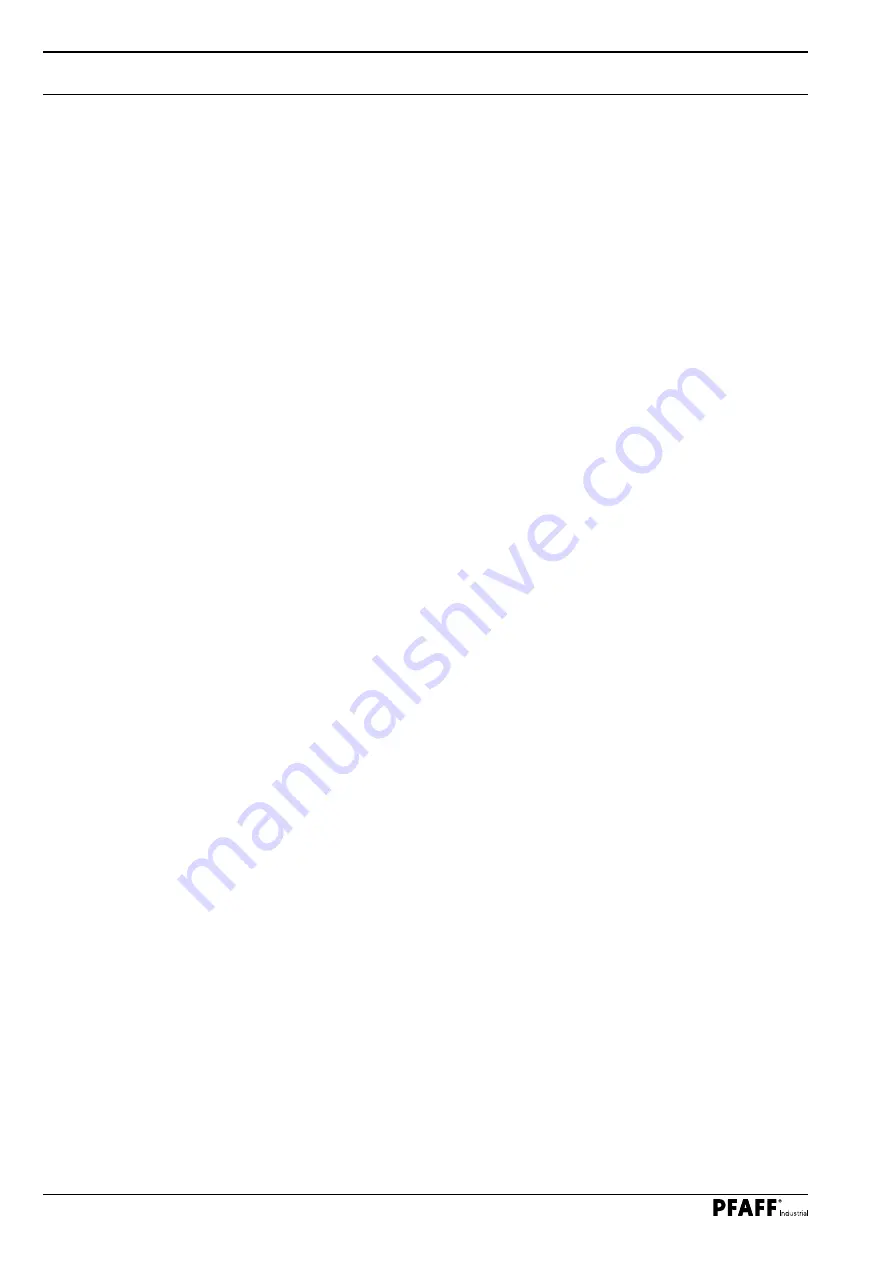
Table of Contents
Contents ..................................................................................Page
13
.05.08
Control cam (pre-calibrating) ................................................................................................ 23
13
.05.09 Blade .................................................................................................................................... 24
13
.05.10
Test cut ................................................................................................................................ 25
13
.06
Parameter settings ............................................................................................................. 26
13
.07
Internet update of control P40 CD ...................................................................................... 26
14
Circuit Diagrams
.......................................................................................................... 27
Summary of Contents for 333-712/02
Page 29: ...Notes...