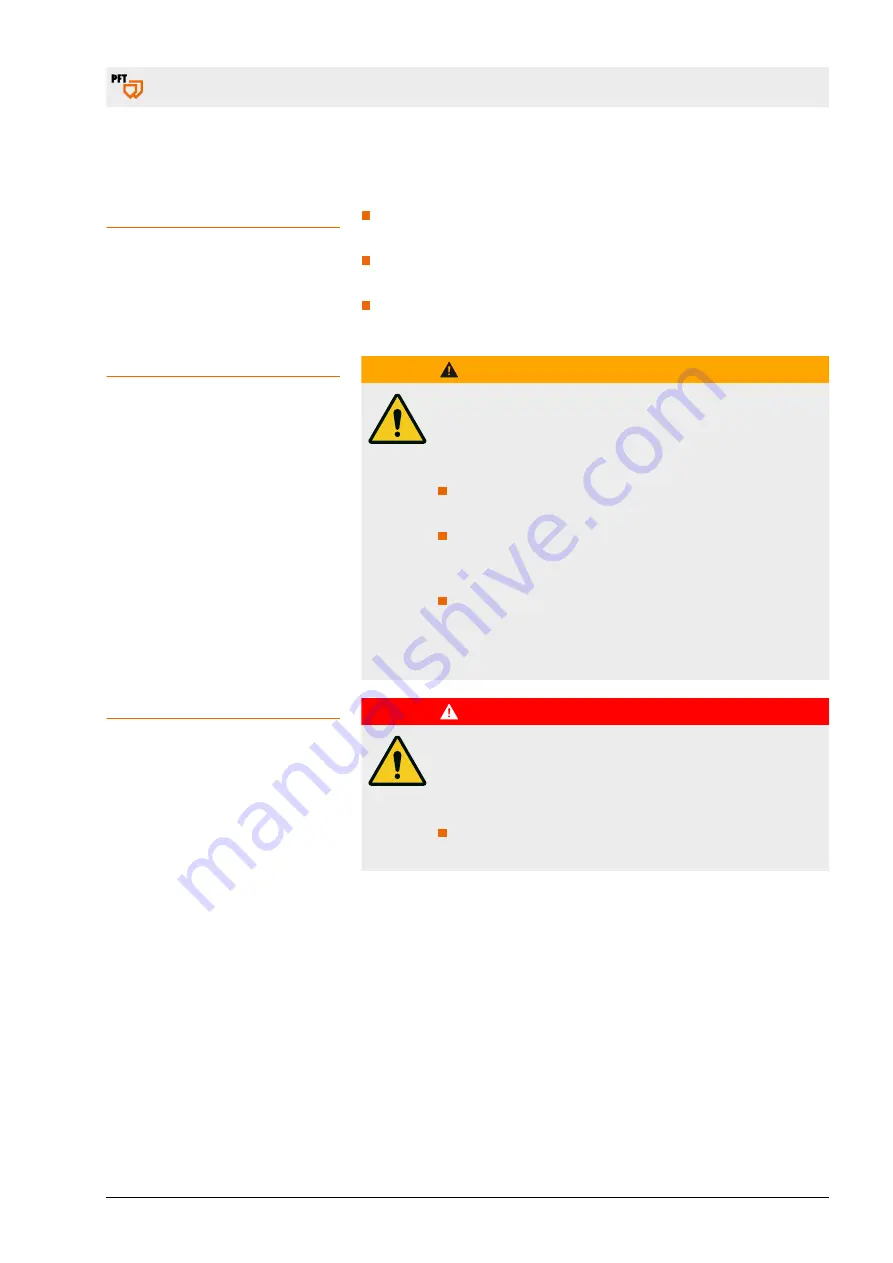
Mixing pump RITMO XL FC-230/400V / Part 2 Overview, operation and service
Maintenance
6
Maintenance
6.1
Safety
Personnel
The maintenance works described here can be carried out by the
operator, unless marked otherwise.
Some maintenance work must only be carried out by specially
trained technical personnel or exclusively by the manufacturer.
Work on electrical systems must always only be carried out by
qualified electricians.
Basic information
WARNING
Risk of injury due to improperly carried out
maintenance work!
Improper maintenance can lead to severe injuries or
considerable property damage.
Prior to starting the works ensure that there is enough
space to carry out the works.
Ensure order and safety at the assembly site! Unat-
tached components or tools left lying around or
stacked on one another can cause accidents.
If components have been previously removed, ensure
that they are mounted again correctly, reattach all
fastening elements and adhere to the specified screw
tightening torques.
Electrical system
DANGER
Danger to life from electric current!
Contact with live components can lead to death or serious
injury. Live electrical components can move uncontrollably
and cause serious injury.
Switch off the energy supply before starting any work
and secure against restarting.
page 65 / 76