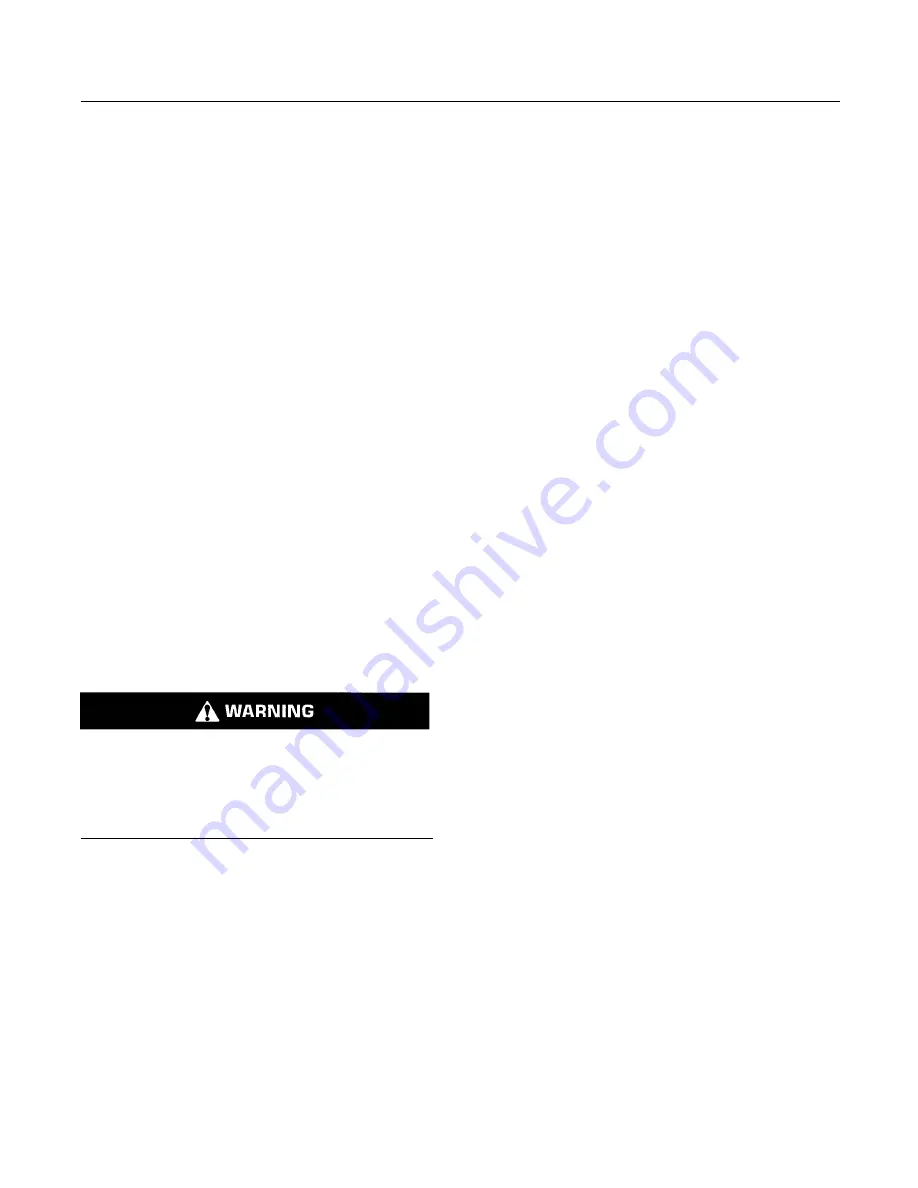
SEBU8337
77
Maintenance Section
Jacket Water Heater - Check
•
Outer covering that is chafed or cut
•
Exposed wire that is used for reinforcement
•
Outer covering that is ballooning locally
•
Flexible part of the hose that is kinked or crushed
•
Armoring that is embedded in the outer covering
A constant torque hose clamp can be used in place
of any standard hose clamp. Ensure that the constant
torque hose clamp is the same size as the standard
clamp.
Due to extreme temperature changes, the hose will
heat set. Heat setting causes hose clamps to loosen.
This can result in leaks. A constant torque hose
clamp will help to prevent loose hose clamps.
Each installation application can be different. The
differences depend on the following factors:
•
Type of hose
•
Type of
fi
tting material
•
Anticipated expansion and contraction of the hose
•
Anticipated expansion and contraction of the
fi
ttings
Replace the Hoses and the Clamps
Pressurized System: Hot coolant can cause seri-
ous burns. To open the cooling system
fi
ller cap,
stop the engine and wait until the cooling system
components are cool. Loosen the cooling system
pressure cap slowly in order to relieve the pres-
sure.
1.
Stop the engine. Allow the engine to cool.
2.
Loosen the cooling system
fi
ller cap slowly in
order to relieve any pressure. Remove the cooling
system
fi
ller cap.
Note:
Drain the coolant into a suitable, clean
container. The coolant can be reused.
3.
Drain the coolant from the cooling system to a
level that is below the hose that is being replaced.
4.
Remove the hose clamps.
5.
Disconnect the old hose.
6.
Replace the old hose with a new hose.
7.
Install the hose clamps.
8.
Re
fi
ll the cooling system.
9.
Clean the cooling system
fi
ller cap. Inspect the
cooling system
fi
ller cap’s gaskets. Replace
the cooling system
fi
ller cap if the gaskets are
damaged. Install the cooling system
fi
ller cap.
10.
Start the engine. Inspect the cooling system for
leaks.
i02486400
Jacket Water Heater - Check
Jacket water heaters help to improve startability in
ambient temperatures that are below 21 °C (70 °F).
All installations that require automatic starting should
have jacket water heaters.
Check the operation of the jacket water heater. For
an ambient temperature of 0 °C (32 °F), the heater
should maintain the jacket water coolant temperature
at approximately 32 °C (90 °F).
i03039820
Overhaul Considerations
(Top End Overhaul)
A scheduled 6000 hour overhaul that is based on
prime operation of the top end can limit down time
of the engine.
Prime Power
Operating Parameters
70% average load factor that is Limited to a maximum
of 4% of use at rated load (Prime point).
i03039981
Overhaul Considerations
(Major Overhaul)
A scheduled 12000 hour major overhaul can limit
down time of the engine.