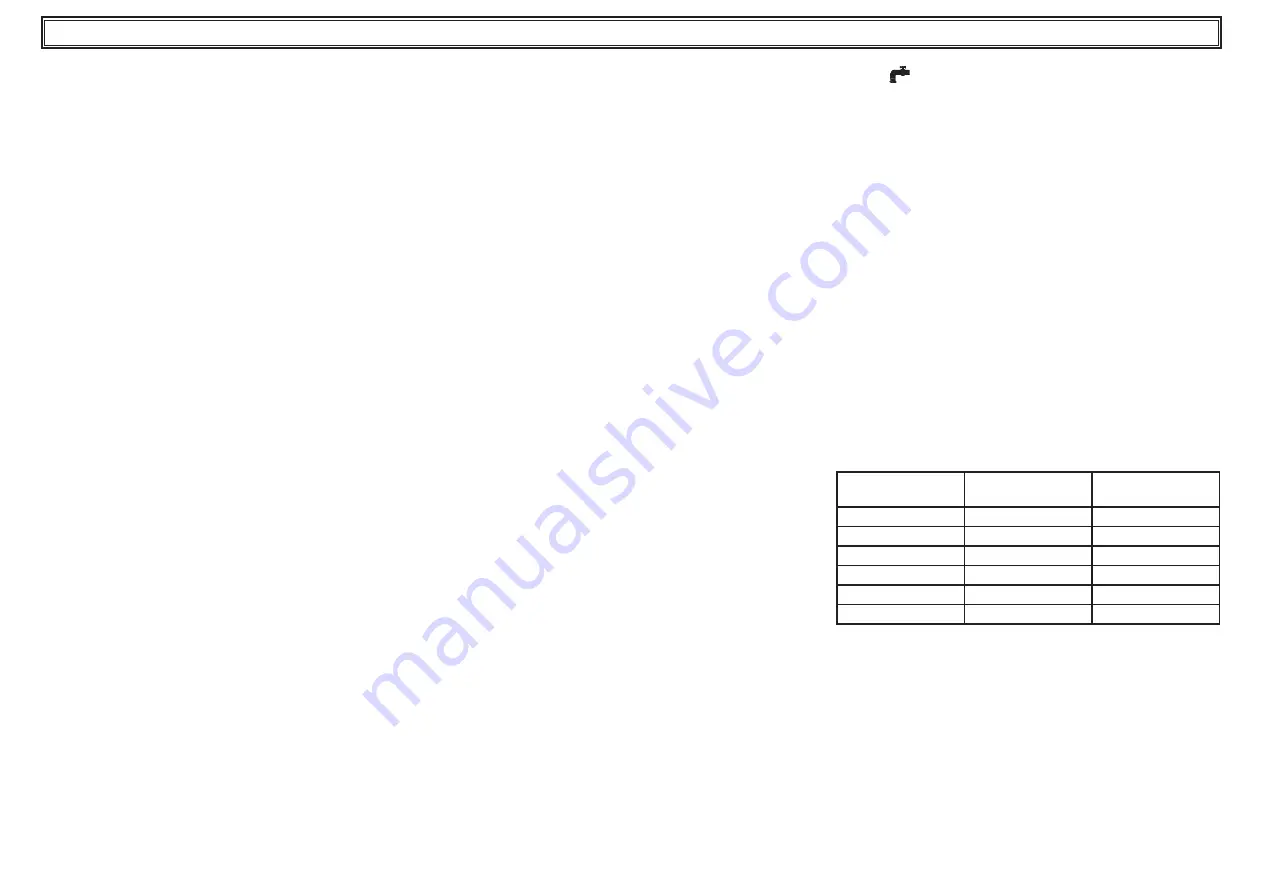
English
2/8
PCW420-650
2 Introduction
These water coolers are monoblock units for the production of cooled
water in a closed circuit.
The fan, pump and compressor motors are equipped with a thermal
protector that protects them against possible overheating.
2.1 Transport
The packed unit must remain:
a) Upright;
b) Protected against atmospheric agents;
c) Protected against impacts.
2.2 Handling
Use a fork-lift truck suitable for the weight to be lifted, avoiding any
type of impact (see paragraph 7.2).
