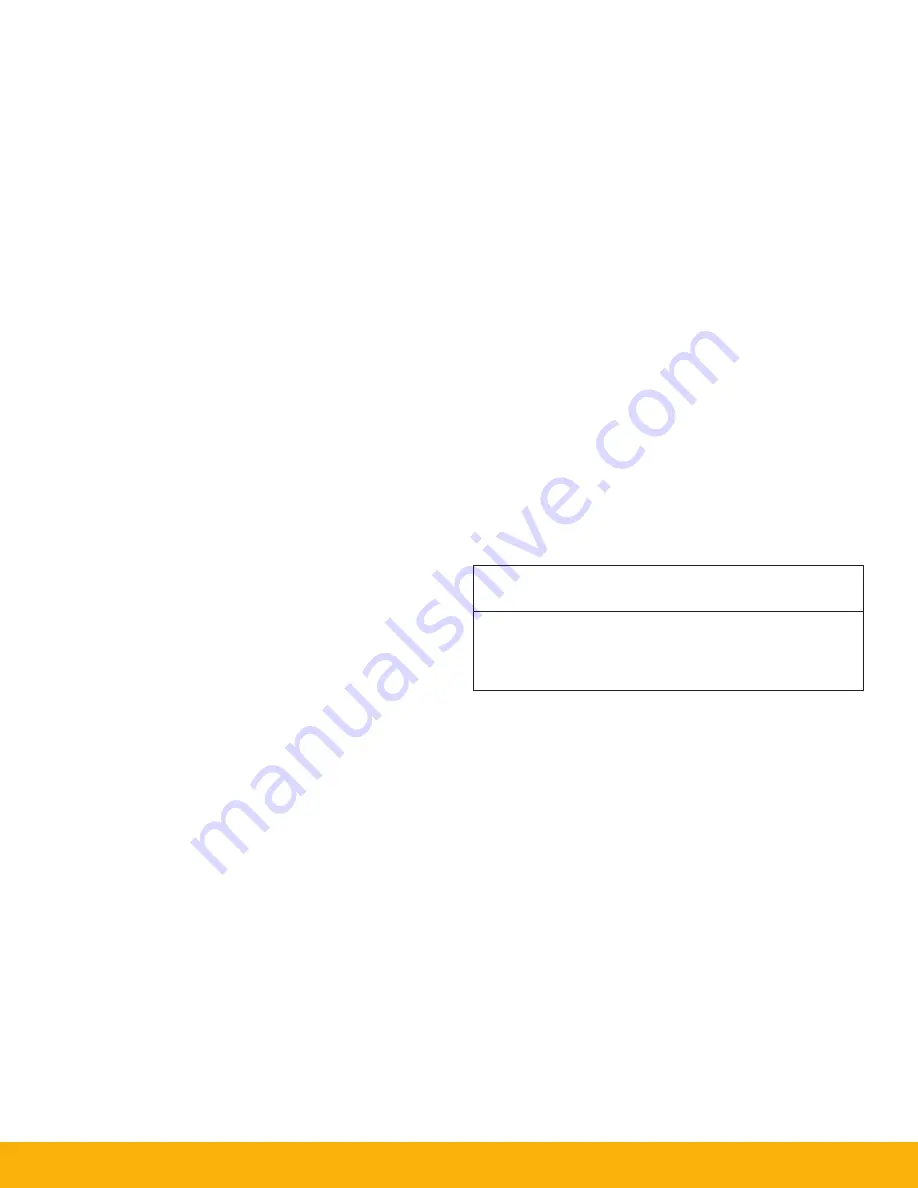
8
Basic Controls – The remote controls panel/enclosure will
contain the blower speed adjusting potentiometer inside the
enclosure, and an on/off switch on the cover. This enclosure
will be attached to the SHM unit at the factory with 50ft of wire.
The cable can be cut down in length at the time of installation if
needed by disconnecting the wire from the remote panel, cut-
ting to length, and reconnecting. Use the wire diagram on page
A2 for reference.
Touchscreen Controls – The remote touchscreen controls
enclosure will contain the touchscreen and terminal blocks for
the wire connections. There are two cables connected to the
remote enclosure that are 100ft each. One is the 24 VDC power
supply and control cable, and the other is a communication
cable. These wires will need to be connected to the rear control
panel of the SHM unit by the customer at the time of installation.
The first wire is the low voltage controls wire that will connect
to the terminal blocks in the back of the SHM unit on +24VDC,
-24VDC, AN2, AN3, AN4, I0, and O0. Use the wire diagram on
page A6 for wire colors and terminal location for landing. The
second wire is a communication wire that needs landed in the
WAGO 222 Lever Wall Nuts. Match the colors of the wires,
brown with brown and black with black.
