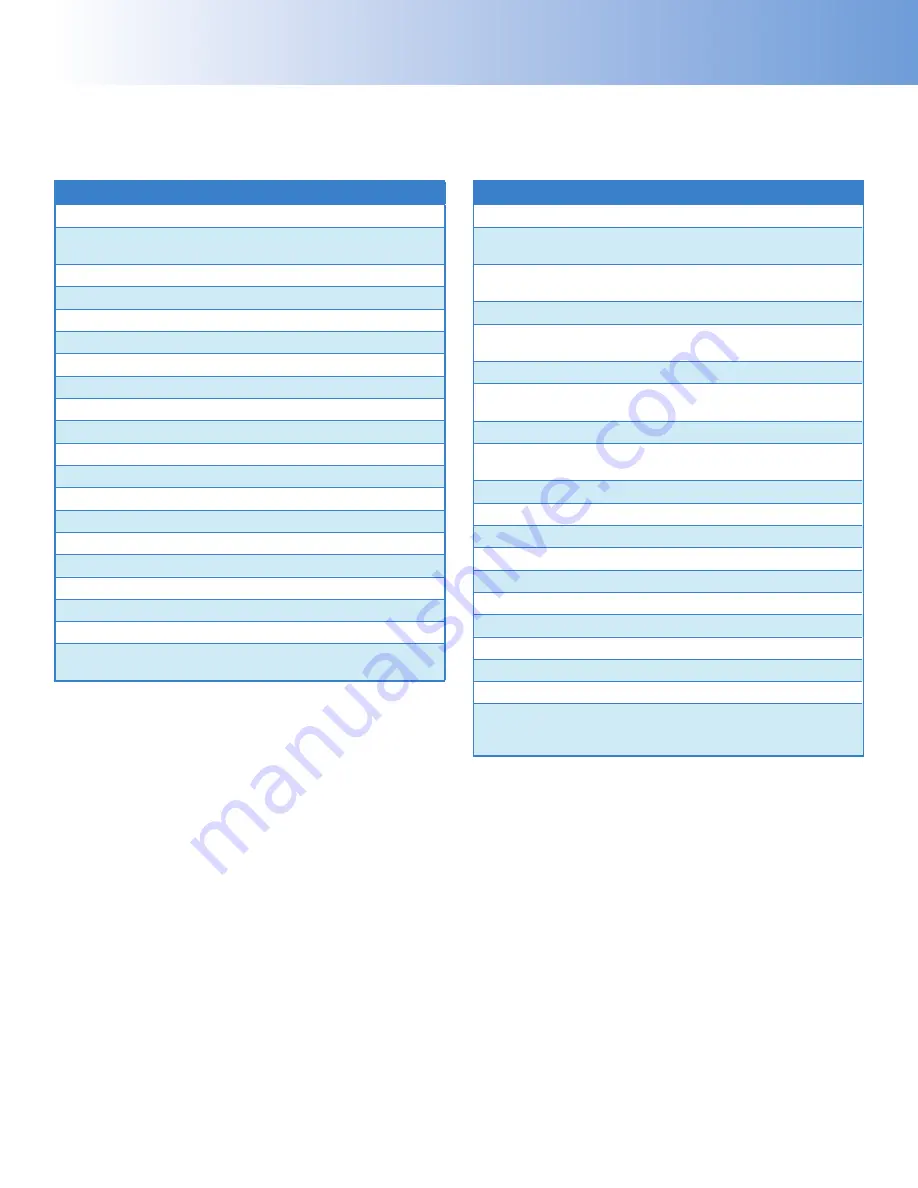
4838 Reactor Controller
13
A sample program to heat to 200 °C as fast a pos-
sible, hold for 2-hrs, and come back down as quickly
as possible:
Variable
Value
Meaning
ptrn
00
Pattern 0
SP00
200
Setpoint of 200 °C (first step is
a soak by default)
tI00
00:00
Move setpoint to 200 °C im-
mediately
SP01
200
Setpoint of 200 °C
tI01
01:00
Ramp from 200°C to 200 °C
over 1-hrs *
SP02
200
Setpoint of 200 °C
tI02
02:00
Ramp from 200C to 200 °C over
2-hrs **
SP03
25
Setpoint of 25 °C
tI03
00:00
Ramp to setpoint immediate-
ly***
SP04
25
Setpoint of 25 °C
tI04
00:00
SP05
25
Setpoint of 25 °C
tI05
00:00
SP06
25
Setpoint of 25 °C
tI06
00:00
SP07
25
Setpoint of 25 °C
tI07
00:00
PSy0
3
Execute steps 0-3 only****
CyC0
0
Do not re-cycle program
Lin0
off
Do not execute another pro-
gram upon completion of this
program
* The physical system will take some time to go from
room temp to 200 °C. Step 01 is presented as a “heat
up” step. The time value in this step should be ad-
justed after the fi rst run is complete and the operator
knows the expected heat up time.
** It is useful to keep this step 02 separate from step
01 so you can adjust step 01 to match the heat up
time.
*** The time is zero, making this a step function in-
stead of a ramp.
**** Steps 4-7 are not executed here.
Appendix: sample programs
A sample program to ramp from 25 °C to 250 °C in
2-hrs:
Variable Value Meaning
ptrn
00
Pattern 0
SP00
25
Setpoint of 25 ºC (first step is a
soak by default)
tI00
00:01
Hold for 1-min
SP01
250
Setpoint of 250 °C
tI01
02:00
Ramp to setpoint in 2 hrs
SP02
250
Setpoint of 250 °C
tI02
00:40
Ramp to setpoint in 40-min*
SP03
25
Setpoint of 250 °C
tI03
00:00
Ramp to setpoint immediately**
SP04
25
Setpoint of 25 °C
tI04
00:00
SP05
25
Setpoint of 25 °C
tI05
00:00
SP06
25
Setpoint of 25 °C
tI06
00:00
SP07
25
Setpoint of 25 °C
tI07
00:00
PSy0
3
Execute steps 0-3 only***
CyC0
0
Do not re-cycle program
Lin0
off
Do not execute another program
upon completion
* The beginning and fi nal setpoint are equal, making
this a soak step.
** The time is zero, making this a step function in-
stead of a ramp.
*** Steps 4-7 are not executed here.
**** The SP_0 vaue must be higher than the initial
temperature (PV) of the reactor or the program will
not initiate correctly.