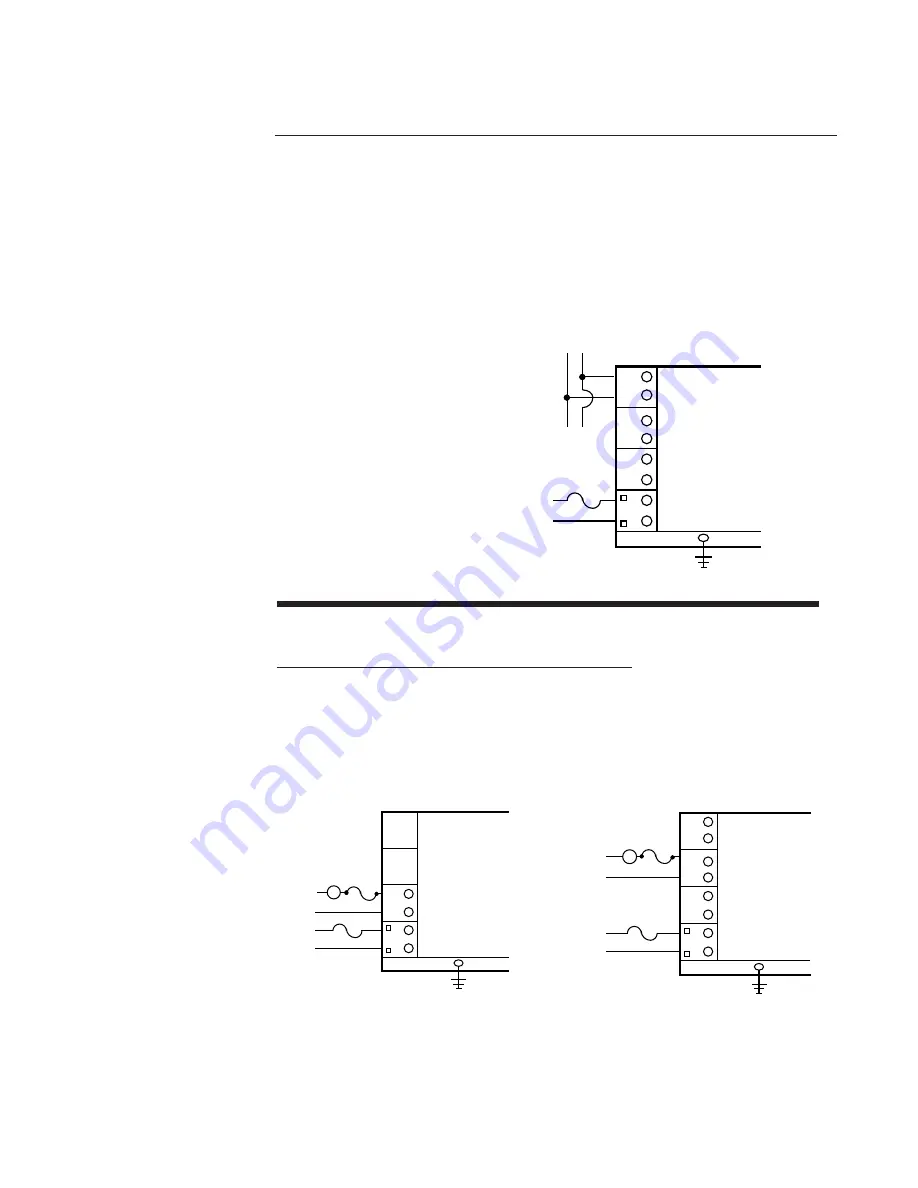
P
AGE
18
B
A
GROUND
RELAY A
D
C
INPUT
POWER
LOAD
L2
L1
Rear View
FIGURE 2-13
Alternate Remote Digital Communications RS 485 Terminals G & H (Optional)
If the communications network continues on to other units, connect the shields together, but
not to the instrument. A terminating resistor should be installed at the terminals of the last
instrument in the loop. The shield should be grounded at the computer or the
convertor box , if used. See the Protocol Manual (Form 2878) for more details on the use of
the digital communications option.
Output Connections 2.4
FIGURE 2-14
Relay Output
Connections are made to relay A as illustrated below. Connect relay(s) B & C (if present) in
the same manner. Relay contacts are rated at 5 amp Resistive load 115 VAC.
Terminals G & H are
used for communications when the
model number is 82XY04X,
82XY06X where
X = any valid number and
Y = 3, 4, or 5.
Use when Second Output is 4-20mA.
B
A
GROUND
D
C
INPUT
POWER
F
E
H
G
Rear View
Output 3 Must Be 0
From Host
Computer
To Other
Instruments
DIGITAL COMMUNICATIONS
CONNECTIONS - TERMINALS G & H
B
A
GROUND
D
C
INPUT
POWER
F
E
H
G
L2
L1
LOAD
Rear View
RELAY B