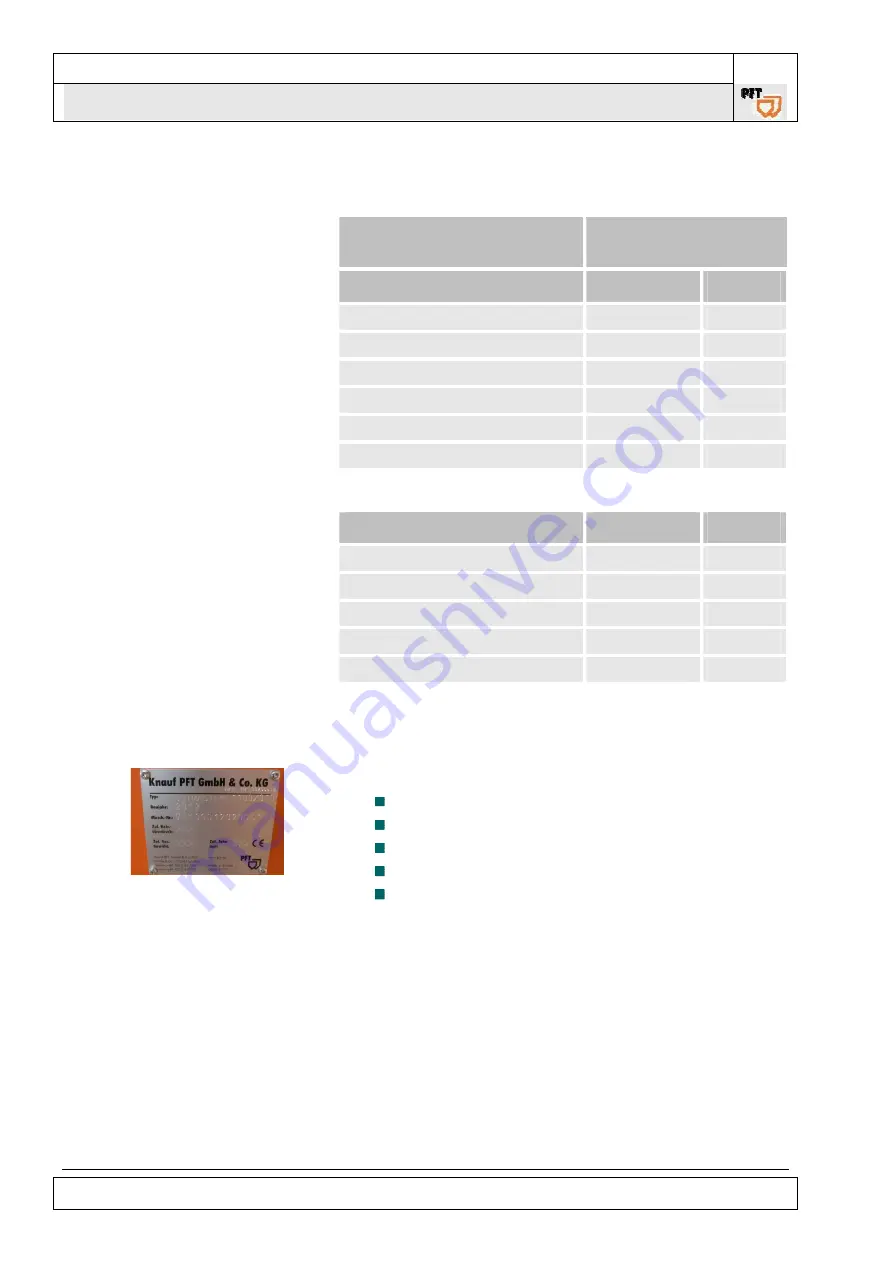
HOT WIRE CUTTING TOOL Overview - Operation - Spare parts lists
Name plate
Page 26
29.07.2013
12.4 Technical data PFT CUTMASTER 1300/310
Article number PFT CUTMASTER
1300/310
00 29 30 72
Particular
Value Unit
Weight
approx. 16.5 kg
Rear support foot
approx. 1.0 kg
Cutting depth
300 mm
Cutting height
1350 mm
Scale, left
up to 1000 mm
Scale, right
up to 440 mm
12.5 Connection values
Particular
Value Unit
Power connection
230 V
Power
200 VA
Secondary voltage
36 V
Protection class
44 IP
Thermal circuit breaker
110° C
13 Name plate
Fig. 2: Name plate
The following details can be found on the name plate:
Manufacturer
Article number of the tool
Type
Year of manufacture
Machine number