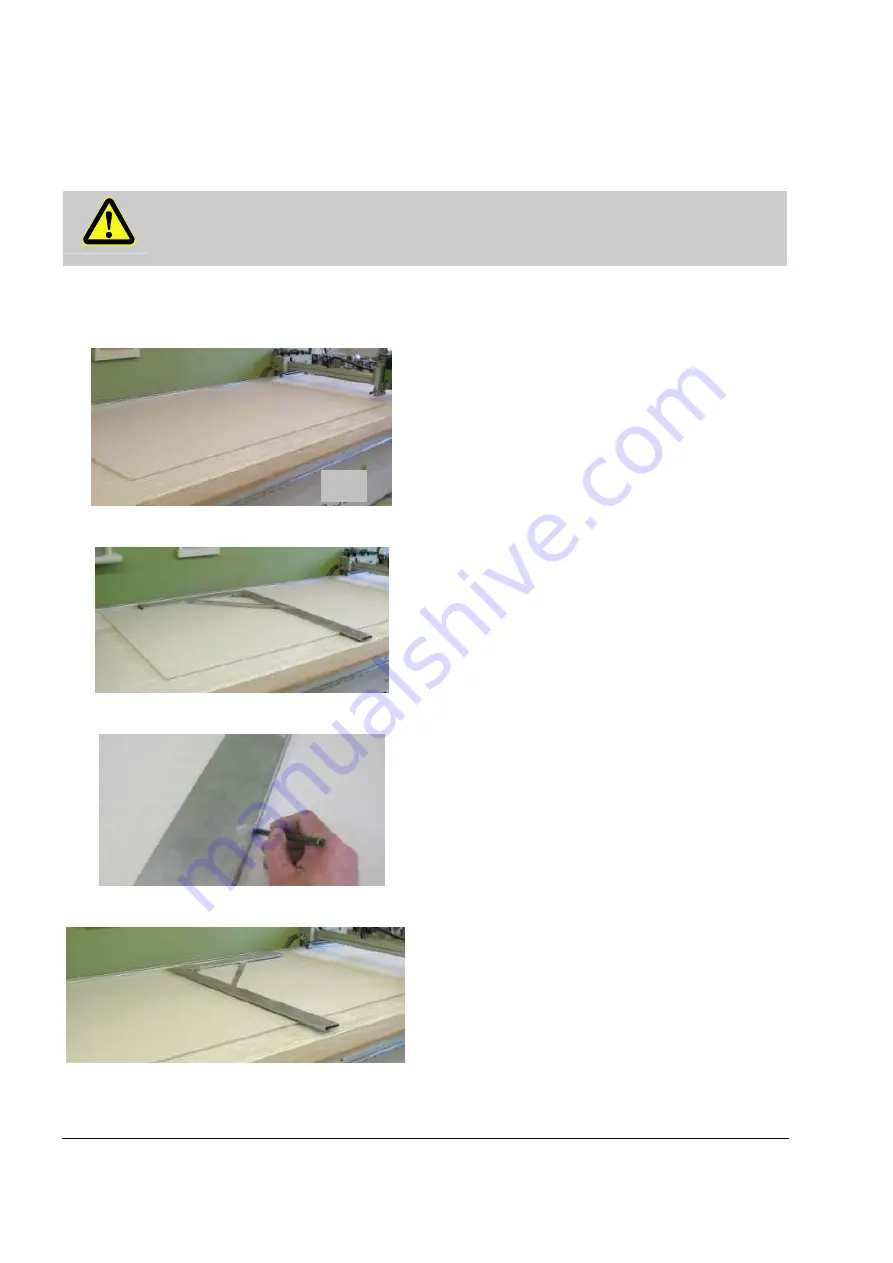
Safety - Service Manual - Spare Part Lists
Service Manual PFT BOARDMASTER and Units
2011-04-07
10
6 Service Manual PFT BOARDMASTER and Units
DANGER!
During all service and setting tasks, the main switch must be put Off and/or the
machine detached from the mains.
7 Settings Angularity on the Y- Arm
7.1 First, the Y –arm is checked for angularity
Figure 1.1
For this purpose, a gypsum board is laid on the
machine table, which is placed against the rear rail.
(Figure: 1.1)
Figure 1.2
Afterwards, lay a large angle in the middle of the
gypsum board on the rear rail. (Figure: 1.2)
Figure 1.3
A pencil line is then drawn along the angle. (Figure:
1.3)
Figure 1.4
Afterwards the angle is rotated for verification and
thus verified whether the rail is straight. (Figure: 1.4)
Har