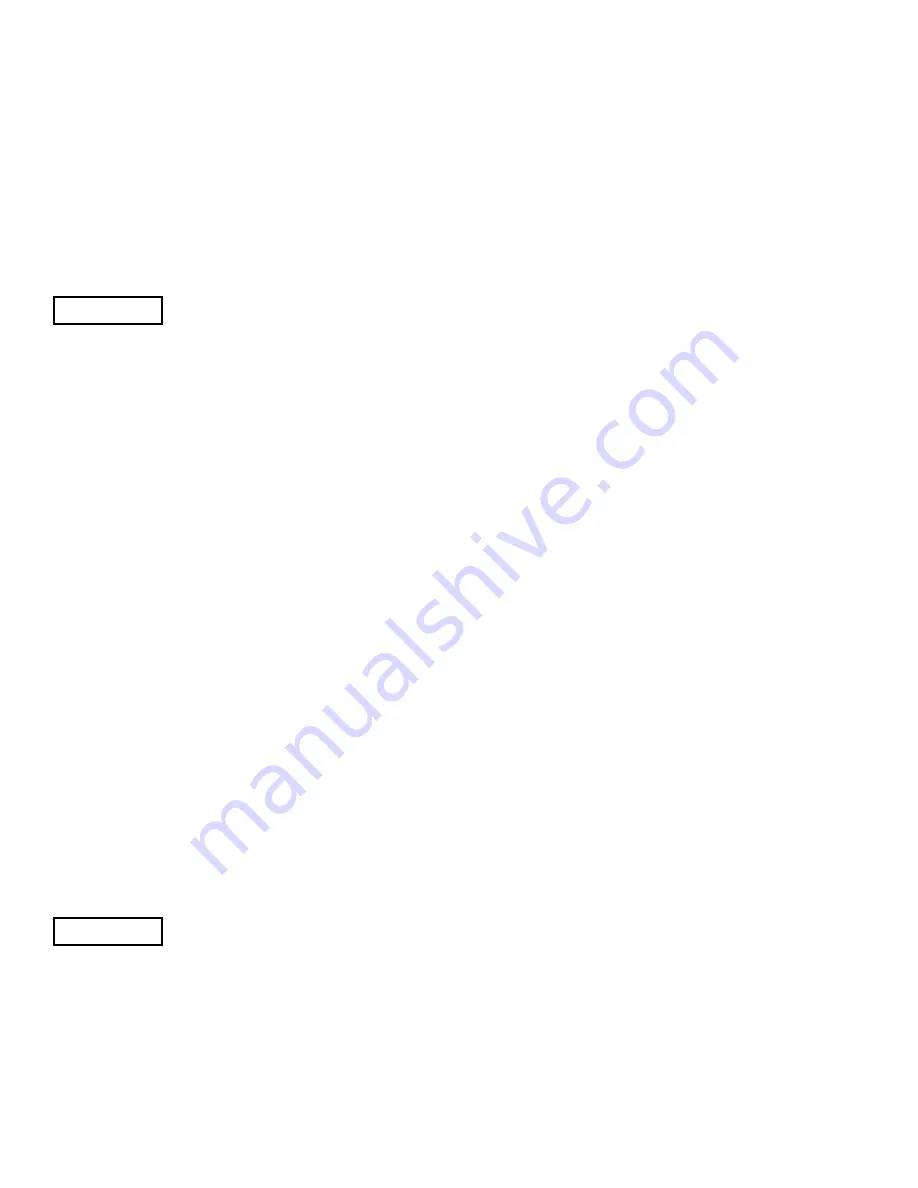
PUMP LUBRICATION:
This unit is provided with a
lifetime charge of lubricant for lower sleeve bearings
reservoired in the hanger pipe sections. The ball
thrust bearing and upper bronze guide bearing are
lubricated by the grease cup provided on the floor of
the motor pedestal. The is grease-filled at the
factory and should be given a half turn before
starting the pump. Keep this cup filled with a good
Check the following items before starting unit.
Due to automatic switch opera-
tion of sump pumps, tie the
main disconnect switch open or remove fuses from
main lines before attempting lubrication, mechanical
and electrical examinations, or repairs. Attach a card
“DO NOT CLOSE SWITCH – PUMP REPAIR IN
PROGRESS”. Disregard of this warning may result
in serious personal injury or death.
1. Be sure the unit is lubricated as directed under
Lubrication.
2. Turn the shaft by hand to see that it rotates
freely. Failure of the shaft to turn freely may be
caused by pump bearings being too tight, dirt
clogging pump or jamming motor armature, or
impeller rubbing in pump casing due to improper
thrust adjustment.
3. See that voltage and frequency on motor
nameplate are the same as service provided.
4. See that wires are connected according to motor
manufacturer’s instructions for voltage and phase
used.
5. See that the proper fuses are installed.
6. See that the piping connections have been made
as directed under installation.
7. Check the float-switch mechanism for regulation.
Due to automatic switch opera-
tion
of
sump
pumps,
tie
the
main disconnect switch open or remove fuses from
main lines before attempting lubrication, mechanical
and electrical examinations, or repairs. Attach a card
“DO NOT CLOSE SWITCH – PUMP REPAIR IN
PROGRESS”. Disregard of this warning may result
in serious personal injury or death.
INSPECTION:
To insure the best operation of the
unit make a systematic inspection at least once a
week. Watch the following:
grade of a No. 2 or 3 grease, and turn the cup down
two or three turns approximately every week or two,
frequency depending upon severity of pump service.
MOTOR LUBRICATION:
Lubricate the motor accord-
ing to directions given by the motor instruction label,
but avoid over-lubrication especially of the top
bearing which may overflow into the windings.
OPERATION
8. Be sure the basin is clean and system flushed as
directed.
WARNING
9. See that the unit is firmly anchored and in a
vertical position.
STARTING PUMP:
IF the unit is of the cord and
plug type, insert the plug into the outlet provided.
Otherwise, close the manual disconnect switch.
Remember, the pump will operate only when the
float switch is closed (basin is filled).
AFTER STARTING NOTE THE FOLLOWING:
1. Note operation of the float switch. Observe a
complete start-stop cycle for freedom of float rod and
location of buttons. See that float switch closes
and opens properly as basin fills and is emptied by
the pump. The operation of this unit should be
absolutely automatic.
2. See that all pipe connections are tight.
3. See that bearings of motor do not overheat.
4. See that pump and motor rotate in a clockwise
direction looking down on the motor.
5. Observe operation of pump closely for the first
day and at regular intervals for ten days. A new
machine is frequently stiff and tight, and therefore
the unit should be watched to note performance.
(Refer to Inspection under Maintenance.)
MAINTENANCE
Sticking: See that the pump does not stand idle for
very long periods. If necessary start pump manually
to see that the shaft is free.
WARNING
Automatic equipment: Check frequency of starts and
stops to see that unit is properly regulated. Check
contacts of switches, cleaning them and applying
Vaseline if they show signs of burning. If contacts
are badly burnt, replace the switch before serious
consequences result.
6
2899982