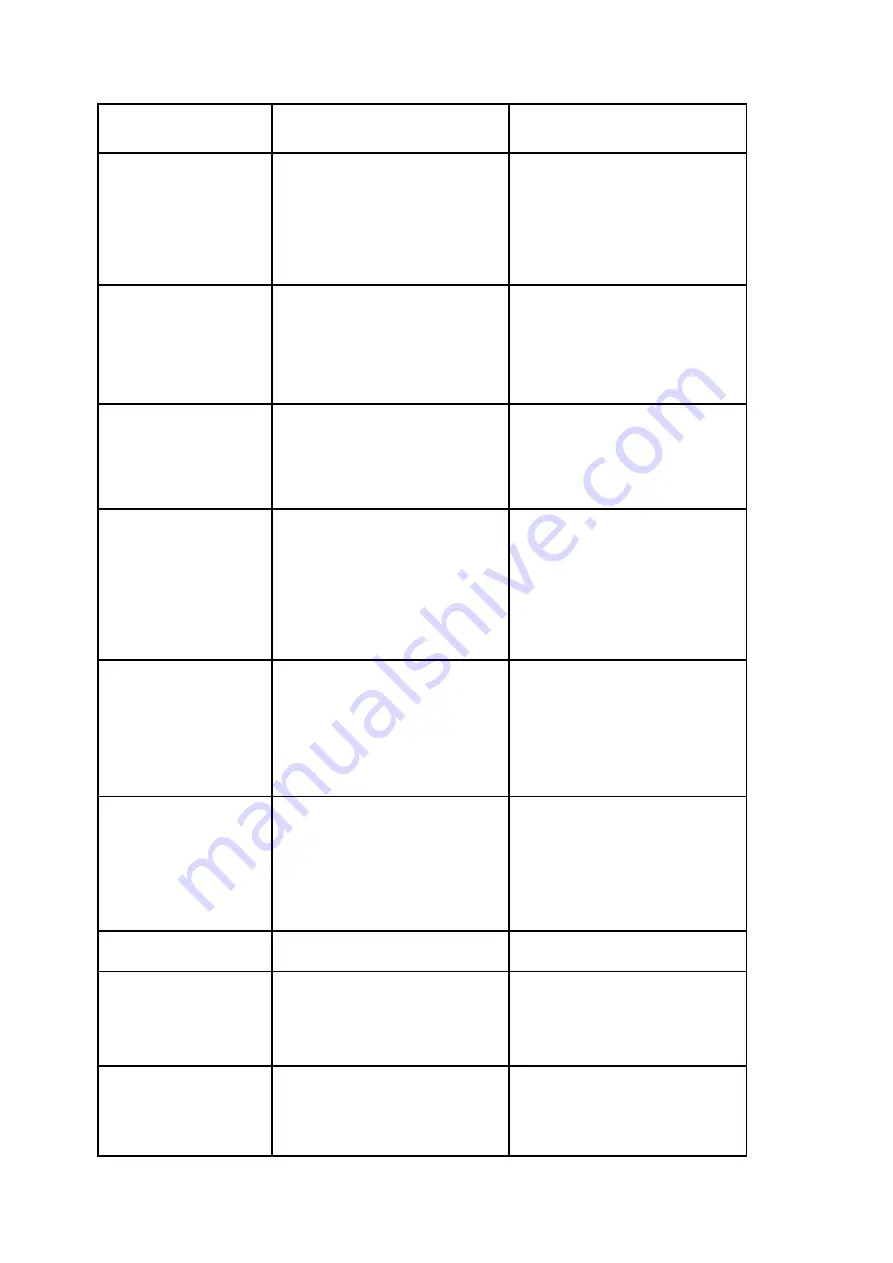
8
APPROVED LUBRICANTS
Supplier
U.K. Winter & Summer
Up to 30°C (86°F)
Tropical
Above 30°C (86°F)
Shell Oil Co. Ltd.
Rotella SX 10W
Rotella TX 10W
Rotella TX 10W/30
X-100 10W
Talona Oil 10W
Rotella SX 20 20W
Rotella TX 20 20W
Rotella SX 20W/40
Rotella TX 20W/40
Super Oil
Tractor Oil Universal
Mobil Oil Co. Ltd.
Delvac Special 10W/30
Delvac 1210
Delvac Special 10W/30
Mobiliand Universal
Mobiloil 20W 30
Delvac 1220
Mobilgard 212
B.P. Companies Ltd
Vanellus 10W
Super Visco-Static 10W/40
Vanellus 20W
Vanellus 20W 30
Super Visco-Static 20W/50
Energol 1C M20W
Tractor Oil Universal 20W/30
Castrol Ltd.
Deusol CRI 10
Deusol CRB 10
Deusol CRB 10W/30
Castrol CRI 10
Castrol CRB 10
Agricastrol Multi-Use 10W/30
Deusol CRI 20
Deusol CRB 20
Deusol CRB 10W/30
Oeusol CRM
Castrol CRB 20
Castrol 210 MX
Agricastrol Multi-Use 20W/30
Esso Petroleum Co
Ltd.
EssolubeHD 10W
Essolube HDX 10W
Essolube 0.3 HP 10W
Essolube D-3 10W
Essolube HDX 10W/30
Motor Oil 10W
Essolube HO 20W
Essolube HDX 20W
Essolube D-3 HP 10W
Essolube D-3 10W
Essolube HDX 10W/30
Motor Oil 20W
Caltex (UK) Ltd.
Supreme Five Star 10W/30
Custom Five Star 10W/30
Five Star 10W
RPM Delo200 10W/30
RPM Delo 200 10W
RPM Delo 100 10W
Supreme Five Star 10W/30
Custom Five Star 10W/30
Five Star 20/20W
RPM Delo200 10W/30
RPM Delo 200 20/20W
RPM Delo 100 20/20W
Chevron International
Oil Co Ltd.
Delo Special 10W
Delo200 10W
Delo Special 20/20W
Delo 200 20/20W
Texaco Ltd.
Ursa Extra Duty 10W
Ursa Extra Duty 10W/30
Havoline 10W
Havoline 10W/40
Ursa Extra Duty 20W
Ursa Extra Duly 10W/30
Havoline 20/20W
Havoline 10W/40
Gulf Oil (G.B.) Ltd
Gulflube XHD 10W
Gulflube XHD 10W/30
Multi-G 10W/30
Gulflube XHD 20/20W
Gulflube XHD 10W/30
Mulli-G 10W/30
Superfleet 20W/30