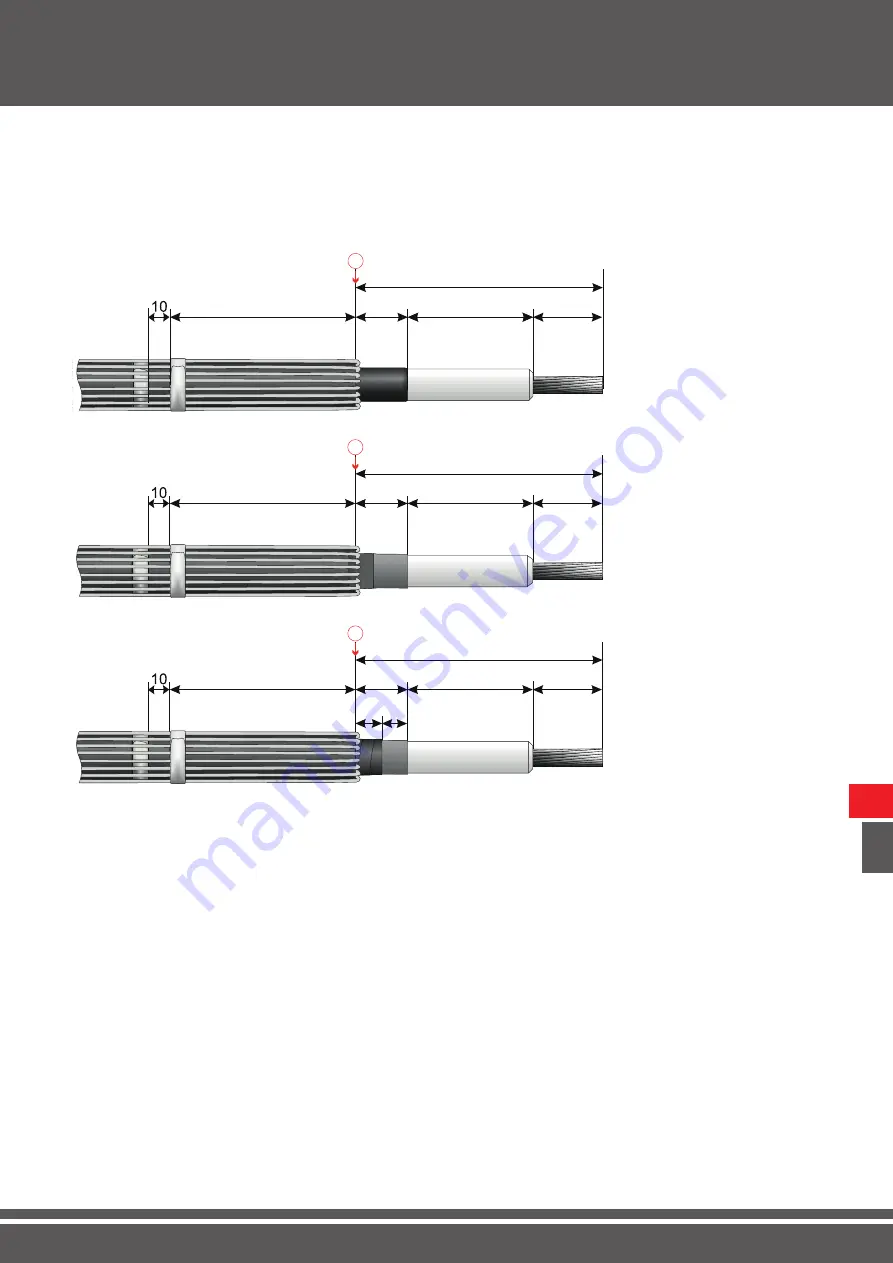
www.pfisterer.com
25
Drawings not to scale - for information only Size 3 | 3-S / Standard instructions wire screen / No. 040 371 001 (2014-05-08) i-01
8.3
Checking
160
85
110
1
235
40
160
85
110
1
235
40
160
85
110
1
235
40
20 20
Comparing the insulation diameter with application of the
insulating part
Check if the diameter of the insulation is within the working range of the
insulating part (see label / packing list / insulating part ). If the diameter is
not within these values,
DO NOT INSTALL THE INSULATING PART
.
VIII
"normal" peelable conductive layer
"thick" peelable conductive layer
Installation / Assembly
Control image for dimensions
strippable conductive layer
Summary of Contents for MV-CONNEX 3
Page 2: ...2 www pfisterer com...