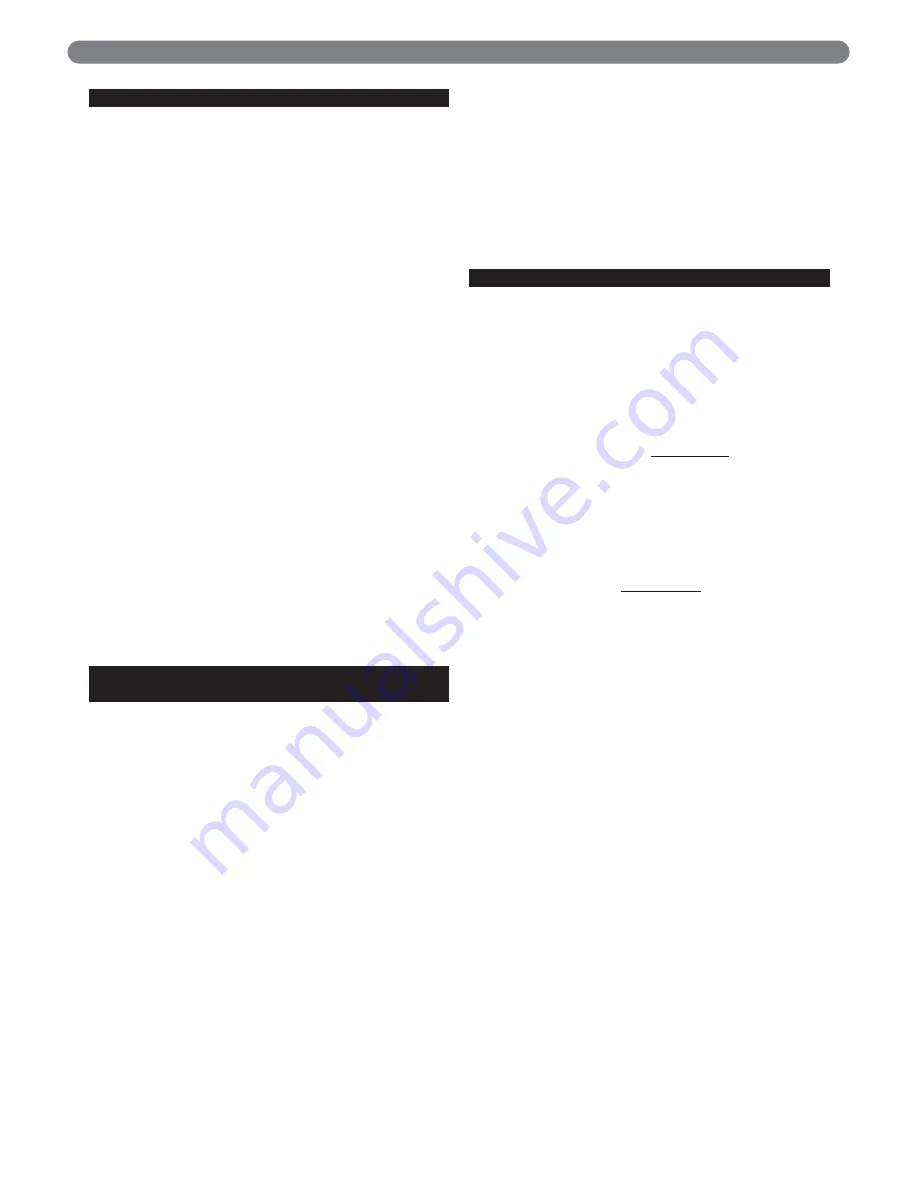
26
B. CONTROL DESCRIPTIONS
See Figure 6.1 in Section 6 (Electrical) for locations of
these devices.
1. FLAME ROLL-OUT SAFETY SHUT-OFF SWITCH
(FLAME ROLL-OUT SWITCH) – A thermally
activated switch located between the first burner
from the left and the manifold bracket. The flame
roll-out safety shut-off switch will sense excessive
temperature caused by continued flame roll-out and
shut down main burner gas. This is a non-recycling
switch that must be replaced once it has been
activated and the cause of the roll-out eliminated.
