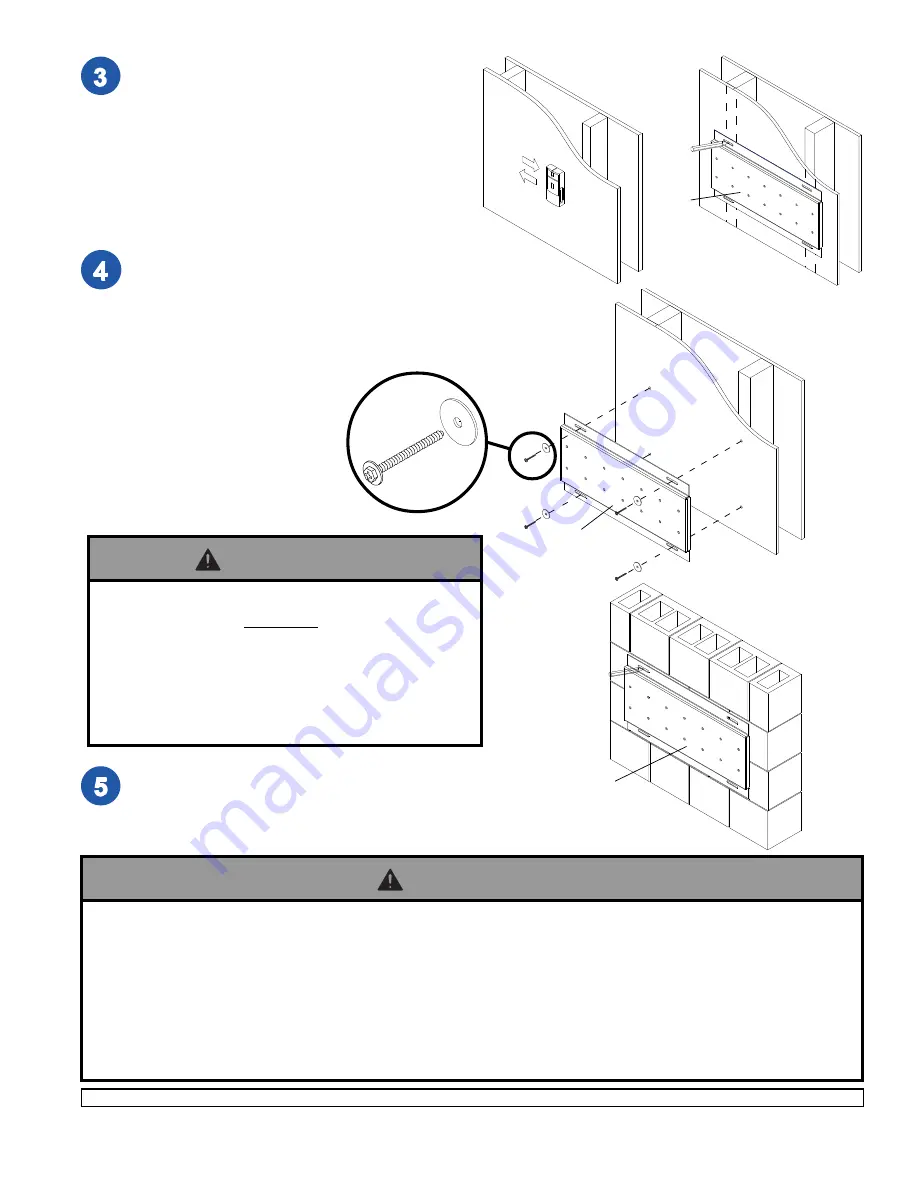
3 of 6
ISSUED: 07-03-02 SHEET #: 200-9386-6 01-25-11
Visit the Peerless Web Site at www.peerlessindustries.com
For customer service call 1-800-729-0307 or 708-865-8870.
L
O
N
L
Use stud finder to locate stud centers. Place wall plate
(
L
) on wall as template, level wall plate and mark center
of studs with pencil. The wall plate can be mounted on
16" centers. When mounted to 16" studs, the wall plate
can be shifted 4" left or right of center if desired.
Note: Hardware provided is for attachment of plasma mount
through standard thickness drywall or plaster into wood studs.
Installers are responsible to provide hardware for other types of
mounting situations.
For Wood Stud Walls
drill four 5/32" (4 mm) dia. holes 2 1/2" (65
mm) deep. Attach wall plate (
L
) using four #14 x 2.5" (6 mm x 65
mm) wood screws and washers (
O
&
N
).
CONCRETE/CINDER BLOCK INSTALLATION
Place wall plate (
L
) on wall as template, level
wall plate and mark center of slots with pencil.
L
• Tighten wood screws so that wall plate is firmly
attached, but do not overtighten. Overtightening can
damage screws, greatly reducing their holding power.
• Never tighten in excess of 80 in • lb (9 N.M.).
• Make sure that mounting screws are anchored into the
center of the studs. The use of an "edge to edge" stud
finder is highly recommended.
WARNING
• When installing Peerless wall mounts on cinder block, verify that you have a minimum of 1 5/8" of actual concrete
surface in the 1/4" diameter hole to be used for the concrete anchors. Do not drill into mortar joints! Be sure to
mount in a solid part of the block, generally 1" minimum from the side of the block. Cinder block must meet ASTM
C-90 specifications. It is suggested that a standard electric drill on slow setting is used to drill the hole instead of
a hammer drill to avoid breaking out the back of the hole when entering a void or cavity.
• Concrete must be 2000 psi density minimum. Lighter density concrete may not hold concrete anchor.
• Make sure that the wall will safely support 4 times the combined load of the equipment and all attached hardware
and components.
WARNING