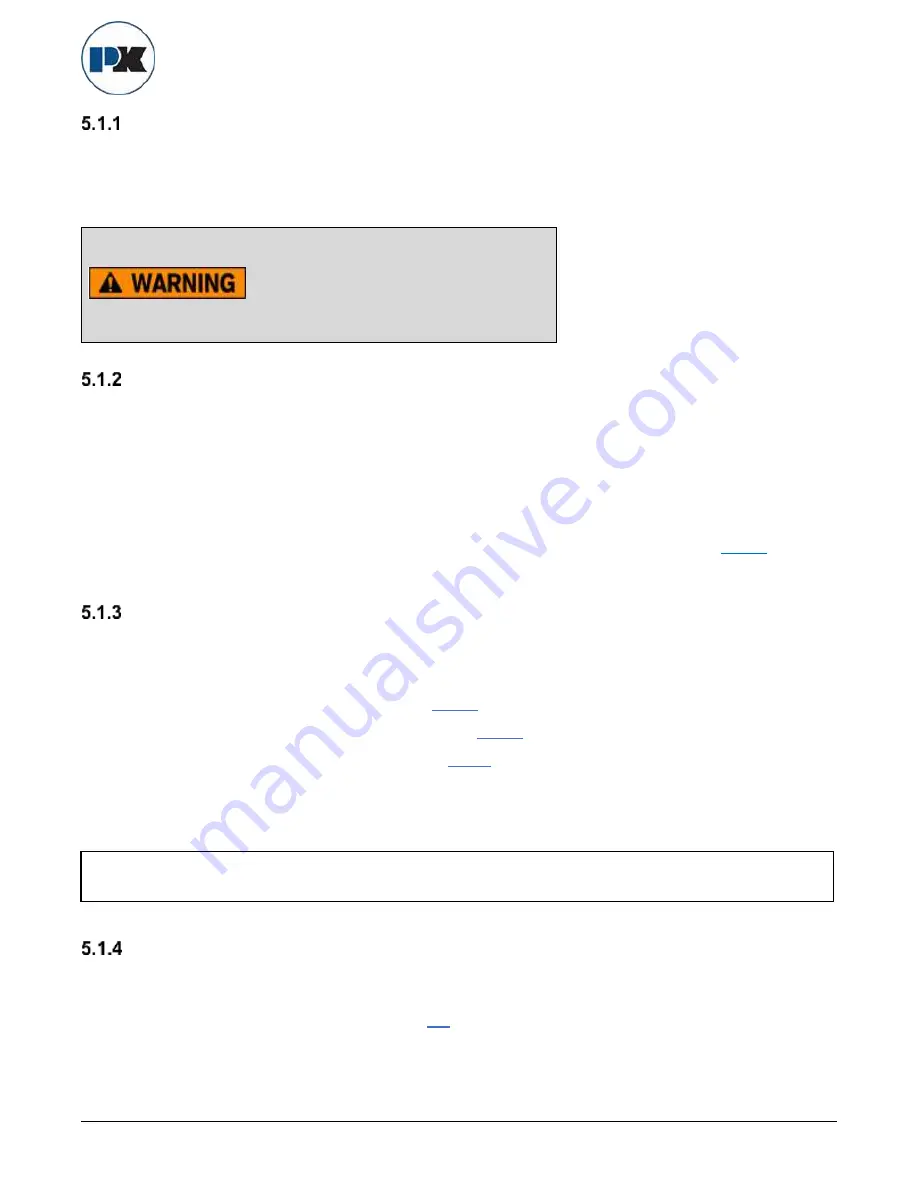
P-K Storm
TM
Gas Fired Boiler
Technical Service 1.877.728.5351
Revised: June 26, 2020
Released: June 26, 2020
©
Patterson-Kelley 2020
All Rights Reserved.
2691000273 P-K Storm ST2500-ST4000
Installation and Owners Manual Rev A.docx
Page 53
Daily
Observe operating temperature and general conditions. Make sure that the flow of combustion and
intake air to the appliance is not obstructed. Determine the cause of any service codes or lockouts on
the NURO
®
touchscreen display. Observe any unusual noises or operating conditions and make the
necessary corrections. Notify responsible individuals for required corrective action or repair.
Weekly
Observe the conditions of the main flame. A normal high fire flame is mostly blue, though the refractory
in the rear of the heat exchanger will glow an orange red color. A normal low fire flame is also blue.
The refractory may not show any orange-red color at low fire. Never
attempt to adjust the flame “by
eye”. The correct flame/combustion is dependent on the air and gas adjustment.
Correct air adjustment is essential to the efficient operation of this appliance. Ensure that the flow of
combustion and ventilation air is not obstructed. If an adjustment in the combustion appears
necessary, the flue gas composition should be checked with a combustion analyzer and compared to
the values stated in the Combustion Setup and Adjustment combustion settings table in
If an
adjustment to the combustion is necessary, call a qualified and knowledgeable installer or service
agency that has been trained on the Patterson-Kelley appliance.
Monthly
1.
Press the “Info” button on the NURO
®
touchscreen to load the Information Screen and scroll
down to view the flame signal measured in Volts. Typical flame signals should read between 8-
25V.
2. Test the low water level cut-off. Refer to
3. Test the manual reset high-temp limit. Refer to
4. Test the low gas pressure switch. Refer to
5. Test operating temperature controls by reducing or increasing temperature settings as
necessary to check burner operation.
6. Check the combustion chamber condensate drain piping for leaks or obstructions.
Semi-Annually
In addition to the recommended monthly service:
1. Check the burner for any accumulated dust or lint. You may clean the burner using only water to
remove accumulated material. Refer to
2. Inspect burner for any signs of deterioration or corrosion. Replace immediately if deterioration
or corrosion is evident.
Check daily to be sure that the
immediate area around the boiler or
water heater is free and clear of any
combustible materials, including
flammable vapors and liquids.
NOTICE!
Installation and service must be performed by a qualified installer or service agency that
has been trained on the appliance.