2. PRESSURE SWITCH – A pressure sensing device
that is located in the jacket vestibule. This control
senses a suction pressure when fan is energized on a
call for heat. Switch contacts close allowing control
circuit to energize ignition system.
3. LIMIT (AQUASTAT) – A thermally activated,
manually adjustable switch located on the left side of
the boiler, towards the top and rear. The temperature
sensing element is placed in the supply and will shut
down main burner gas if the supply water exceeds
the preset temperature limit. This is a recycling switch
that will automatically reset when the supply water
falls below the preset temperature.
4. LOW WATER CUT-OFF (FOR GRAVITY SYSTEMS
OR HOT WATER BOILERS INSTALLED ABOVE
RADIATION LEVEL) – A level-sensing device (float
or probe) located in supply piping near the boiler. If
water level in the system drops below the control’s
position, it will shut down main burner gas. The
control will automatically reset once the water level
rises above its position.
C. ADJUSTMENT OF GAS PRESSURE
REGULATOR
1. Connect a manometer to 1/8 N.P.T. tapping on gas
manifold, set manifold pressure as follows for various
gases.
a. Natural Gas . . . . . . . . . .3.5
″
W.C. (0.9 kPa)
b. LP Gas . . . . . . . . . . . . .10.0
″
W.C. (2.5 kPa)
2. To adjust gas pressure, turn adjusting screw of gas
pressure regulator counterclockwise to decrease
pressure, clockwise to increase pressure. Refer to
Figure 7.2 for location of gas pressure regulator.
Replace the cap screw when adjustment is complete.
3. In no case should the final manifold pressure vary
more than ±0.3 inches water column (0.07 kPa)
from the above specified pressures. Any necessary
major changes in the flow should be made by
changing the size of the burner orifice spuds.
4. When adjustment is complete, turn off boiler, gas
flow and electricity to boiler. Remove manometer
connection from valve and plug tapping with plug
provided. Turn utilities back on and resume
checkout.
D. CHECKING BURNER INPUT
1. Refer to rating label mounted on the jacket top panel
to obtain the rated BTU per hour input. In no case
shall the input to the boiler exceed the value shown
on the rating label.
2. Check input by use of the following formula
(PB Heat suggests reading meter for 2 Cu.Ft.
[0.0566 cubic meter]):
U.S. Customary Units:
Input (BTU/Hr.)= 3600 x F x H
T
Where:
3600 – Seconds per hour
F – Cubic Feet of Gas Registered on Meter
H – Heat Value of Gas in BTU/Cubic Feet
T – Time in Seconds the Meter is Read
SI Metric Units
Input (kW)= 3600 x F x H
T x 3.6
Where:
3600 – Seconds per hour
3.6 – Megajoule (MJ) per kilowatt hour (kwhr)
F – Cubic Meters of Gas Registered on Meter
H – Heating Value of Gas in MJ/Cubic Meter
T – Time in Seconds the Meter is Read
3. As an alternative, use Table 7.1a and 7.1b. Use the
heating value provided by gas supplier. Use a
stopwatch to record the time it takes for 2 cubic feet
(0.0566 cubic meter) of gas to pass through the
meter. Read across and down to determine rate.
START-UP PROCEDURES
Summary of Contents for DE-03
Page 1: ...DE Boilers Series Gas Installation Operation Maintenance Manual ...
Page 26: ...START UP PROCEDURES Figure 7 3 Operating Instructions 24 ...
Page 27: ...25 Figure 7 4 Operating Instructions START UP PROCEDURES ...
Page 32: ...30 TROUBLESHOOTING Figure 8 1 Procedure For Measuring Fan Suction Pressure SEE TABLE 7 ...
Page 39: ...37 This page intentionally left blank ...
Page 42: ...40 REPAIR PARTS Figure 11 2 Base Burners Manifold ...