2.3 Inspection
a) All the units are assembled, wired, charged with refrigerant and oil
and tested in the factory;
b) On receiving the machine check its condition: immediately notify
the transport company in case of any damage;
c) Unpack the unit as close as possible to the place of installation.
2.4 Storage
a) Keep the unit packed in a clean place protected from damp and
bad weather.
b) Do not stack the units;
c) Follow the instructions given on the package.
3 Installation
Y
For correct installation, follow the instructions given in par.7.2, 7.3,
7.4 and 7.8.
!
The product installed must be suitably protected against fi re risk
(ref. EN378-3).
Y
For the correct application of the warranty terms, follow the in-
structions given in the start-up report, fi ll it in and send it back to Seller
!
Liquids to be chilled
The liquids to be chilled must be compatible with the materials used.
Examples of liquids used are water or mixtures of
water and ethylene
or propylene glycols.
The liquids to be chilled must not be fl ammable.
If the liquids to be chilled contain hazardous substances (e.g. ethylene/
propylene glycol), any liquid discharged from a leakage area must be
collected, because it is harmful to the environment. When draining
the hydraulic circuit, comply with the current regulations and do not
disperse the contents in the environment.
3.1 Operating space
To allow an unrestricted air fl ow around the chiller and easy access for
servicing, ensure the area around the unit is kept free of obstacles (see
paragraph 7.3).
Leave a space of at least 80 inch (2 metres) above the refrigerator in
models with vertical emission of condensation air.
3.2 Versions
Air-cooled version
Axial fans (A)
Do not create cooling air recirculation situations.
Do not obstruct the ventilation grilles.
The ducting of extracted air is not recommended for versions with axial
fans.
Centrifugal version (C)
Always ensure a minimum counterpressure on the delivery of
fans, ducting the individual hot air outlets.
Water- cooled version (W)
If the water to the condenser is in open circuit, install a mesh fi lter on
the condensation water inlet.
Please note that for special cooling water types such as demineral-
ized, deionized or distilled it is necessary to contact the manufacturer
to verify which kind of condenser should be used since the standard
material may not be suitable.
3.3 Water circuit
3.3.1
Checks and connection
Y
Before connecting the chiller and fi lling the water circuit, check
that all the pipes are clean. If not, wash them out thoroughly.
Y
If the plumbing circuit is of the closed type, under pressure it is
advisable to install a safety valve set to 87 PSIg (6 bar).
Y
Always install mesh fi lters on the water inlet and outlet pipelines.
Y
If the hydraulic circuit is intercepted by automatic valves, protect
the pump with an anti-hammering system.
Y
If the hydraulic circuit is emptied for shut-down periods we
recommend that you add lubricating fl uid to the pump’s impeller to
avoid the risk of blockage when it is re-started. In case the impeller is
blocked then you should unblock it manually.
Remove the rear cover of the pump and carefully turn the plastic fan.
If the impeller is stuck then remove the fan and turn the impeller shaft
directly. After un-blocking the impeller re-assemble the fan and cover.
Preliminary checks
1) Check that any shut-off valves in the water circuit are open.
2) In the case of a closed water circuit, check that an expansion tank
of suitable capacity has been installed. See paragraph 3.3.3.
Connection
1) Connect the water cooler to the inlet and outlet piping, using the
special connections located on the back of the unit.
We recommend the use of fl exible unions to reduce system rigidity.
2) Fill the water circuit using the fi tting provided on the rear of the
chiller (
).
3) The tank is equipped with a breather valve that should be operated
manually when fi lling the tank. Also, if the hydraulic circuit has high
points, install a vent valve at the highest points.
4) We recommend that taps are installed on the inlet and outlet pipes,
so that the unit can be excluded for maintenance when necessary.
5) If the chiller works with an open tank, the pump must be installed
on intake to the tank and on delivery to the chiller.
Subsequent checks
1) Check that the tank and the circuit are completely full of water and
that all the air has been expelled from the system.
2) The water circuit must always be kept full. For this reason, carry
out periodic checks and top the circuit up if necessary, or install an
automatic fi lling kit.
3.3.2
Water and ethylene glycol
If installed outdoors or in an unheated indoor area, it is possible that
the water in the circuit may freeze if the system is not in operation dur-
ing the coldest times of the year.
