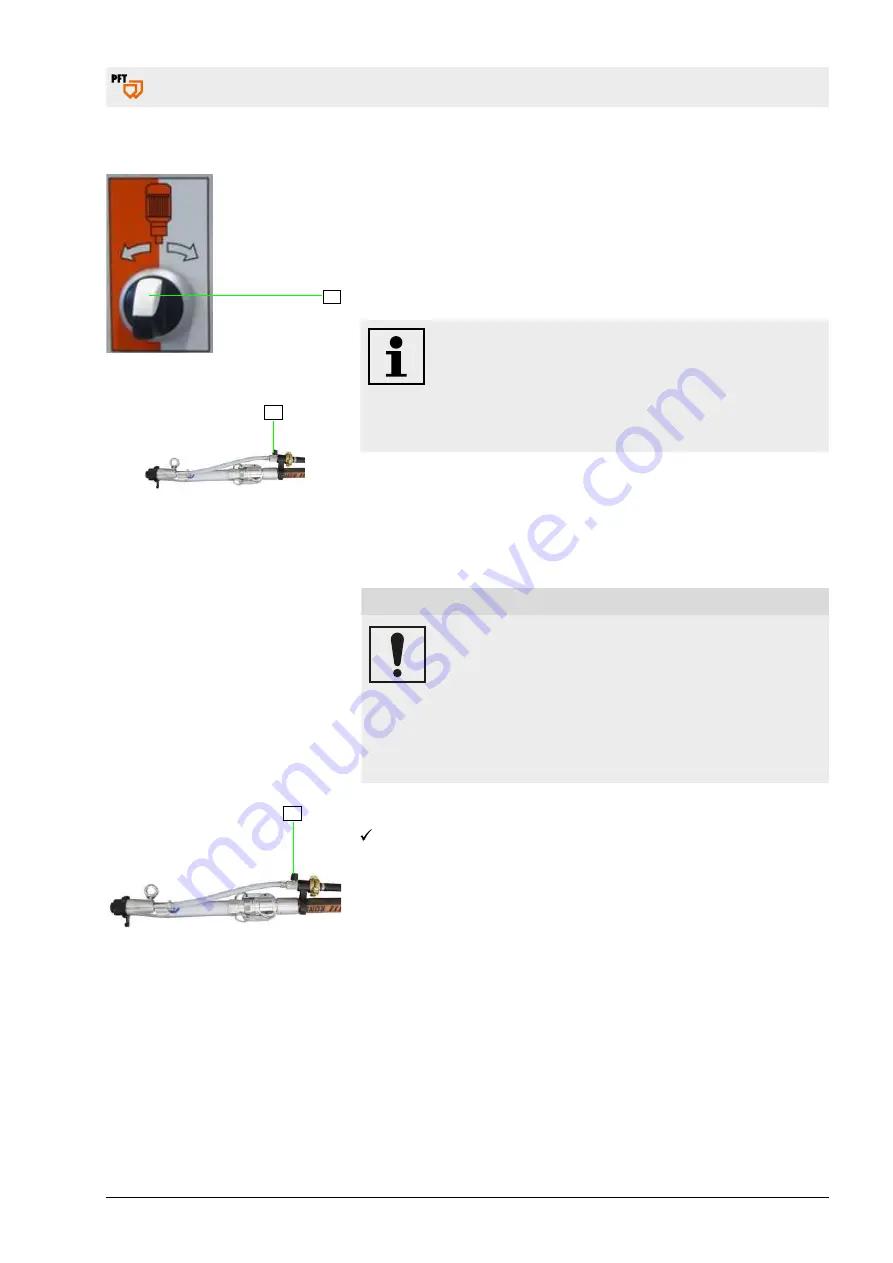
Mixing pump G 4 X FU 230/400V / Part 2 Overview, operation and service
Operation
5.7.1
Opening the air tap on the spray gun
1
Figure 61: Switching on
2
Figure 62: Opening the air tap
1. Turn the pump motor selector switch (1) to "right" position.
2. Point the spray gun toward the wall to be plastered.
3. Ensure that nobody is in the discharge area of the mortar.
4. Open the air tap (2) on the spray gun.
5. The machine will start-up automatically via the pressure switch-off
and the mortar emerges.
The correct mortar consistency is reached, if the mate-
rial mixes on the surface to be sprayed (we recommend
application on wall surfaces from top to bottom). Uniform
mixing and spraying cannot be ensured if the amount
of water is insufficient. This can clog the hoses and the
pumping components are then subjected to greater wear.
5.8
Interruption of work
NOTE
Always observe the setting time of the material to be
processed:
Clean the system and mortar hoses depending on the
setting time of the material and the length of the interrup-
tion (pay attention to outside temperature).
The guidelines of the material manufacturers have to be
observed regarding breaks.
1
Figure 63: Closing the air tap
1. Close the air tap (1) if you interrupt your work for a short while.
The machine stops.
By opening the air tap (1), the machine will start running again.
page 47 / 80
Summary of Contents for 00260621
Page 77: ...Mixing pump G 4 X FU 230 400V Part 2 Overview operation and service Disposal page 77 80...
Page 78: ...Mixing pump G 4 X FU 230 400V Part 2 Overview operation and service Disposal page 78 80...
Page 79: ...Mixing pump G 4 X FU 230 400V Part 2 Overview operation and service Disposal page 79 80...