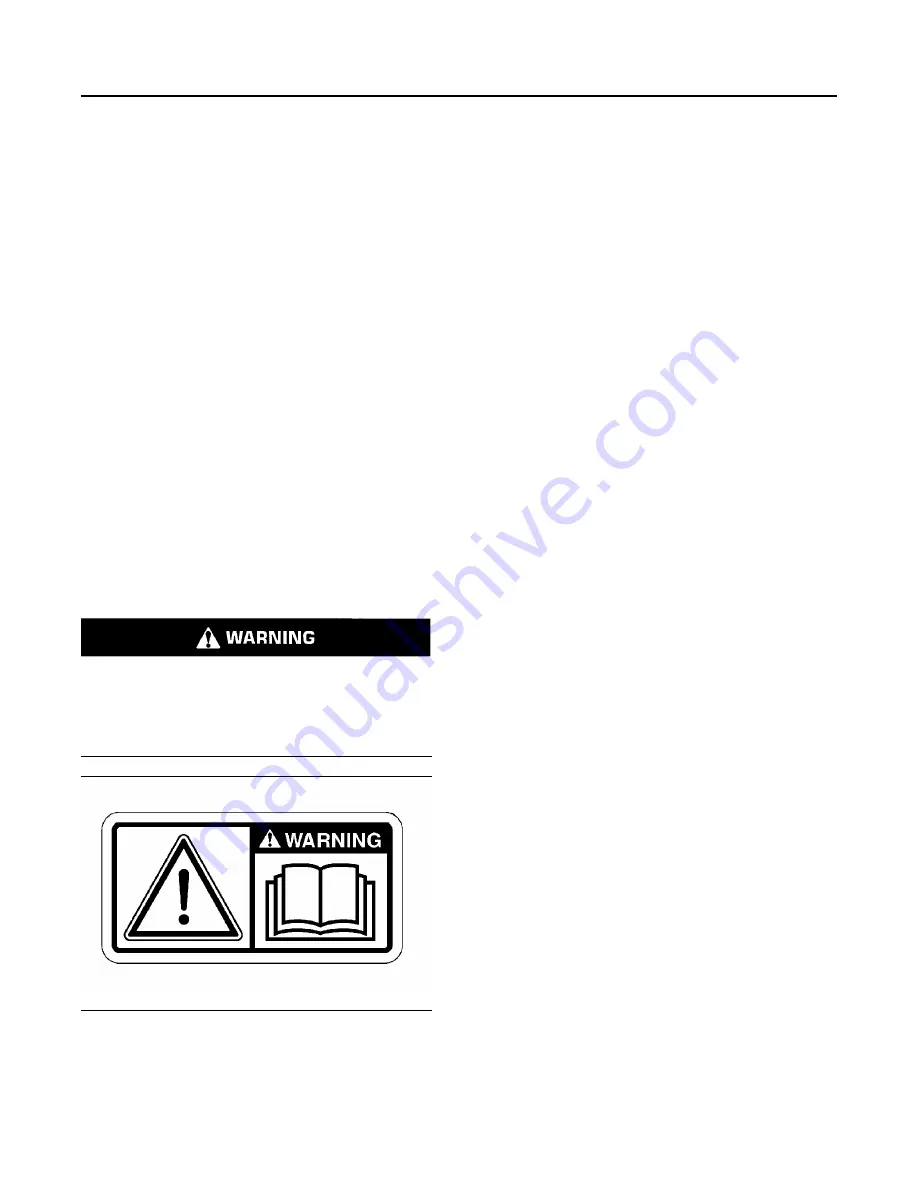
Safety Section
i02788195
Safety
Messages
There
may
be
several
specific
warning
signs
on
your
engine.
The
exact
location
and
a
description
of
the
warning
signs
are
reviewed
in
this
section.
Please
become
familiar
with
all
warning
signs.
Ensure
that
all
of
the
warning
signs
are
legible.
Clean
the
warning
signs
or
replace
the
warning
signs
if
the
words
cannot
be
read
or
if
the
illustrations
are
not
visible.
Use
a
cloth,
water,
and
soap
to
clean
the
warning
signs.
Do
not
use
solvents,
gasoline,
or
other
harsh
chemicals.
Solvents,
gasoline,
or
harsh
chemicals
could
loosen
the
adhesive
that
secures
the
warning
signs.
The
warning
signs
that
are
loosened
could
drop
off
of
the
engine.
Replace
any
warning
sign
that
is
damaged
or
missing.
If
a
warning
sign
is
attached
to
a
part
of
the
engine
that
is
replaced,
install
a
new
warning
sign
on
the
replacement
part.
Your
Perkins
distributor
can
provide
new
warning
signs.
(1)
Universal
Warning
Do not operate or work on this equipment unless
you have read and understand the instructions
and warnings in the Operation and Maintenance
Manuals. Failure to follow the instructions or
heed the warnings could result in serious injury
or death.
Illustration 1
g01154807
Typical example
The Universal Warning label (1) is located on both
sides of the valve mechanism cover base.
6
SEBU8119-04