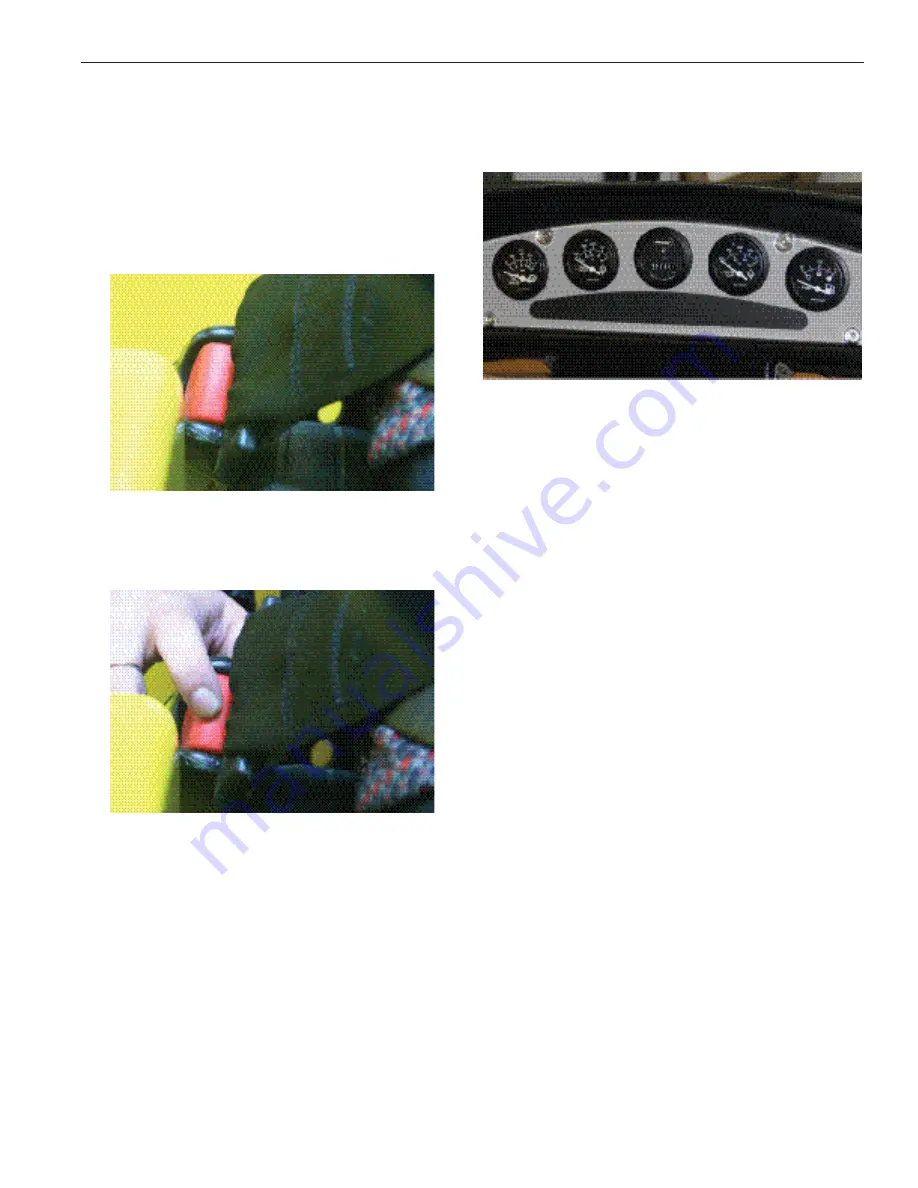
fORKLIfT OPERaTION
45
Extendo and Traverse Operation and Maintenance Manual
800-GO-PETTIBONE
seat Belt
fasten the seat belt as follows:
Position the belt across your waist as low on the
1.
hips as possible. This is necessary to spread
the force of the belt over the hip bone instead of
across the abdomen.
Insert latch plate into buckle until a “click” is
2.
heard. Hold tab and pull on strap so it fits snugly.
seat Belt fastening
figure 13.
