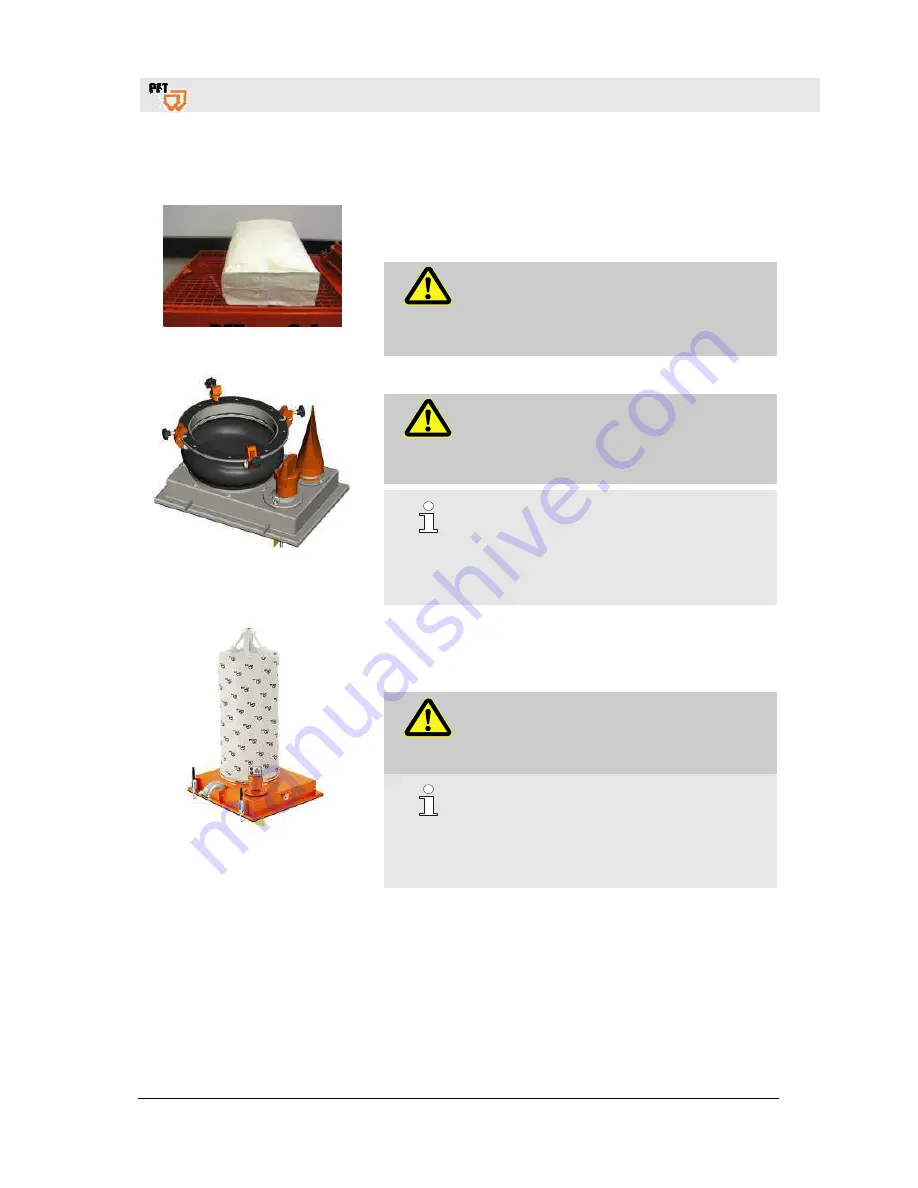
Mixing pump RITMO XL 400V Overview – Operation
Feeding machine with factory dry material
2019-12-11
29
22 Feeding machine with factory dry material
Fig. 43: Sack
Depending on the equipment, the machine can be fed with
sacks, with transfer hood or injection hood.
Feeding with sacked materials:
DANGER!
Danger of injury at sack splitter!
Sharp edges give rise to danger of injury at the
sack splitter.
– Wear safety gloves.
Fig. 44: Transfer hood
Feeding with transfer hood:
DANGER!
Do not open the transfer hood when the
machine is in operation. Switch off the main
reverse switch before opening, and disconnect
power supply.
NOTE:
Feed the mixing pump RITMO XL only with
material. To do this, pull out the dummy
connector or switch off machine via air
pressure control. Start work only when the
filling level indicator shows Full.
Fig. 45: Injection hood
Feeding with injection hood:
Install the injection hood on the adapter injection hood RITMO
XL complete Art. No. 00201619 (accessory).
Ensure that the connection is tight.
DANGER!
Do not open the machine during compressed
air delivery. Switch off the main switch before
opening, and disconnect power supply.
NOTE:
Feed the mixing pump RITMO XL only with
material. To do this, pull out the dummy
connector or switch off machine via air
pressure control. Start work only when the
filling level indicator shows Full.