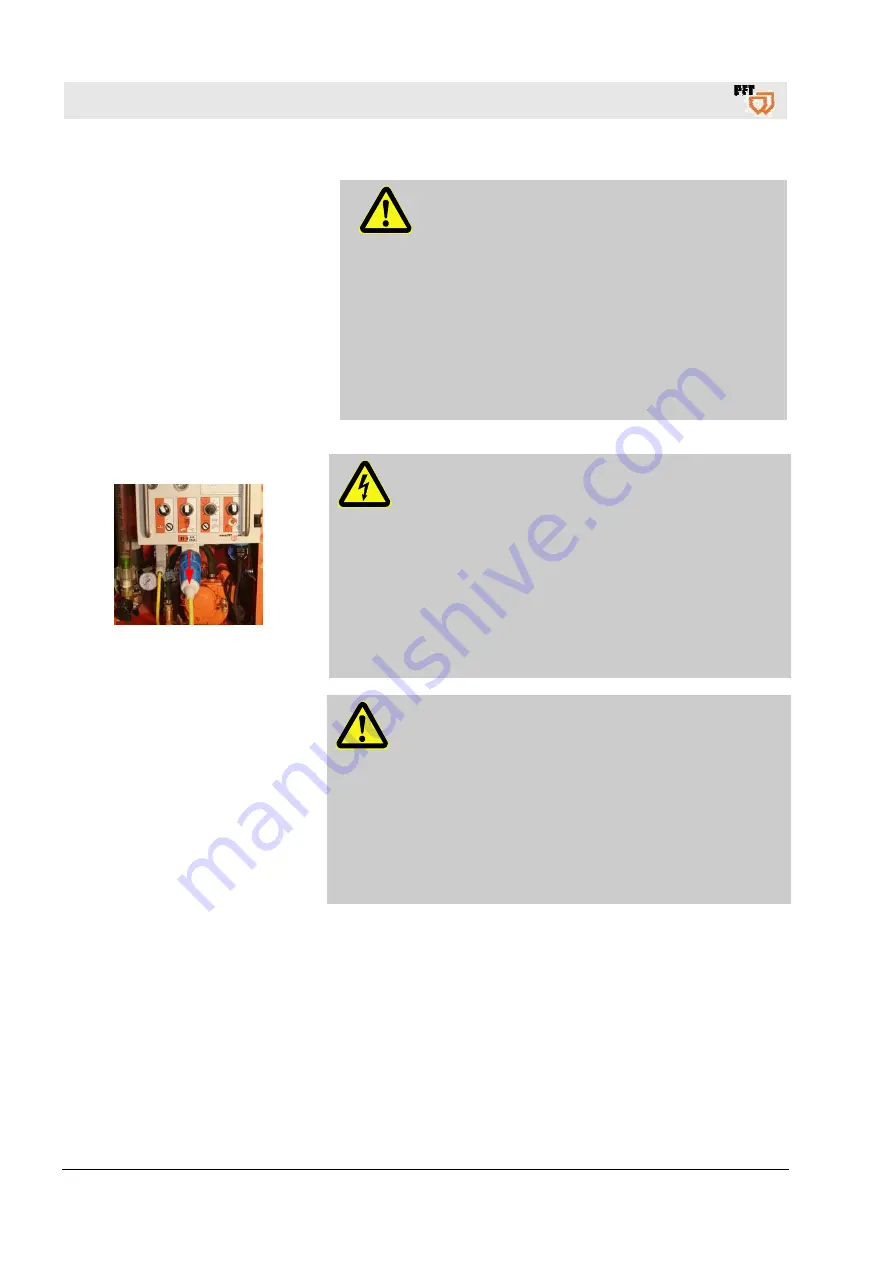
Mixing pump RITMO L / RITMO M Overview - Operation
Maintenance
64
2016-02-17
Basic information
WARNING!
Risk of injury due to improperly carried out
maintenance work!
Improper maintenance can lead to severe injuries
or considerable property damage.
Therefore:
Ensure order and safety at the assembly site!
Loose, stacked components or components lying
about can cause accidents.
If components were removed, ensure proper
assembly, put back all fastening elements and
observe torque indications for screws.
49.2 Remove connection cable
Electrical system
Fig. 111: Remove connection cable
DANGER!
Danger of death from electric current!
There is danger to life if you come in contact with live
parts. Activated electrical components can carry out
uncontrolled movements and cause serious injuries.
Therefore:
Switch off the energy supply before starting any work
and secure against restarting.
Disconnect the power supply by removing the
connection cable
Secure against restarting
DANGER!
DANGER!
Danger to life from unauthorised restarting!
When carrying out troubleshooting work, there is the
risk that the energy supply is switched on without
authorisation. This poses a danger to life for the
persons in danger area.
Therefore:
Switch off all power supplies before starting any
work and secure against restarting