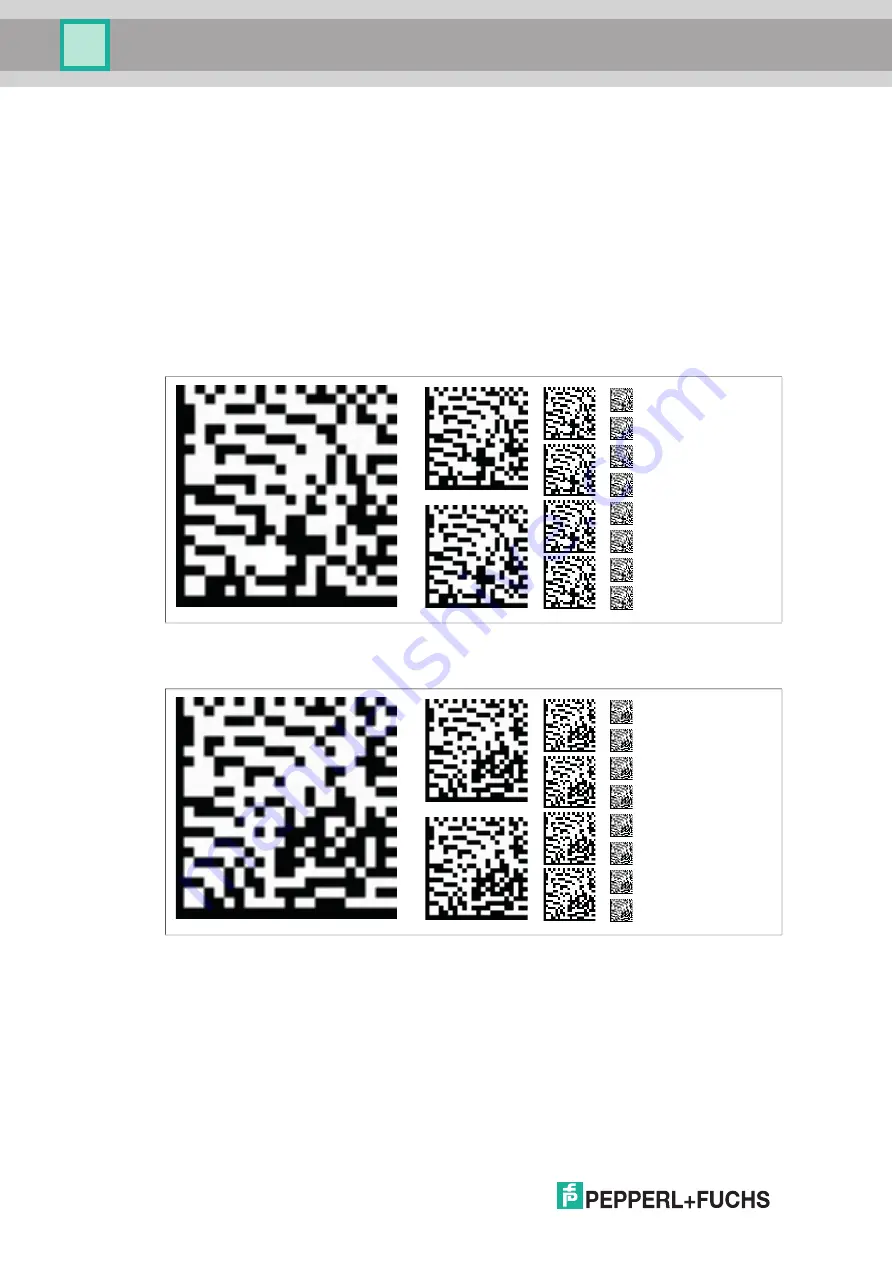
2
01
7-
11
30
Appendix
6.1.5
Code Cards for Adjusting Input/Output 3
Parameterization enables you to assign various functions to input/output 3 on the read head.
The following input/output functions are available:
Input: none
Output: Overspeed
Output: Warning
Output: Fault
Output: Event
Output: No position
Figure 6.17
Input/output 3 is defined as an input but has no function.
Figure 6.18
Input/output 3 is defined as an output. This output carries the potU
B
as long as
the defined maximum speed is exceeded.
Input 3: No Function
Output 3: Overspeed
Input 3
No function
Output 3
Overspeed