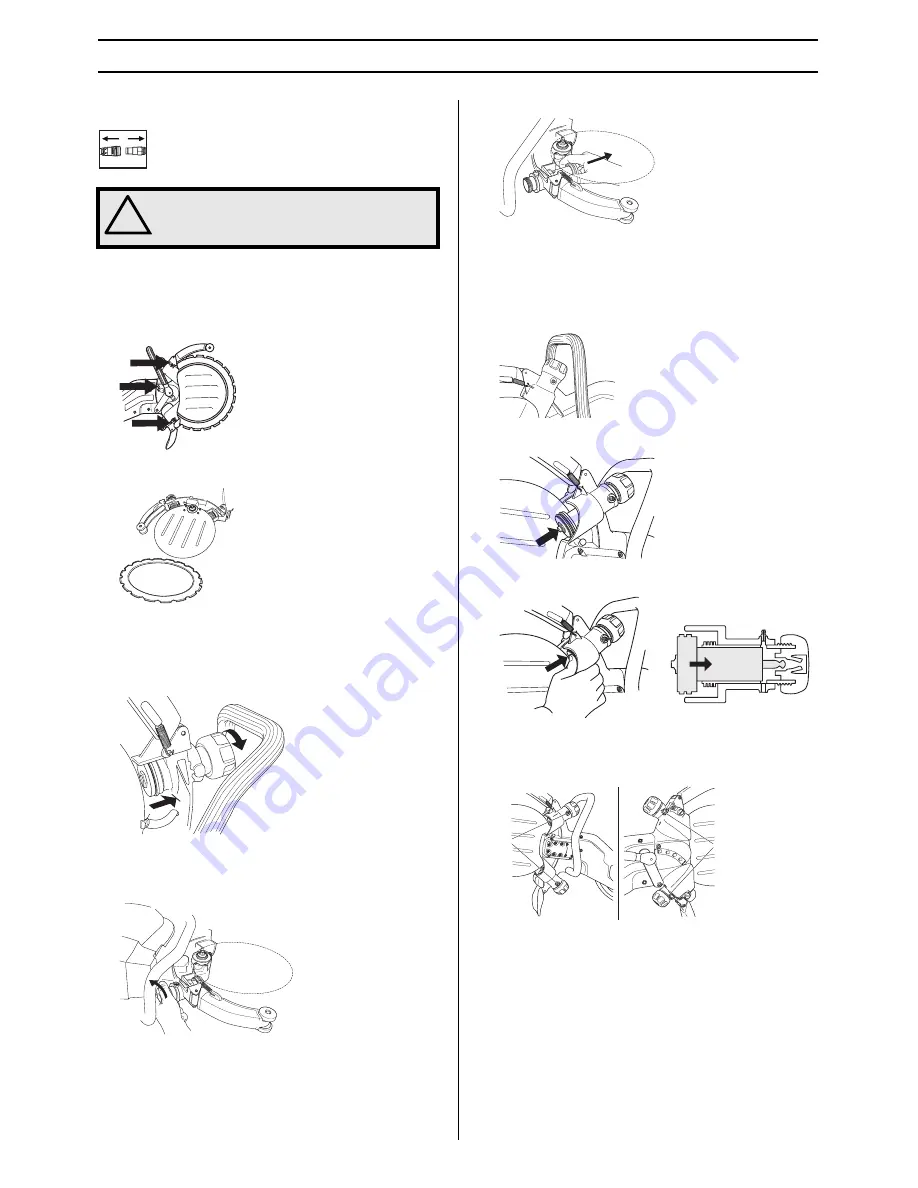
14 –
English
MAINTENANCE
Maintenance
Dismantling the complete guide
roller
•
Remove the support roller cover.
•
Lift off the blade.
•
Unscrew the knob.
First turn the knob a few turns until you feel a resistance.
The guide roller then follows the knob out and stops when
it feels a resistance.
The guide roller is pressed into the knob. In order to loosen
the guide roller, you need to continue turning the knob until it
loosens completely.
•
The guide roller can now be pulled out of the chassis
Assembling the complete guide
roller
•
Screw the knob until it bottoms, and then loosen the knob
2 turns.
•
Insert the guide roller in the chassis
•
Now press the guide roller into the knob.
Lubricate the guide roller’s sleeve using grease. Fit the
grease gun on the grease nipples (A) and pump in grease
until clean grease emerges from the overflow hole (B).
•
Fit the blade. See the heading Fitting the blade.
Important notes:
•
The support rollers do not drive the blade.
•
Incorrect adjustment can result in damage to the blade.
•
If the blade rotates slowly or stops, stop cutting
immediately and trouble shoot.
!
WARNING! Inspection and/or maintenance
should be carried out with the hydraulic
hoses disconnected.
A
B
Summary of Contents for K3600 MKII
Page 21: ......
Page 22: ... z x 6r z x 6r ...
Page 23: ......
Page 24: ... z x 6r 2004 12 22 z x 6r 1088929 26 www partner industrial com ...