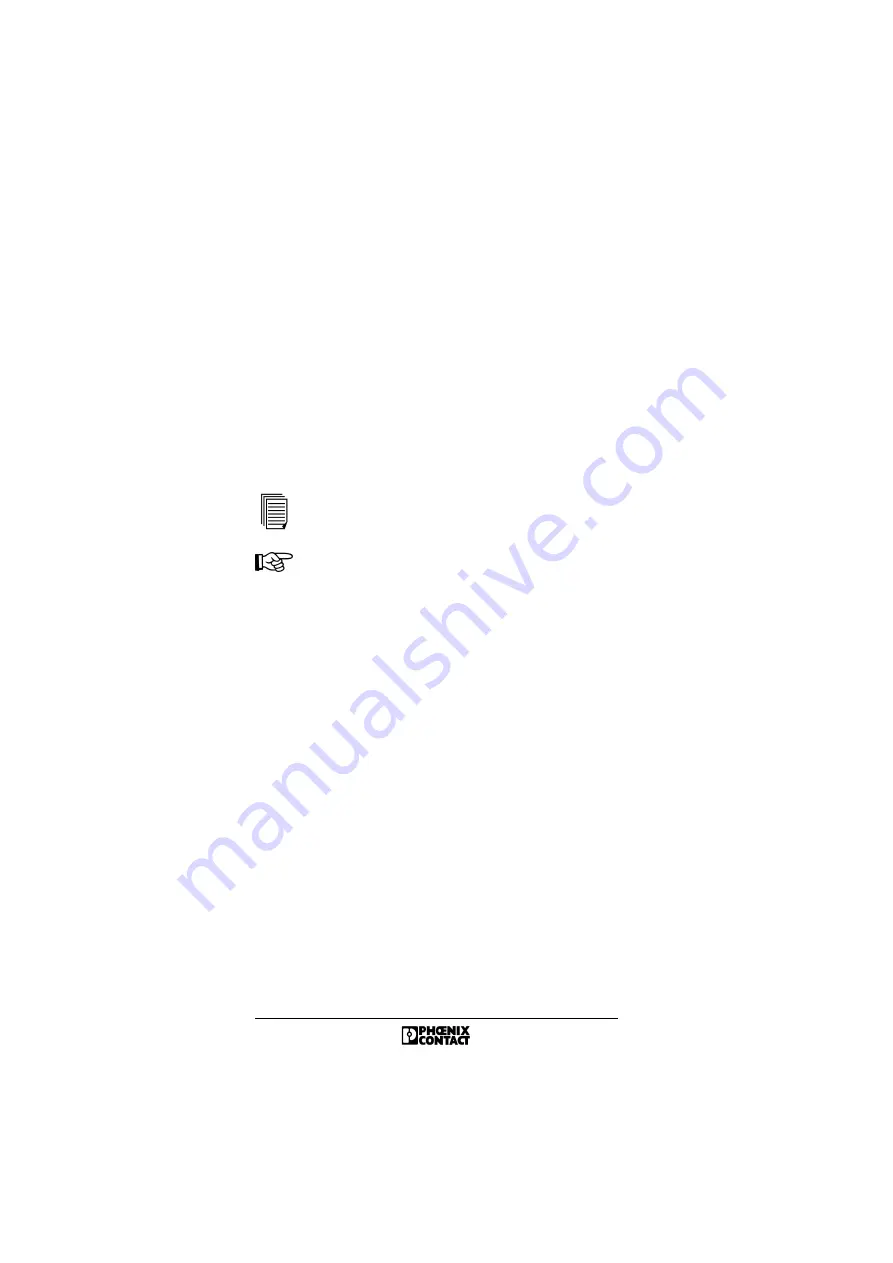
26
5756B
Checking the Connected INTERBUS
Configuration
If the controller board was able to start up the system
successfully, all connected INTERBUS devices are correctly
installed (however, this does not mean that all of the I/O
signals were wired correctly). Please check if the desired
configuration agrees with the one being read-in. The
controller board can be used to check the ID code
(identification code), the position, the device number and the
process data length of each connected INTERBUS device
from the menu-controlled LCD. In addition, you can check the
wiring of inputs. This requires knowledge of how to use the
keypad on the controller board.
Please refer either to the IBS SYS DIAG DSC UM E
Diagnostics Guide or the Appendix to this Quick Start
Guide for further information.
Set the PLC to the STOP state before activating the
test mode.
Please note that the RUN LED on the CPU continues
to flash if you try to set the CPU to the RUN state. In
this case, the controller board does not indicate to the
CPU that it is "ready".
The CPU then starts a monitoring time for ready signal
from modules internally. During this time, the CPU
behaves as described above.
During controller board test mode, the CPU cannot be
accessed via the MPI interface. Once the system has
undergone another POWER-UP without activation of
the INTERBUS test mode, the diagnostic buffer of the
CPU indicates that the modules are not ready for
operation.
Any parameterization which may be stored on the
parameterization memory is not activated during test
mode.
To return to normal system mode, start the controller board
without pressing the test mode button using a PLC
POWER-UP.