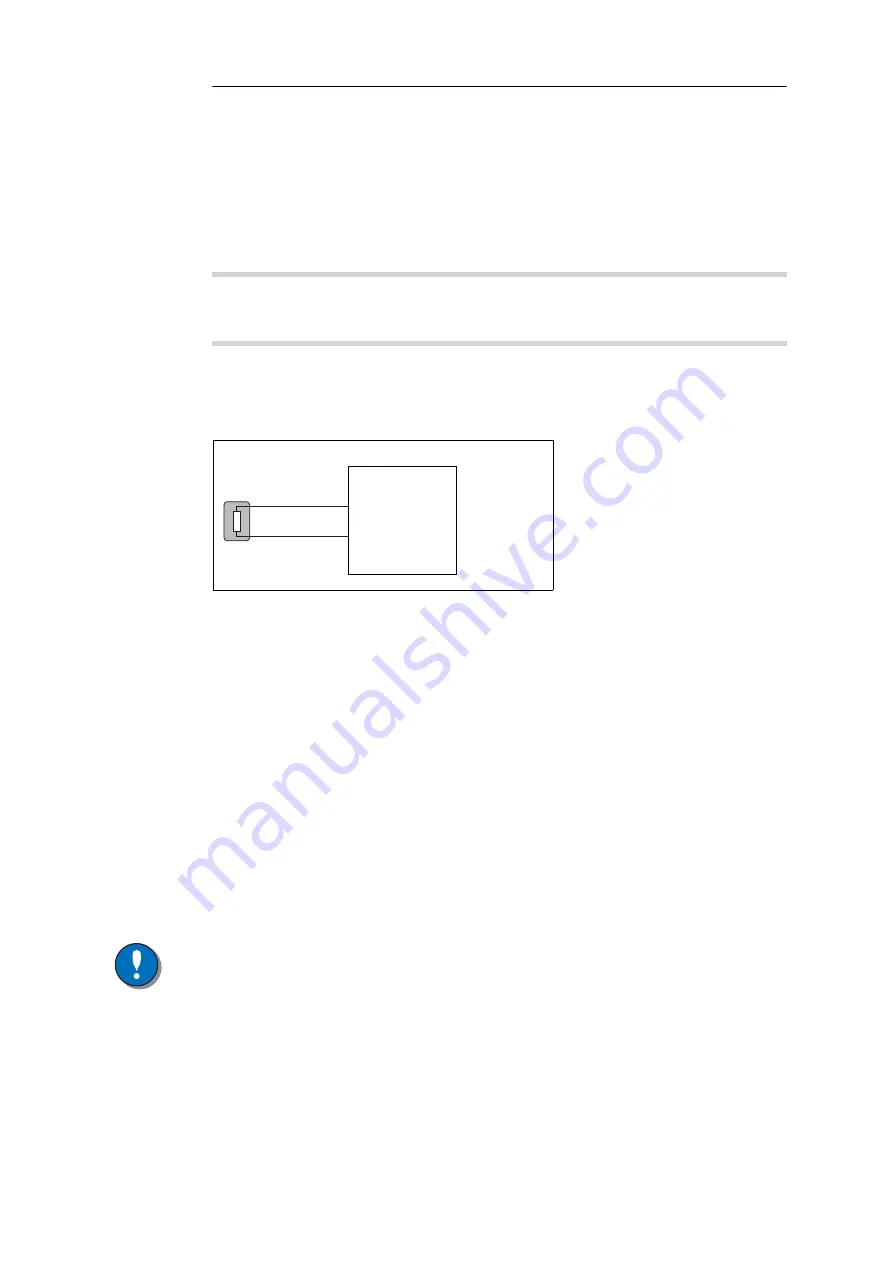
12
Addressing/terminating
Instruction book, IQAN
Addressing/terminating
Addressing
Each IQAN expansion module will have a specific address, enabling the master module
to communicate with the modules through the CAN-bus. When operating, the system
distinguishes between different modules by first verifying the module type and
secondly, through the modules having unique addresses.
The maximum number of similar modules in a system is four or eight depending on the
master module, denoted in the first case as addresses 0, 1, 2, 3 respectively. In order to
assign any IQAN module a unique CAN-address, an ID-Tag will have to be connected
to the positions ADDR-H and ADDR-L.
Connecting of Id-Tag.
Terminating
To eliminate interference in the communications through the CAN-bus, the CAN-bus
must be terminated at both ends. By default, if no ID-tag is installed in an IQAN
master, it will be terminated internally to be the Bus master and will have no special
configuration.
When an IQAN expansion module is located at the end of the CAN-bus, then you
would use an ID-tag having a combined addressing and terminating function. This is
denoted with a "T" for terminating, after the appropriate address such as; 0T, 1T, 2T...
etc. In the application, the same address value as the non-terminated ID-Tag with
equivalent number will be transferred to the application.
Selecting appropriate ID-Tag
•
Check the address number of the module assigned in the application.
•
If the module is located at the end of the CAN-bus, then select the appropriate ID-
Tag denoted with a "T".
N
OTICE
The CAN-bus must not be terminated at the module using an external regular
terminating resistor, due to the fact that terminating is made from within the module by
default or in conjunction with the ID-Tag.
EXAMPLE
If having an expansion module with address 0, the system will denote this one as
[module type]-A0, The letter "A" in the example refers to CAN-bus A.
ID-Tag
ADDR-L
ADDR-H
IQAN module