To unlock the seat belt, press button on the
3.
buckle and pull latch plate from buckle.
seat Belt Release
figure 14.
Make sure that seat belt fits snugly across
•
your waist with a minimal amount of slack.
If the belt has too much slack, it may not be
able to restrain you in an accident.
Never wear a twisted seat belt.
•
Pettibone/Traverse Lift, LLC recommends that
operators use the seat belt at all times when driving
this machine and will not be held responsible if the
operator does not use the safety restraints available.
Instrument Panel
The instrument panel indicates the location of each
standard and optional gauge, warning light and
control.
Instrument Panel
figure 15.
fuel Gauge
The fuel gauge indicates the level of diesel fuel in
the fuel tank. The fuel gauge is electrically operated
and registers only with the ignition switch in the ON
or sTaRT position.
Engine Coolant Temperature Gauge
This gauge indicates the temperature of the fluid
in the engine cooling system. Normal coolant
temperature for the Cummins QsB4.5 engine is
160-194°f (70-90°C). NOTICE: Do not operate
engine if coolant temperature exceeds 225°f
(107°C).
Engine Hour Meter
Indicates the actual hours of engine operation. It
records up to 9,999.9 hours and then restarts at
zero.
Transmission Temperature Gauge
This gauge indicates the temperature of the
transmission oil.
Normal Operating Range: 180-220°f (82-106°C)
Red Line Temperature: 250°f (121°C)
Summary of Contents for Extendo 1032
Page 1: ...Operator s Manual PMOM 4021 736 744 936 944 1032 1144 1157 T944 T1157...
Page 2: ......
Page 8: ...vi Extendo and Traverse Operation and Maintenance Manual 800 GO PETTIBONE Contents...
Page 65: ...FORKLIFT OPERATION 57 Extendo and Traverse Operation and Maintenance Manual 800 GO PETTIBONE...
Page 67: ...FORKLIFT OPERATION 59 Extendo and Traverse Operation and Maintenance Manual 800 GO PETTIBONE...
Page 68: ...FORKLIFT OPERATION 60 Extendo and Traverse Operation and Maintenance Manual 800 GO PETTIBONE...
Page 70: ...FORKLIFT OPERATION 62 Extendo and Traverse Operation and Maintenance Manual 800 GO PETTIBONE...
Page 71: ...FORKLIFT OPERATION 63 Extendo and Traverse Operation and Maintenance Manual 800 GO PETTIBONE...
Page 73: ...FORKLIFT OPERATION 65 Extendo and Traverse Operation and Maintenance Manual 800 GO PETTIBONE...
Page 75: ...FORKLIFT OPERATION 67 Extendo and Traverse Operation and Maintenance Manual 800 GO PETTIBONE...
Page 77: ...FORKLIFT OPERATION 69 Extendo and Traverse Operation and Maintenance Manual 800 GO PETTIBONE...
Page 78: ...FORKLIFT OPERATION 70 Extendo and Traverse Operation and Maintenance Manual 800 GO PETTIBONE...
Page 80: ...FORKLIFT OPERATION 72 Extendo and Traverse Operation and Maintenance Manual 800 GO PETTIBONE...
Page 81: ...FORKLIFT OPERATION 73 Extendo and Traverse Operation and Maintenance Manual 800 GO PETTIBONE...
Page 83: ...FORKLIFT OPERATION 75 Extendo and Traverse Operation and Maintenance Manual 800 GO PETTIBONE...
Page 85: ...FORKLIFT OPERATION 77 Extendo and Traverse Operation and Maintenance Manual 800 GO PETTIBONE...
Page 87: ...FORKLIFT OPERATION 79 Extendo and Traverse Operation and Maintenance Manual 800 GO PETTIBONE...
Page 89: ...FORKLIFT OPERATION 81 Extendo and Traverse Operation and Maintenance Manual 800 GO PETTIBONE...
Page 91: ...FORKLIFT OPERATION 83 Extendo and Traverse Operation and Maintenance Manual 800 GO PETTIBONE...
Page 119: ......