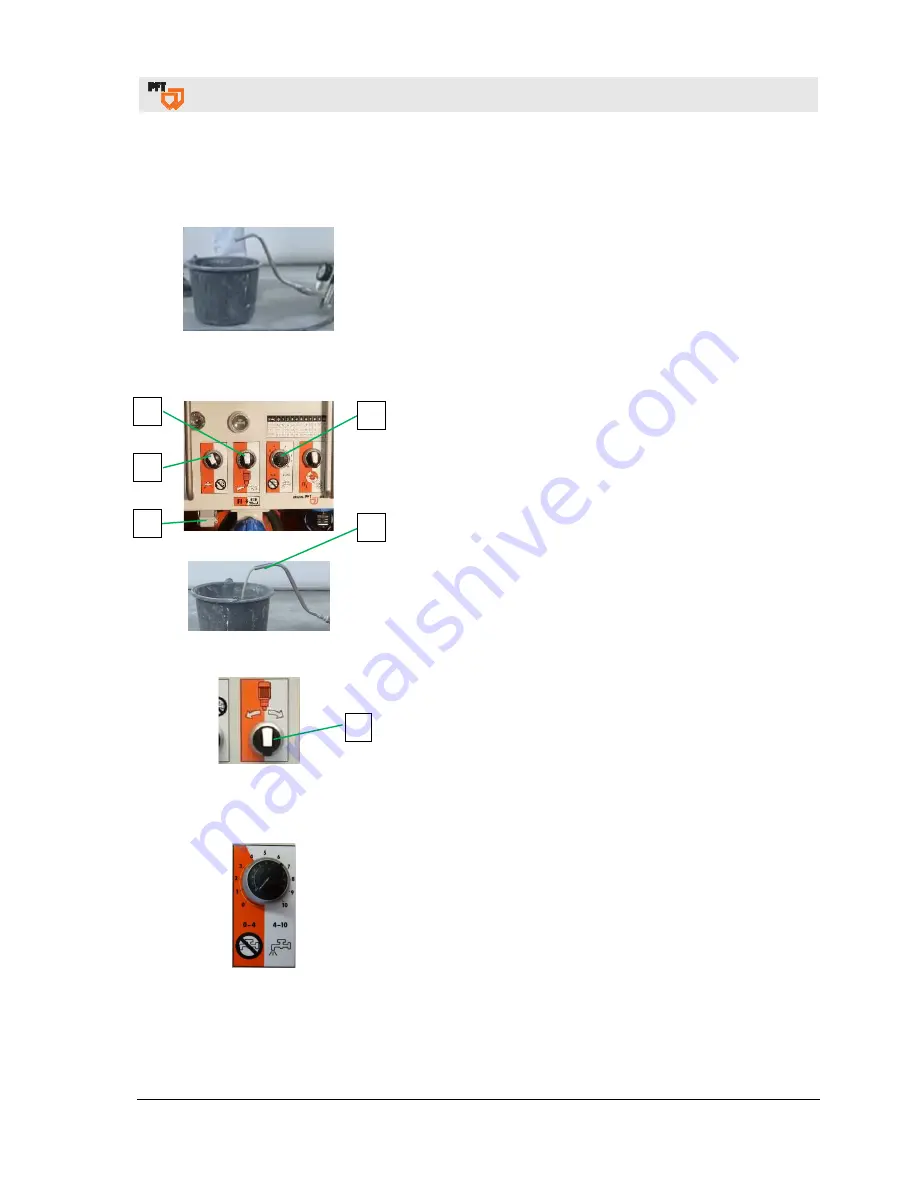
Part 2 EC Declaration of Conformity Overview – Operation
Putting the machine into operation
2020-03-25
35
38 Putting the machine into operation
38.1 Checking the mortar consistency
Fig.53: Consistency inspection pipe
1. Connect consistency inspection tube to the mortar
pressure gauge.
2. Place a bucket or tray below the consistency inspection tube.
Item number: 00099057 Consistency inspection tube 25M-part.
38.2 Switching on the RITMO L plus powercoat with material
Fig. 54: Switching on
1. Turn selector switch (1) left to position “With water”.
2. Turn potentiometer (2) for motor speed / material volume to
position 10 (readjust as required).
3. Dummy plug (3) must be connected to the remote control
socket.
4. Turn selector switch (4) Pump motor directions of rotation to the
right (machine starts).
5. Check material consistency at consistency inspection tube (5).
6. Switch off machine at selector switch (4) (middle position).
7. Remove consistency inspection tube (5) and clean..
Fig. 55: Switching off
Switch off the machine at the selector switch (4) (position
"0").
Remove and clean the consistency test tube.
39 Potentiometer
Fig. 56: Potentiometer
If the RITMO is switched on/off with the remote control within
short time intervals, the mortar consistency will fluctuate.
The solenoid valve opens from 40Hz. This means that no
water can be supplied in the potentiometer positions 1-4.
(Parameter value 11 – 75Hz)
2
5
4
1
3
2