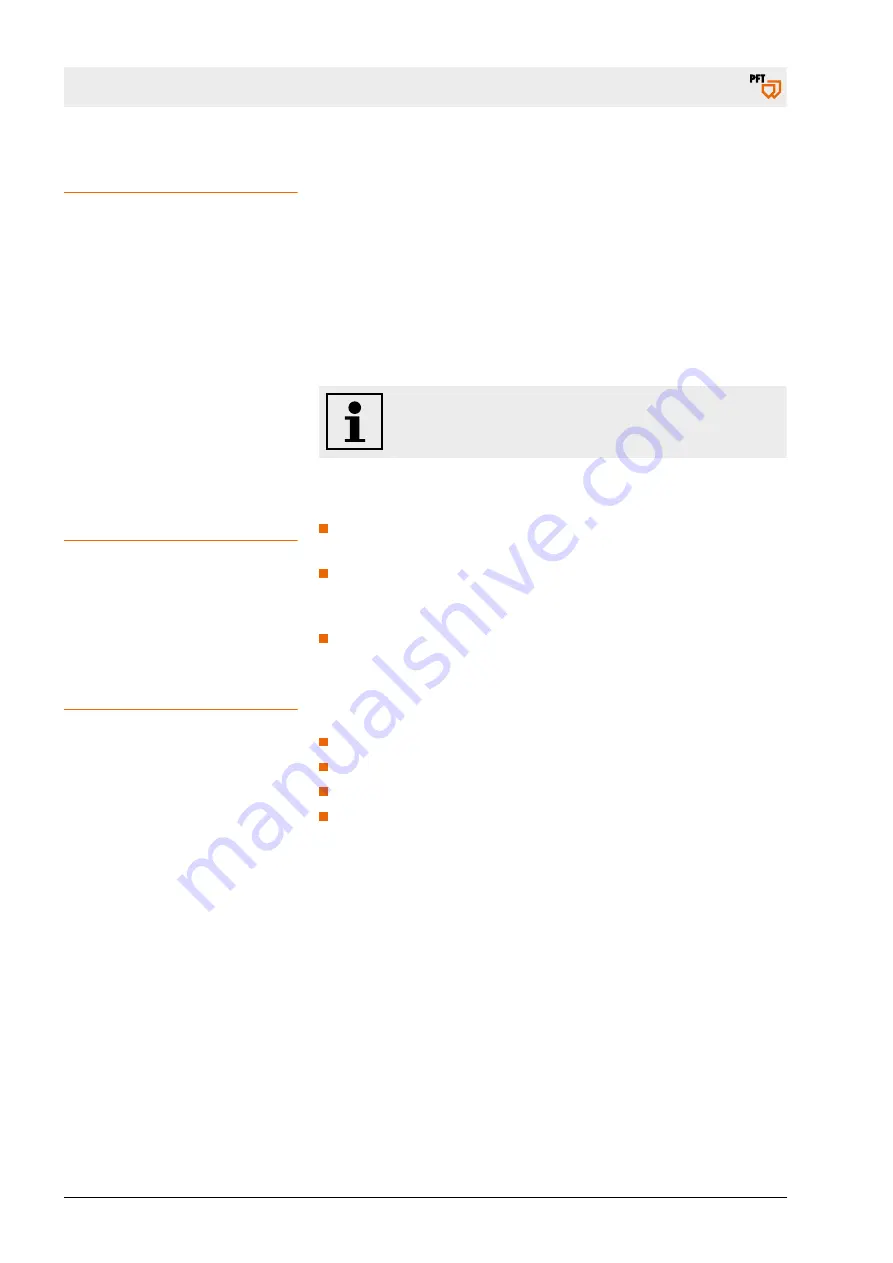
Mixing pump G 4 X Super / G 4 X XL / Part 2 Overview, operation and service
Operation
5.14
Reaction in the event of faults
Reaction in the event of faults
The following applies as a general rule:
1. In the event of faults presenting immediate danger to persons or
property, activate the emergency OFF function immediately.
2. Determine cause of the fault.
3. If the rectification of faults requires works in the danger zone,
switch off the system and secure against restarting.
4. Inform the manager on site immediately about the fault.
5. Depending on the type of fault, commission authorised skilled
personnel or rectify the fault yourself.
The following fault table gives information on who is
authorised to rectify the fault.
5.14.1
Safety
Personnel
The work for rectification of faults described here can be carried
out by the operator, unless marked otherwise.
Some works must be carried out only by specially trained skilled
personnel or exclusively by the manufacturer. Information on this
can be found in the description of the individual faults.
Work on electrical systems must always only be carried out by
qualified electricians.
Personal protective equipment
The following protective equipment has to be worn for all maintenance
work:
Protective clothing
Protective goggles
Protective gloves
Safety shoes
5.14.2
Faults
The following chapter describes possible causes for faults and the
activities carried out for their rectification.
In case faults occur frequently, shorten the maintenance intervals in
accordance with the actual load.
Contact your dealer if malfunctions occur that cannot be solved using
this manual.
page 52 / 72