3.5.5 Machine Interlock Dry Contact
The customer has the option to control the SHM On/Off oper-
ation with the oil mist generating equipment or process. This
will allow the operator to control the SHM with a dry-contact
off another piece of equipment. Refer to the wiring diagrams
in the appendix for wiring of this option and to Section 4 for
Machine Interlock set up on the touchscreen.
Wiring will be terminated to the terminal blocks located in
the rear electrical panel in Figure 1B. When the machine dry
contact is closed, the SHM blower will be on and when the
contact is open, the SHM unit blower will shut down.
Note: A relay coil cannot be connected to the SHM and will
not work for this type of electrical circuit.
3.6 Filter Installation
The primary filter elements are shipped already installed in the
SHM unit. If an after-filter option is selected by the customer,
those filters will be shipped separate of the unit to be mounted
following unit installation at the customer facility. Filters may
removed from the primary filter cabinet by the customer when
delivered to lessen weight, protect them from damage, and ease
unit installation.
Proper removal and installation of each filter type is shown in
figures 5A & 5B.
3.6.1 Installation Procedure for After-Filters
3.6.1.1 Hold Down
Center the filter(s) atop the unit when viewed from the front. If the
unit is two filters deep, then the two after-filters will be butted against
each other in the center of the unit (looking at it from the side) from
front to back just as with the internal filters.
The hold-down brackets are to be placed on top the filters as
shown in Figure 5A balloon #7 and secured down with all-thread
rods, washers and nuts. Tighten nuts using hand tools and be sure
not to over compress the gasket on the bottom side of the after-
filter. Minimal torque should be applied; just enough to cinch down
each bracket so it will not slide around on top of the filter(s). On
units two filters deep, a center bracket is also supplied that runs in
the same direction, it is placed immediately over the seam where
the two filters are butted together.
Larger size unit after-filter setups will be installed in an identical
fashion. The filters will always be installed in-line, directly over the
perforated square cutouts on the top panel.
3.6.1.2 Enclosure
For units with an after-filter cabinet/enclosure, the after-filters must
be installed into this cabinet. The box-shaped after-filter slides into
the cabinet door on the cam-bars. Be sure the filter(s) is pushed all
the way to the back of the cabinet where it will bottom out on a stop.
Rotate the cam-bars upward as illustrated in figure 5B. This will seal
the filter’s top mounted gasket onto the cabinet’s upper tube sheet.
3.7 Drains
All SHM units are supplied with 1-1⁄2˝ FPT drain connections. Use
a 1-1⁄2˝ drain trap or similar to prevent air from being sucked up
through the drain when unit is running.
NOTES: Main drain line should be sufficiently sloped and vented. All
plumbing should conform with all state and local codes.
Appropriate design criteria as provided by a plumb-
ing/mechanical contractor should be utilized to
ensure proper control of drainage from the SHM
Unit.
C A U T I O N
Summary of Contents for SmogHog SHM-C
Page 1: ...SMOG HOG Media Mist Collector Owner s Manual Models SHM C SHM F...
Page 6: ...Page intentionally left blank...
Page 8: ...4 FIGURE 1B SHM Equipment Description 61 10113 FIGURE 1A SHM Equipment Description...
Page 13: ...9 61 10126 FIGURE 4 Remote Panel Touchscreen Connection...
Page 23: ...19 Figure 6 SHM Replacement Parts SHM 11C SHM 11F...
Page 24: ...20 APPENDIX A1 WIRING DIAGRAMS BASIC CONTROLS 04 001682...
Page 25: ...21 REMOTE PANEL BASIC CONTROLS 04 001799 APPENDIX A2...
Page 26: ...22 ONE BLOWER AND CONTROLS 04 001695 APPENDIX A3...
Page 27: ...23 TWO BLOWER AND CONTROLS 04 001696 APPENDIX A4...
Page 28: ...24 THREE BLOWER AND CONTROLS 04 001697 APPENDIX A5...
Page 29: ...25 REMOTE PANEL TOUCH CONTROLS 04 001802 APPENDIX A6...
Page 30: ...26 ONE BLOWER AND REMOTE CONTROLS 04 001798 APPENDIX A7...
Page 31: ...27 TWO BLOWER AND REMOTE CONTROLS 04 001797 APPENDIX A8...
Page 32: ...28 THREE BLOWER AND REMOTE CONTROLS 04 001796 APPENDIX A9...
Page 33: ...29 575 480 TRANSFORMER 04 001717 APPENDIX A10...
Page 36: ...32...
Page 37: ...33...