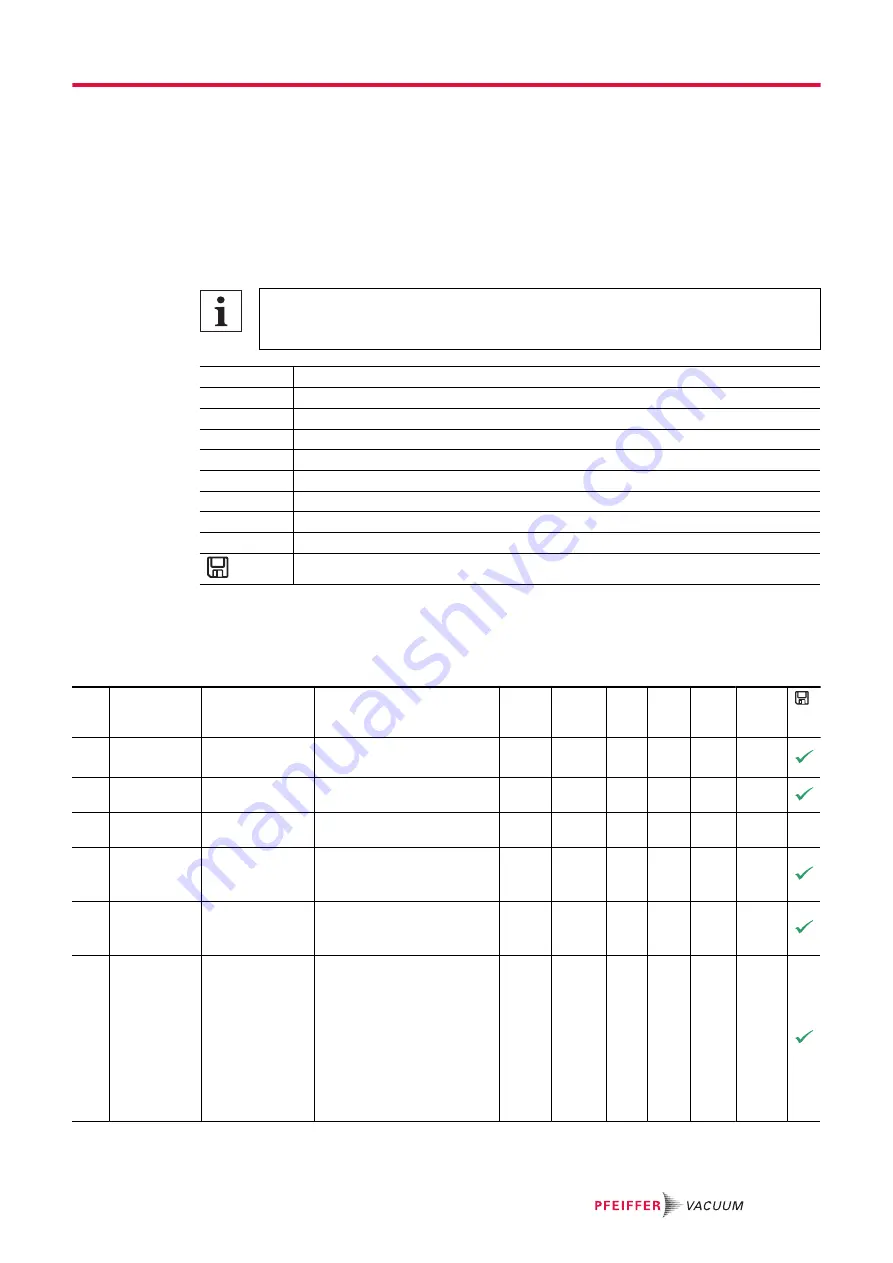
7 Parameter set
7.1 General
Important settings and function-related characteristics are factory-programmed into the electronic drive
unit as parameters. Each parameter has a three-digit number and a description. The parameter can be
accessed via Pfeiffer Vacuum control units or externally via RS-485 using Pfeiffer Vacuum protocol.
The vacuum pump starts in standard mode with factory default pre-set parameters.
Non-volatile data storage
When switching off or in the event of unintentional voltage drop, the
parameters
and the
operating hours stay saved in the electronics.
#
Three digit number of the parameter
Indicator
Display of parameter description
Description
Brief description of the parameters
Functions
Function description of the parameters
Data type
Type of formatting of the parameter for the use with the Pfeiffer Vacuum protocol
Access type
R (read): Read access; W (write): Write access
Unit
Physical unit of the described variable
min. / max.
Permissible limit values for the entry of a value
default
Factory default pre-setting (partially pump-specific)
The parameter can be saved persistently in the electronic drive unit
Tbl. 8:
Explanation and meaning of the parameters
7.2 Control commands
#
Indicator
Designations
Functions
Data
type
Ac-
cess
type
Unit min. max. de-
fault
002 Stand-by
Stand-by
0 = off
1 = on
0
RW
0
1
0
006 Auto stdby
automatic
standby
not supported
0
RW
0
1
0
009 ErrorAckn
Malfunction ac-
knowledgement
1 = Malfunction acknowl-
edgement
0
W
1
1
010 PumpgStatn
Pumping station
0 = off
1 = on and malfunction ac-
knowledgment
0
RW
0
1
0
011 Auto boost
automatic boost
operation
(Not supported)
0 = off
1 = on
0
RW
0
1
0
019 Cfg DO2
Output DO2
configuration
0 = Switch-point reached
1 = No error
2 = Error
5 = Set rotation speed
reached
6 = Pump on
9 = Always "0"
10 = Always "1"
11 = Remote priority active
7
RW
0
21
5
Parameter set
35/68