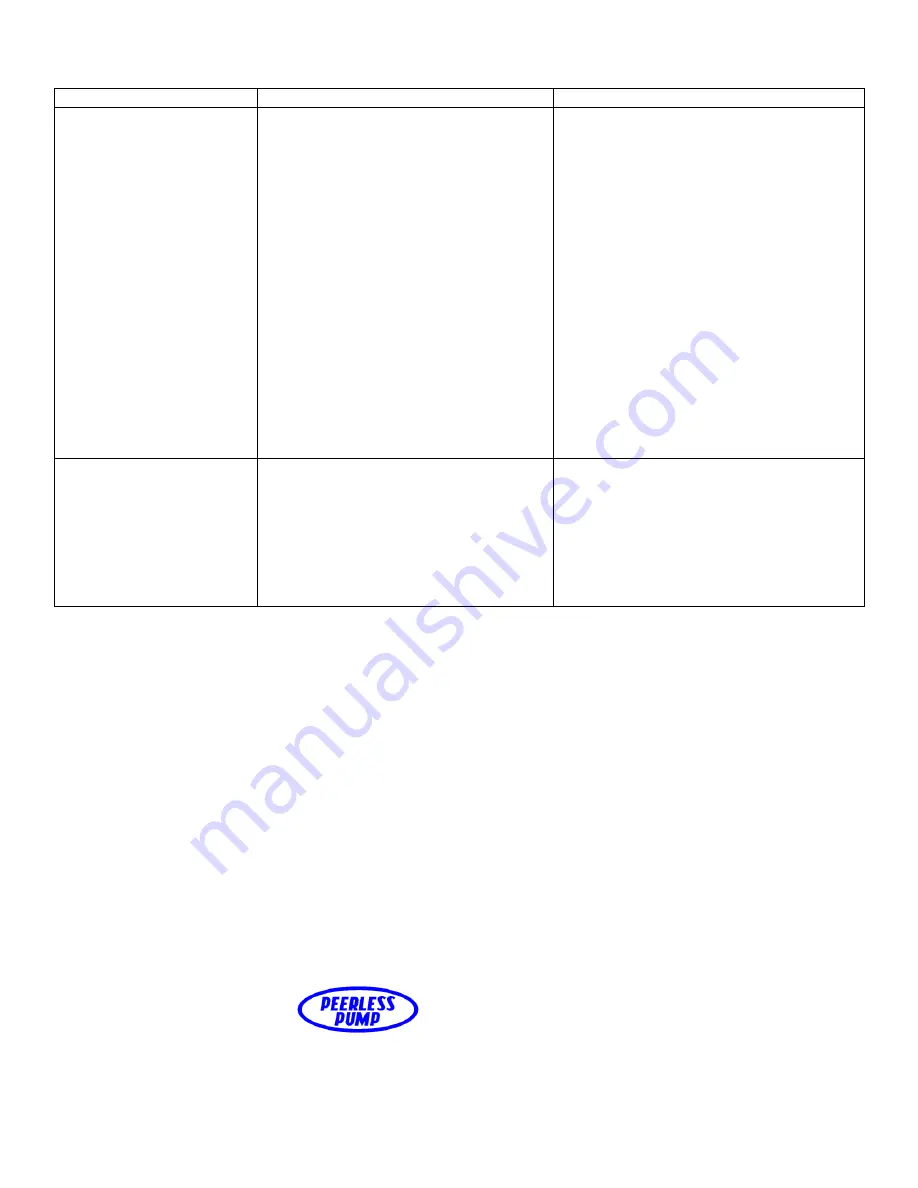
TABLE V (continued)
TROUBLES
TROUBLE PROBABLE
CAUSE
REMEDY
Overload on driver
Pump speed high.
Total head lower than rating.
Tight packing.
Liquid is of higher specific gravity or
Viscosity than rating.
Mechanical trouble of pump or driver.
Motor voltage higher than name plate rating
will cause the motor to run faster. Either
reduce motor voltage or trim impeller
diameter. On other drives, reduce speed if
possible. If speed reduction not realized,
trim impeller diameter.**
Check suction and discharge pressures and
determine the total dynamic head. If TDH
lower than ratings, throttle discharge to rated
TDH or, if this is not possible, reduce
impeller diameter.**
Stop pump – following proper repacking
procedure. Check for scored sleeve; and for
sleeve run-out if packing wears rapidly. Replace
sleeve and packing as required.
Check with Peerless Pump Company distributor
to determine If a larger motor is required.
See if pump and motor turn freely. Check
impeller fit, shaft straightness and ball
bearings.
Pump vibrates or is noisy
Driver unbalanced.
Misalignment
Cracked foundation.
Worn ball bearings.
Disconnect driver and operate it alone. Check
pump for large pieces of debris, such as wood,
rags, etc.
Realign pumping unit.
Replace foundation.
Replace bearings. Check lubricants for proper
Grade. Check pump alignment. Check for
Condensation on water cooled bearings.
**Always obtain new trim diameter from Peerless Pump Company representative.
3-6.SPARE PARTS. To keep delays to a minimum when
pump repairs are required, we suggest that the following
spare parts be stocked. The number of each part
required depends upon the application. For a minimum,
we
recommend:
(A) One set of inboard bearings.
(B) One set of outboard bearings.
(C) One set of shaft sleeves.
(D) One set of case wear rings
(E) One set impeller wear rings.
(F) In some instances, and entire rotating element
should be stocked.
3-7. To obtain quick and accurate service when ordering
spare parts, provide the following information:
(A) Pump size and type as noted on nameplate.
(B) Pump serial number as noted on nameplate.
(C) The name and number of the parts as shown on
the sectional drawings.
(D) Quantity required of each item.
Aid may be obtained from the Peerless representative,
or an authorized distributor, for planning an adequate
supply of spare parts.
NOTICE: Materials of construction, specifications, dimensions, design features, and application information, where shown
in this bulletin, are subject and/or modification without notice by Peerless Pump Company at their option.
Peerless Pump Company
P.O. Box 7026 – Indianapolis, IN 46207-7026
Phone: (317) 925-9661- Fax: (317) 924-7388
Bulletin No. 2883819 Rev. 10-04
12