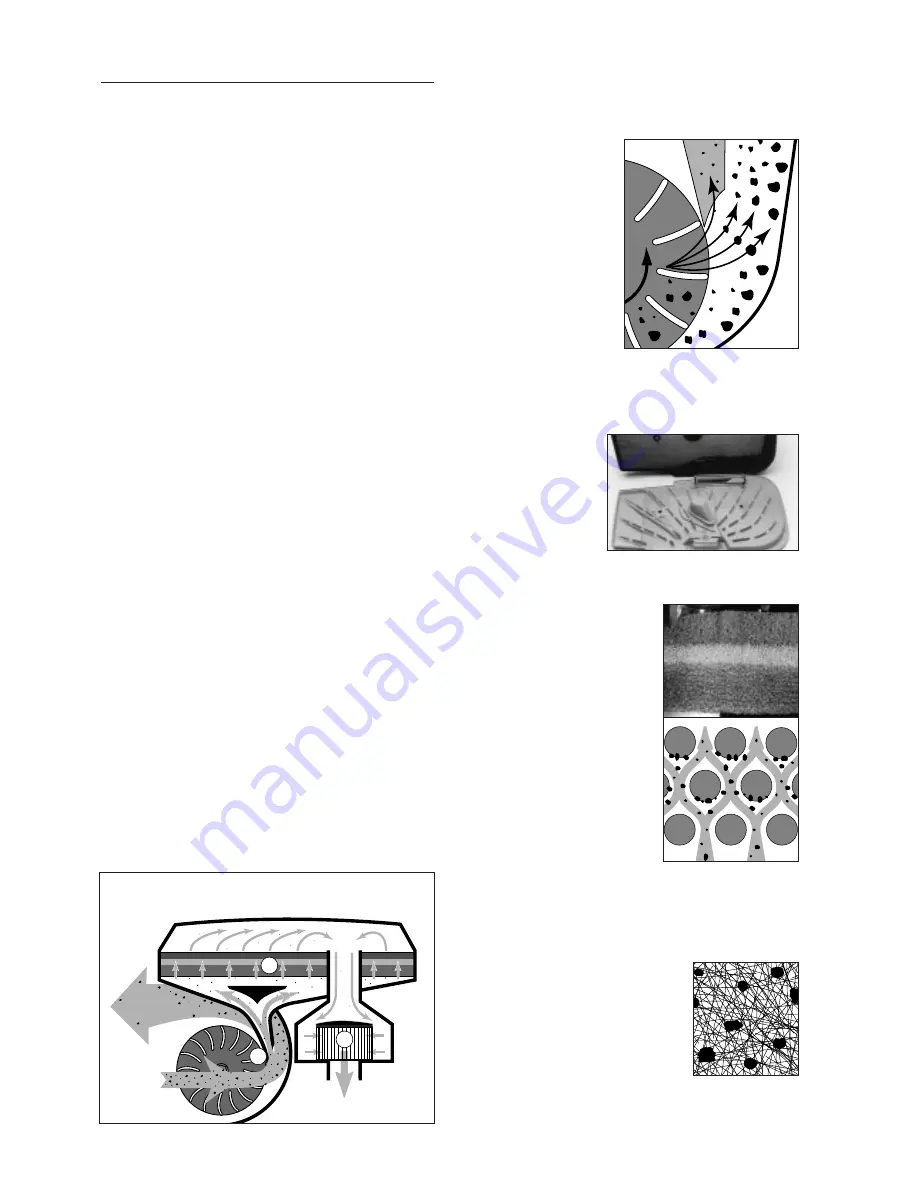
1. Centrifugal force
is the first stage in cleaning the
intake air of the K950/K1250 Active. Centrifugal cleaning
was previously only used on larger engines in dusty
environments, for example for construction machines
(cyclone air filter).