To avoid this hazard:
a) Equip the chiller with suitable antifreeze protection devices, avail-
able from the manufacturer as optional accessories;
b) Drain the system via the drain valve if the chiller is to remain idle for
a prolonged period;
c) Add an appropriate quantity of antifreeze to the water in circulation
(see table).
Sometimes the temperature of the outlet water is so low as to require
the addition of ethylene glycol in the following percentages.
Outlet water
temperature [°C]
Ethylene glycol
(% vol.)
Ambient
temperature
4
5
-2
2
10
-5
0
15
-7
-2
20
-10
-4
25
-12
-6
30
-15
3.3.3 Expansion
tank
To avoid the possibility of an increase or decrease in the volume of the
fl uid due to a signifi cant change in its temperature causing damage to
the machine or the water circuit, we recommend installing an expansion
tank of suitable capacity.
The expansion tank must be installed on intake to the pump on the rear
connection of the tank.
The minimum volume of an expansion tank to be installed on a closed
circuit can be calculated using the following formula:
V=2 x Vtot x (Pt min - P t max)
where
Vtot= vol. circuit total (in litres)
P t min/max= specifi c weight at the minimum/maximum temperature
reached by the water [kg/dm3].
Summary of Contents for Hyperchill PCW420
Page 2: ......
Page 35: ......
Page 37: ...Ap ndice Appendix Appendice Anexo DATE 14 02 2022 Rev 17 CODE 398H272297...
Page 38: ......
Page 51: ...13 7 5 Circuit diagram PCW420 650 NP PCW650 PCW650 A1...
Page 52: ...14 7 6 Wiring diagram PCW420 510 PCW420 650 Sheet 1 of 11...
Page 53: ...15 7 6 Wiring diagram PCW420 510 PCW420 650 Sheet 2 of 11...
Page 54: ...16 7 6 Wiring diagram PCW420 510 PCW420 650 Sheet 3 of 11...
Page 55: ...17 7 6 Wiring diagram PCW420 510 PCW420 650 Sheet 4 of 11...
Page 56: ...18 7 6 Wiring diagram PCW420 510 PCW420 650 Sheet 5 of 11...
Page 57: ...19 7 6 Wiring diagram PCW420 510 PCW420 650 Sheet 6 of 11...
Page 58: ...20 7 6 Wiring diagram PCW420 510 PCW420 650 Sheet 7 of 11...
Page 59: ...21 7 6 Wiring diagram PCW420 510 PCW420 650 Sheet 8 of 11...
Page 60: ...22 7 6 Wiring diagram PCW420 510 PCW420 650 Sheet 9 of 11...
Page 61: ...23 7 6 Wiring diagram PCW420 510 PCW420 650 Sheet 10 of 11...
Page 62: ...24 7 6 Wiring diagram PCW420 510 PCW420 650 Sheet 11 of 11...
Page 63: ...25 7 6 Wiring diagram PCW650 PCW420 650 Sheet 1 of 11...
Page 64: ...26 7 6 Wiring diagram PCW650 PCW420 650 Sheet 2 of 11...
Page 65: ...27 7 6 Wiring diagram PCW650 PCW420 650 Sheet 3 of 11...
Page 66: ...28 7 6 Wiring diagram PCW650 PCW420 650 Sheet 4 of 11...
Page 67: ...29 7 6 Wiring diagram PCW650 PCW420 650 Sheet 5 of 11...
Page 68: ...30 7 6 Wiring diagram PCW650 PCW420 650 Sheet 6 of 11...
Page 69: ...31 7 6 Wiring diagram PCW650 PCW420 650 Sheet 7 of 11...
Page 70: ...32 7 6 Wiring diagram PCW650 PCW420 650 Sheet 8 of 11...
Page 71: ...33 7 6 Wiring diagram PCW650 PCW420 650 Sheet 9 of 11...
Page 72: ...34 7 6 Wiring diagram PCW650 PCW420 650 Sheet 10 of 11...
Page 73: ...35 7 6 Wiring diagram PCW650 PCW420 650 Sheet 11 of 11...
Page 74: ......
Page 75: ......