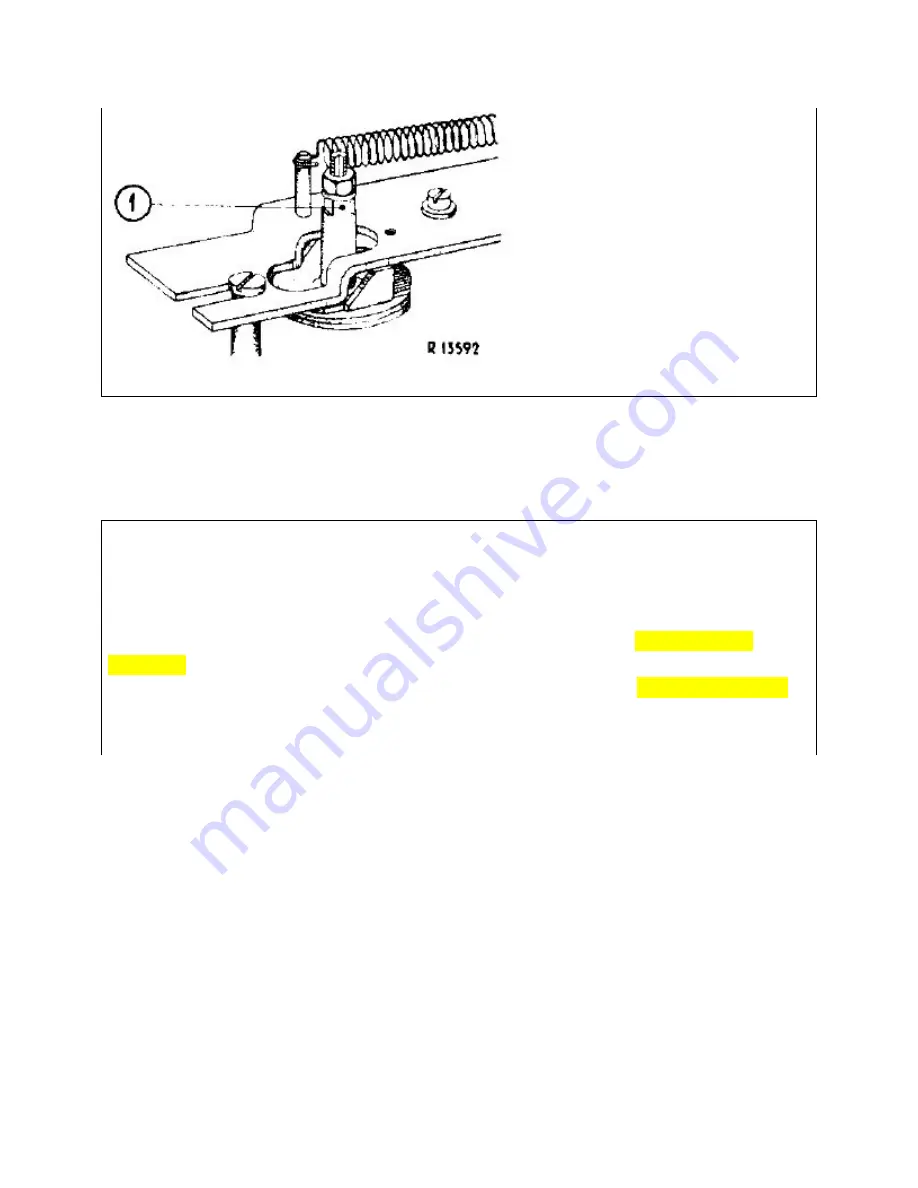
Note:
item ’A’ fig 9 secures here [left end ,top] w 2 screws
XII
THE TURNTABLE REMAINS RUN AFTER THE PU ARM
IS RETURNED ON THE SUPPORT ON THE HEART SWITCH.
The position of the bracket net roll (
1
) is too low. Here, the am of the switch is
not pushed down
sufficiently.
The screw (
2
) by turning on the bracket sliding it toward the top. Dearna tighten the screw
again. It should also be taken to ensure that the caster can rotate easily. Add a
drop of oil if necessary
.
R13568
55
Summary of Contents for AG1000
Page 29: ...See also DSC00130 jg and stitched 00125 00128 and zippy1 fig 6 jpg 29 ...
Page 56: ...56 ...
Page 61: ...Runnells IA usa c60h hotmail com 61 ...
Page 62: ...62 ...
Page 63: ...63 ...
Page 64: ...64 ...
Page 65: ...FIG 8 65 ...
Page 66: ...FIG 8 FIG 9 66 ...
Page 67: ...FIG 9 67 ...
Page 68: ...68 ...
Page 69: ...THERE IS NO 32 THRU 40 WAS NONE 69 ...
Page 70: ...70 ...
Page 71: ...71 ...