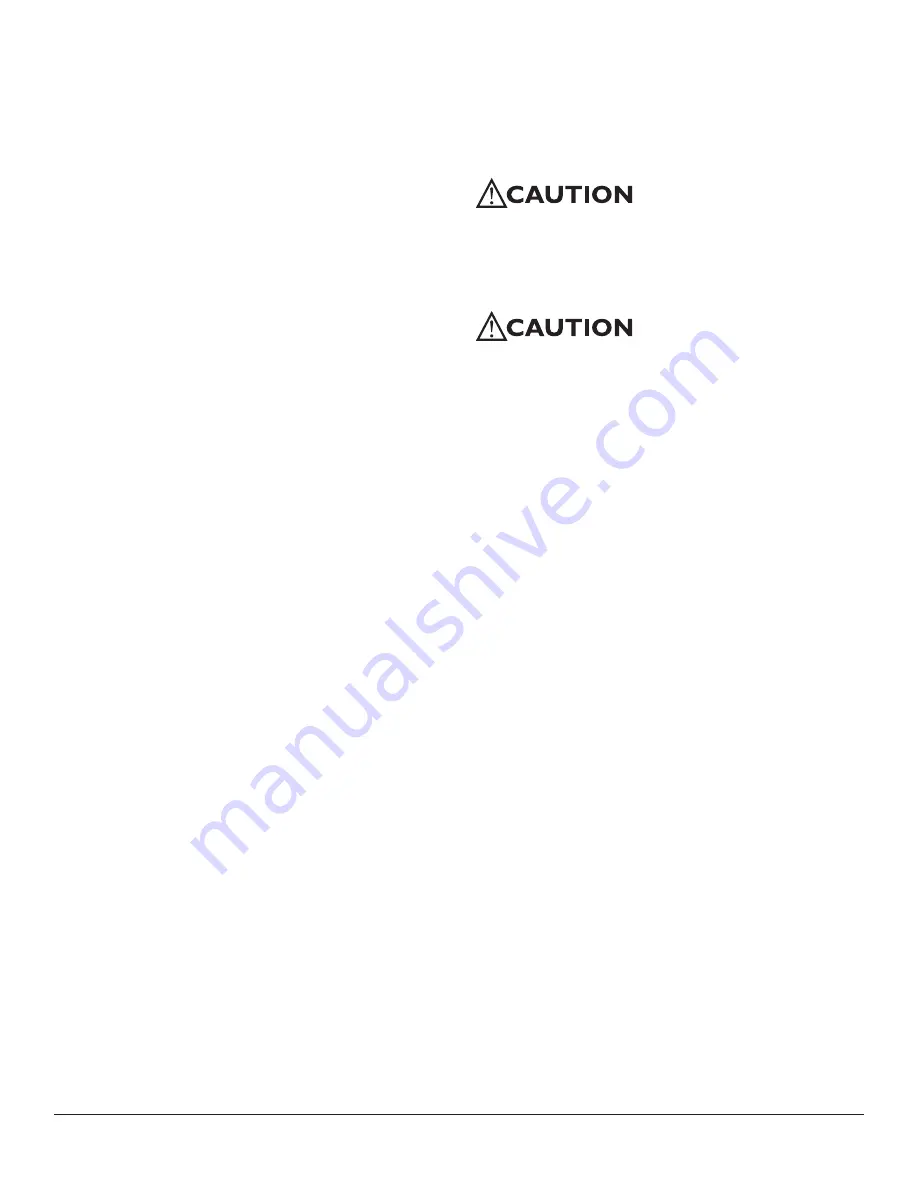
6
www.UsePhoenix.com • sales@UsePhoenix.com
Toll-Free 1-800-533-7533
the point they create a system problem.
Three aluminum (20”x20”x2”) air filters must be checked
regularly. Two filters are located near the process air inlet.
The other one is located near the reactivation air inlet.
Wash the filters with fresh water. Clean the filter from the
downstream side, forcing debris toward the filter inlet. Dry the
filters completely before installing them in unit. Replacement
filters can be ordered from the factory or purchased locally if
available.
DO NOT
operate the unit without the filters or with less
effective filters as the desiccant wheel inside the unit will
become clogged and require disassembly to clean.
6.4 Blower and Motor
Blower and motor bearings are permanently lubricated and
do not require maintenance. Blower wheel - inspect wheel
blades for accumulation of dust and dirt. Clean thoroughly
with compressed air and or vacuum. The wheel should
not strike the housing or the inlet ring. Make sure wheel is
rotating in the proper direction.
6.5 Drive Motor
The media drive motor is permanently lubricated and
requires no maintenance.
6.6 Rotor Drive Chain
A spring loaded tensioner keeps the chain sufficiently
tensioned. Check the chain for signs of excessive wear.
Replace as necessary. If additional tension is required, simply
tighten the nuts on the tension springs as required.
6.7 Seals
High temperature seals separate the process and
reactivation compartments. Normally, the seals will not
require service or replacement. However, should damage
occur, or if poor performance as the result of an air leak is
suspected, the following inspection must be performed to
determine whether the seals should be replaced:
Inspection:
1) Turn the unit off and remove the access covers.
2) Visually inspect for gaps between the desiccant media
and the seals.
3) If significant gaps, wear, or damage are observed,
the seal needs to be replaced.
6.8 Desiccant Media
The silica gel desiccant media supplied with the dehumidifier
will last indefinitely under ideal conditions. Due to the nature
of desiccants they make very good filters. The life of the
desiccant is directly related to the airborne contaminates
passed through it. Atmospheric contaminants, exposure to
acidic gases/or air streams, and contact with petroleum
based airborne particles can reduce the efficiency of the
desiccant media. The preferred method of cleaning is to
blow dust out with compressed air. Proper filtration and
preventing contact with chemicals will greatly improve the life
of the desiccant. Inspect the face of the media to see that no
surface damage has occurred. If damage is noticed, please
contact Therma-Stor at 1-800-533-7533 for assistance. The
rotor should turn smoothly upon the shaft, if not check the
support bearings.
Servicing the Phoenix 4800E with its high voltage
circuitry presents a health hazard which could result in
death, serious bodily injury, and/or property damage. Only
qualified service people should service this unit.
ELECTRICAL SHOCK HAZARD: Electrical power must be
present to perform some tests; these tests should be
performed only by a qualified service person.