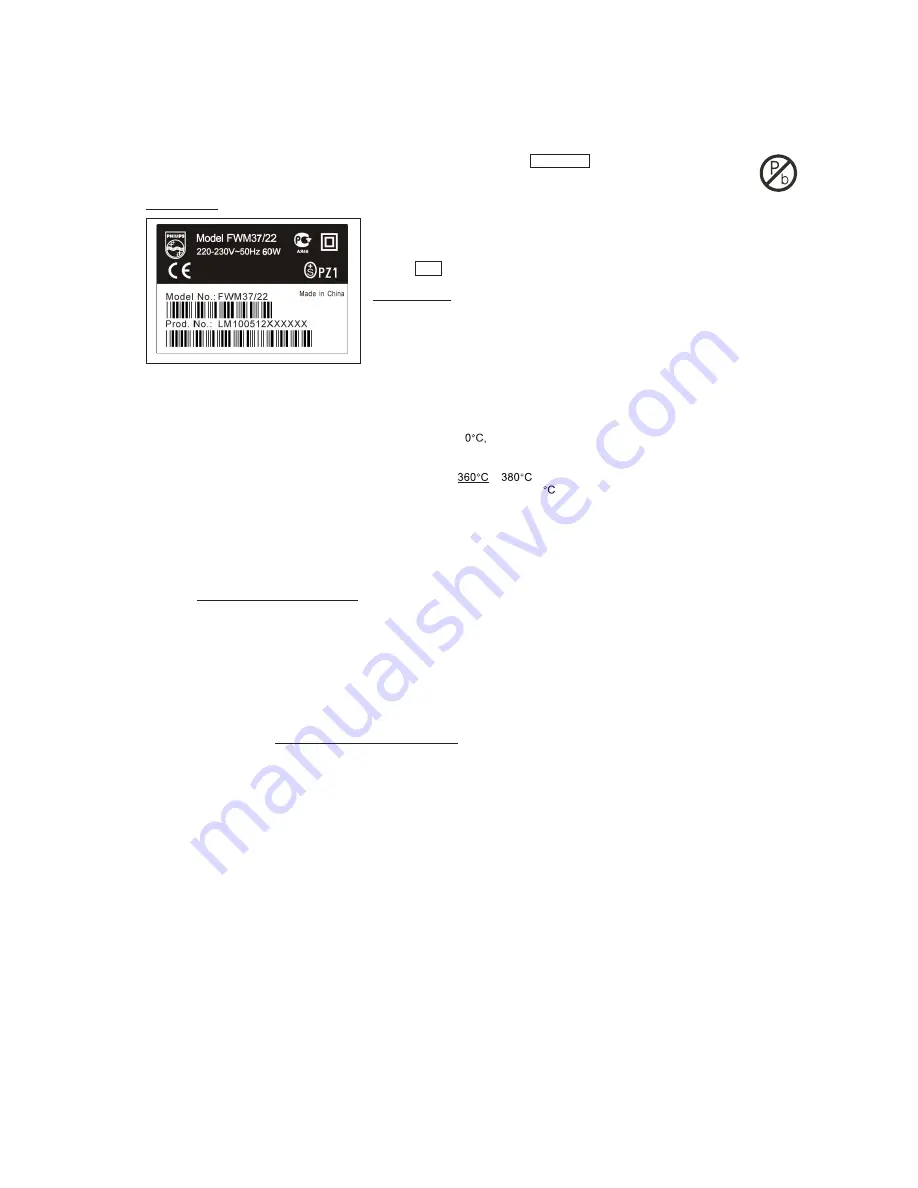
1 - 2
INFORMATION ABOUT LEAD-FREE SOLDERING
Philips CE is producing lead-free sets from 1.1.2005 onwards.
IDENTIFICATION:
Regardless of special logo (not always indicated) one must treat all sets from 1 Jan 2005 onwards, according next rules:
Example S/N:
Bottom line of typeplate gives a 14-digit S/N. Digit 5&6 is the year, digit 7&8 is the week number,
so in this case 2005 wk12
So from 0501 onwards = from 1 Jan 2005 onwards
Im p o rta nt note : In fact also product s of year 2004 must be treated in this way as long as
you avoid mixin g sold er-alloys ( leaded/ lead -free ). So best to always use SAC3 05 and the
higher temperatures belo n g t o t h is.
Due to lead-free technology some rules have to be respected by the workshop during a repair:
•
Use only lead-free solder alloy Philips SAC305 with order code 0622 149 00106. If lead-free solder-paste is required, please contact
the manufacturer of your solder-equipment. In general use of solder-paste within workshops should be avoided because paste is not
easy to store and to handle.
•
Use only adequate solder tools applicable for lead-free solder alloy. The solder tool must be able
o
To reach at least a solder-temperature of 40
o
To stabilize the adjusted temperature at the solder-tip
o
To exchange solder-tips for different applications.