The fan vanes on
the flywheel supply the
cylinder with cool air at
the same time as they act
as the active part of the
centrifugal filtering sys-
tem for the engine’s in-
take air. An intake nozzle
is fitted just beside the
fan vanes. Under centri-
fugal force, the larger
particles do not follow
the curved current of air
to the nozzle but are in-
stead thrown against the outside of the nozzle. Only very
small dust particles will be able to follow the current of
air leading into the intake. Tests show that up to 80% of
all dust is removed by the centrifugal cleaning process.
2. The foam filter
is the next stage of
separation in the filtra-
tion process. This filter
covers the housing’s
entire surface, thus
offering a filter surface
of no less than 3.5 dm
2
(K950), 3.7 dm
2
(K1250). The filter’s base distributes air
across the entire filter surface, so the filter performs
uniformly.
The filter is immersed in oil
and is made up of three layers,
each intended for a different
pore size.
Inside the filter, the air flows
through a structure pretty much
like a labyrinth. Dust particles
which strike against the filter
sides do not bounce off but
instead fasten to the sticky oily
surface. A dry foam filter offers
far less efficient cleaning perfor-
mance than an oil-soaked filter.
An oiled foam filter is by far
the most effective filter for clea-
ning of stone dust, since the
entire filter volume is used as a
“dust trap”, not just the surface. The total dust-absor-
bing filter area is accordingly enormous. The foam filter
absorbs about 95% of the total dust volume remaining
after centrifugal filtering. It can be washed clean and
must be oiled at each service.
3. The paper filter
deals with the
small amount of dust particles which,
more by chance than anything else,
may manage to slip through the foam
filter. Only a tiny amount of extremely
small dust particles will ever get as
far as the paper filter. The filter’s
dense network of cellulose fibres
traps all incoming particles. The paper filter also serves
as a protective barrier during filter services. The paper
filter should be changed at every service.
2
Filter System
Cutting in stone and concrete generates tiny dust parti-
cles which must at all costs be prevented from entering
the engine. The design of the air filter and its maintenan-
ce are the two most important factors governing the ser-
vice life of the cutter. Designing a good air filter system
is a matter of balancing effective filtering with long ser-
vice intervals.
The development of more efficient filters has improved
air-cleaning performance, but service intervals have by
tradition still been inconveniently short in cutting machi-
nes. Machine rental firms inherit the problems caused by
customers who do not carry out the necessary service
during the rental period, or are faced with the cost of tra-
velling frequently to various work-sites to carry out the
necessary service.
Dust
consists of extremely fine particles, generally so
small that the individual particle cannot easily be disting-
uished by the naked eye but which in larger quantities
can be seen as a cloud of dust. The stone or concrete
dust which generally results from cutting operations
generates the most damaging kind of particles for an
engine’s sliding or rotating components. Together with
oil, this dust forms a perfect grinding paste which quick-
ly wears down pistons, piston rings, cylinder walls and
engine bearings once it penetrates an engine.
We generally measure dust particles in µm (1 µm =
0.001 mm), thousandths of a millimetre, and the particle
sizes which are dealt with by the filter system generally
measure between 50 µm and 5 µm. (It takes roughly 2
minutes for a stone particle measuring 10 µm to fall 1 m
in wind-still conditions.)
One physical characteristic which is vital to the func-
tion of the Partner Active Air Filtration system is the
behaviour of dust particles in air currents depending on
particle size:
A small particle is more easily affected by a current of
air than a larger particle
.
The reason for this is that small particles have a larger
surface in relation to their mass. A small particle can the-
refore be steered and guided more easily by a current of
air while a larger particle succumbs to centrifugal force
or the force of gravity.
Partner Active Air Filtration
is a filter system which
effectively cleans the air entering the engine in three
separate stages, utilising three different cleaning princi-
ples. The most immediate practical benefit of Active Air
Filtration is that the service intervals are far longer com-
pared to previous systems.
In
To carburettor
Cylinder
cooling air
2
3
1
Air filtration principle