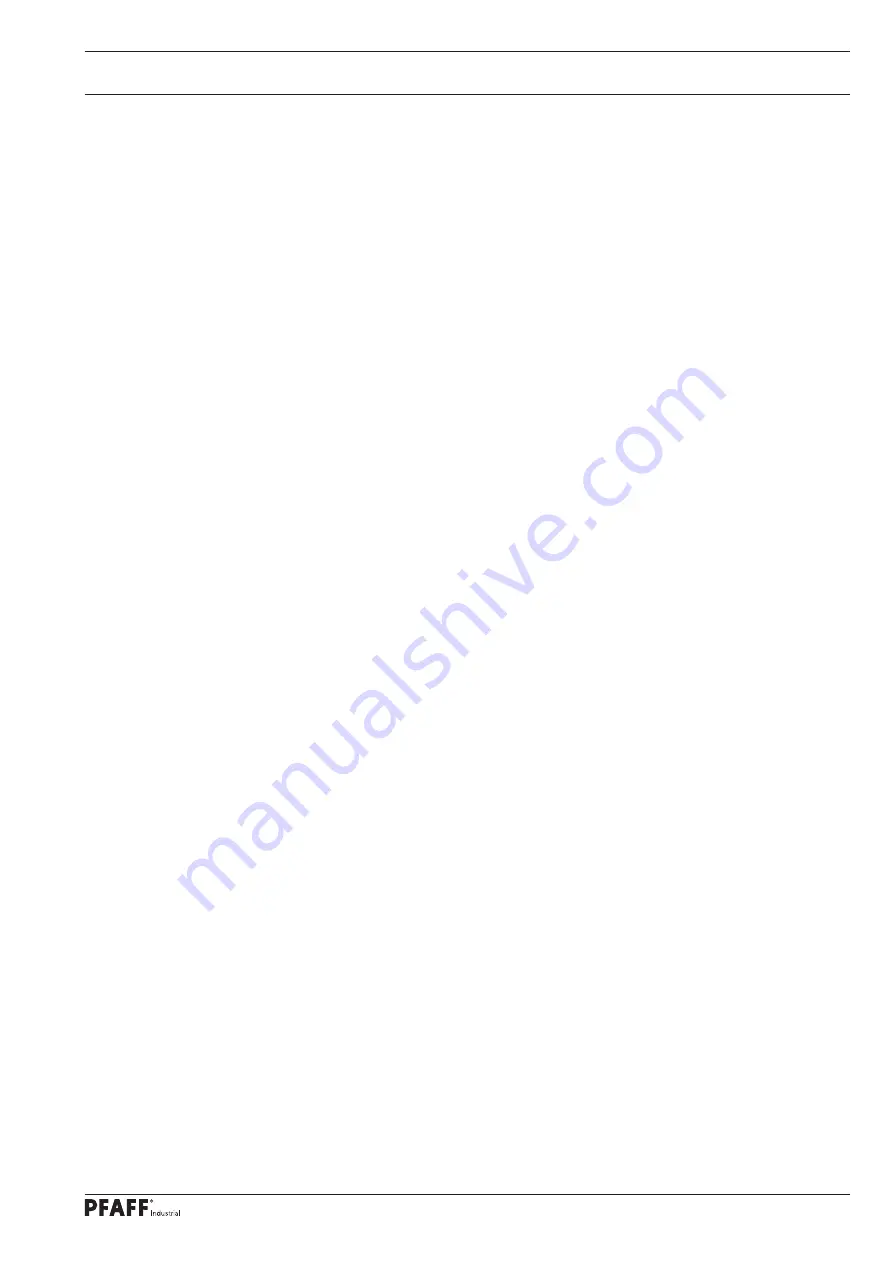
Table of Contents
Contents ..................................................................................Page
1
Safety
.................................................................................................................................... 6
1
.01 Directives
............................................................................................................................... 6
1
.02
General safety instructions .................................................................................................... 6
1
.03 Safety
symbols
...................................................................................................................... 7
1
.04
Special points of attention for the owner-operator ................................................................. 7
1
.05
Operating personnel and technical staff ................................................................................ 8
1
.05.01 Operating
personnel
.............................................................................................................. 8
1
.05.02 Technical
staff
........................................................................................................................ 8
1
.06 Danger
warnings
.................................................................................................................... 9
2
Proper
Use
.......................................................................................................................... 10
3
Technical
Data
.................................................................................................................... 11
3
.01 PFAFF
1591
.......................................................................................................................... 11
3
.02 PFAFF
1593
.......................................................................................................................... 12
4
Disposal of the Machine .................................................................................................... 13
5
Transportation, Packaging and Storage .......................................................................... 14
5
.01
Transport to the customer’s premises ................................................................................. 14
5
.02
Transport within the customer’s premises ........................................................................... 14
5
.03
Disposal of the packaging materials .................................................................................... 14
5
.04 Storage
................................................................................................................................ 14
6
Work
Symbols
.................................................................................................................... 15
7
Operating
Controls
............................................................................................................ 16
7
.01 Main
switch
......................................................................................................................... 16
7
.02
Keys on the machine head ................................................................................................... 16
7
.03
Bobbin thread monitoring using stitch counting .................................................................. 17
7
.04 Pedal
.................................................................................................................................... 17
7
.05
Hand lever to raise the roller presser ................................................................................... 18
7
.06
Swivelling out the roller presser .......................................................................................... 18
7
.07 Knee
switch
......................................................................................................................... 19
7
.08 Knee
lever
............................................................................................................................ 19
7
.09
Edge trimmer -725/04 for PFAFF 1591 ................................................................................ 20
7
.10 Control
panel
........................................................................................................................ 21
8
Set-up and Initial Start-up ................................................................................................. 22
8
.01 Set-up
.................................................................................................................................. 22
8
.01.01
Setting the table height ........................................................................................................ 22
8
.01.02
Inserting the sewing machine into the stand ....................................................................... 23
8
.01.03
Assembling the anti-tipping device ...................................................................................... 24
8
.02
Mounting the fl ange motor .................................................................................................. 24
8
.02.01
Mounting the fl ange motor on the bearing plate ................................................................. 24
Summary of Contents for 1591
Page 77: ...77 13 Table Top 13 01 Tilt base Tilt base 2x rawlplugs ...
Page 81: ...Notes ...