•
Adjust your solder tool so that a temperature around
−
is reached and stabilized at the solder joint. Heating-time of the
solder-joint should not exceed ~ 4 sec. Avoid temperatures above 400 otherwise wear-out of tips will rise drastically and flux-fluid
will be destroyed. To avoid wear-out of tips switch off un-used equipment, or reduce heat.
•
Mix of lead-free solder alloy / parts with leaded solder alloy / parts is possible but PHILIPS recommends strongly to avoid mixed
solder alloy types (leaded and lead-free).
If one cannot avoid or does not know whether product is lead-free, clean carefully the solder-joint from old solder alloy and re-solder
with new solder alloy (SAC305).
•
Use only original spare-parts listed in the Service-Manuals. Not listed standard-material (commodities) has to be purchased at
external companies.
•
Special information for BGA-ICs:
- always use the 12nc-recognizable soldering temperature profile of the specific BGA (for de-soldering always use the lead-free
temperature profile, in case of doubt)
- lead free BGA-ICs will be delivered in so-called 'dry-packaging' (sealed pack including a silica gel pack) to protect the IC against
moisture. After opening, dependent of MSL-level seen on indicator-label in the bag, the BGA-IC possibly still has to be baked dry.
(MSL=Moisture Sensitivity Level). This will be communicated via AYS-website.
Do not re-use BGAs at all.
•
For sets produced before 1.1.2005 (except products of 2004), containing leaded solder-alloy and components, all needed spare-parts
will be available till the end of the service-period. For repair of such sets nothing changes.
• On
our
website
www.atyourservice.ce.Philips.com you find more information to:
∗
BGA-de-/soldering (+ baking instructions)
∗
Heating-profiles of BGAs and other ICs used in Philips-sets
You will find this and more technical information within the "magazine", chapter "workshop news".
For additional questions please contact your local repair-helpdesk.
SERVICE INSTRUCTION
1. Unplug the AC Power cord and connect a wire
between the two pins of the AC Power plug.
2. Set the AC Power switch to the "on" position (keep the
AC Power cord unplugged!).
3. Measure the resistance value between the pins of the
AC Power plug and the metal shielding of the tuner or
the aerial connection on the set. The reading should be
larger than 4.5 Mohm (For U.S. it should be between
4.2 Mohm and 12 Mohm).
4. Switch "off" the set, and remove the wire between the
two pins of the AC Power plug.
Safety regulations require that after a repair, the set must be returned in its original condition. Pay in particular attention to
the following points:
· Route the wire trees correctly and fix them with the
mounted cable clamps.
· Check the insulation of the AC Power lead for external
damage.
· Check the strain relief of the AC Power cord for proper
function.
· Check the electrical DC resistance between the AC Power
Plug and the secondary side (only for sets which have a AC
Power isolated power supply):
•
Check the cabinet for defects, to avoid touching of any
inner parts by the customer.
Summary of Contents for FWV182
Page 2: ...1 1 HANDLING CHIP COMPONENTS ...
Page 6: ...3 1 3 6 ª 6 5 º 9 8 7 1 fi fl CONNECTION AND CONTROLS 1 4 7 3 0 8 9 6 5 2 fl ...
Page 12: ...5 1 5 1 SET BLOCK DIAGRAM ...
Page 13: ...5 2 5 2 SET WIRING DIAGRAM ...
Page 14: ...6 1 6 1 CIRCUIT DIAGRAM FRONT BOARD ...
Page 15: ...6 2 6 2 CIRCUIT DIAGRAM FRONT BOARD ...
Page 16: ...6 3 6 3 LAYOUT DIAGRAM FRONT BOARD ...
Page 17: ...7 1 7 1 CIRCUIT DIAGRAM VCD BOARD ...
Page 18: ...7 2 7 2 LAYOUT DIAGRAM VCD BOARD ...
Page 19: ...8 1 8 1 CIRCUIT DIAGRAM POWER BOARD ...
Page 20: ...8 2 8 2 LAYOUT DIAGRAM POWER BOARD ...
Page 21: ...9 1 9 1 LAYOUT DIAGRAM ANT BOARD LAYOUT DIAGRAM VOL SELECT BOARD ...
Page 22: ...10 1 10 1 CIRCUIT DIAGRAM MAIN BOARD TUNER PART ...
Page 23: ...10 2 10 2 CIRCUIT DIAGRAM MAIN BOARD TAPE PART ...
Page 24: ...10 3 10 3 CIRCUIT DIAGRAM MAIN BOARD ...
Page 25: ...10 4 10 4 LAYOUT DIAGRAM MAIN BOARD ...
Page 26: ...10 5 10 5 LAYOUT DIAGRAM MAIN BOARD ...