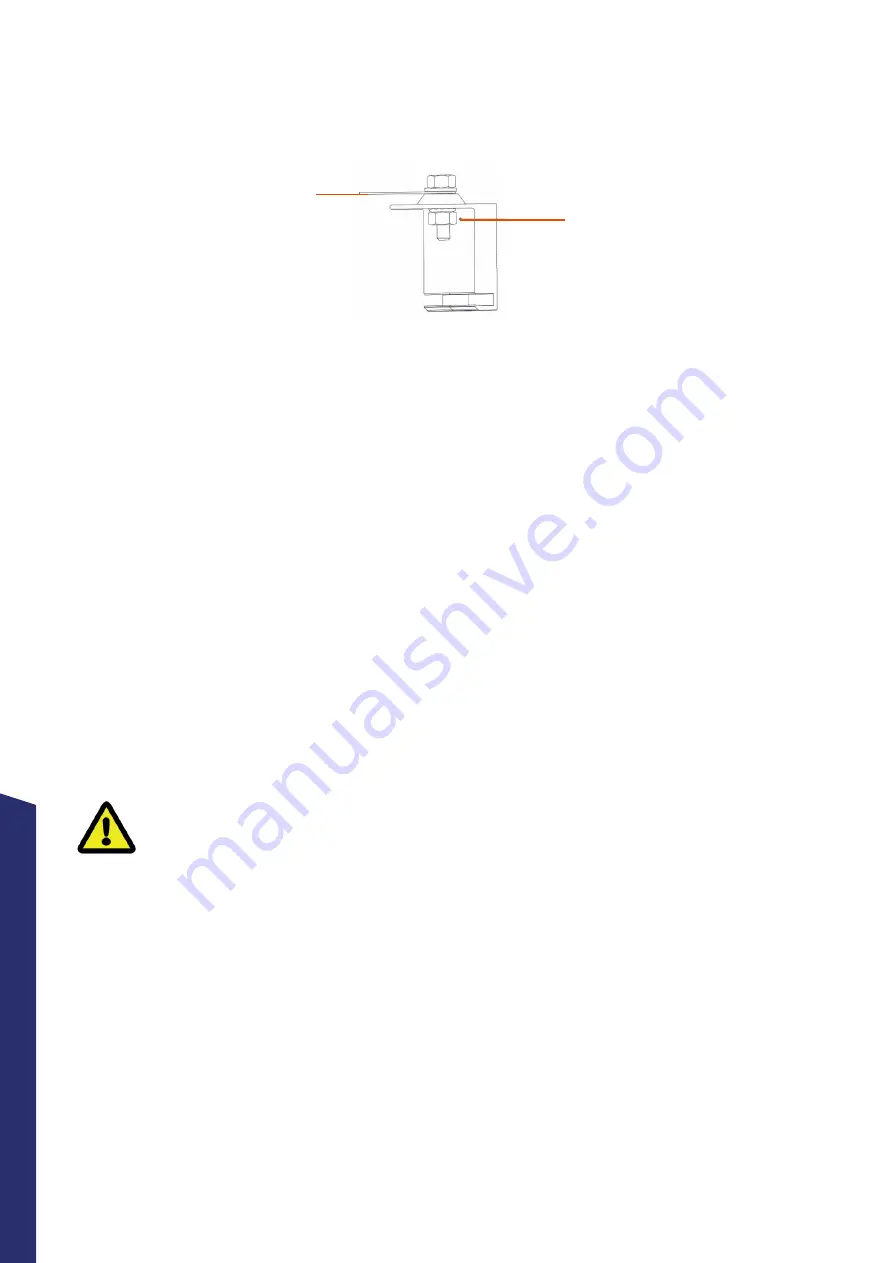
D84-P06-01 GB R3
21/04/2021
www.photowatt.com
11
•
A grounding kit containing an M5 (3/16“) SS cap
bolt, an M5 (3/16“) SS flat washer, an M5 (3/16“) SS
cup washer, and an M5 (3/16“) SS nut (with teeth) is
used to attach copper grounding wire to a pre-drilled
grounding hole on the frame (see image above). The
grounding holes are located at the upper and lower
edges of the long side frame, close to the module
short sides.
•
Mounting rail designs should be such to allow easy
access to the grounding holes located on the long
side of the frame, in order to enable the equipment
grounding function when required.
•
Place the wire between the flat washer and the cup
washer. Ensure that the cup washer is positioned be-
tween the frame and the wire with the concave side
up to prevent galvanic corrosion. Tighten the bolt
securely using the SS toothed nut. A wrench may be
used to do this. The tightening torque is 3-7 Nm (2.2-
5.2 ft-lbs).
6.0
MOUNTING INSTRUCTIONS
The applicable regulations pertaining to work
safety, accident prevention and securing the
construction site must be observed. Workers
and third party personnel shall wear or install
fall arrest equipment. Any third party need to be protect-
ed against injuries and damages.
•
The mounting design must be certified by a regis-
tered professional engineer. The mounting design
and procedures must comply with local codes and
requirements from all relevant authorities.
•
The loads described in this manual correspond to
test loads. For installations complying with UL 1703
or UL 61730 and IEC 61215-2:2016, a safety factor of
1.5 should be applied for calculating the equivalent
maximum authorized design loads. Project design
loads depend on construction, applicable stan-
dards, location and local climate. Determination of
the design loads is the responsibility of the racking
suppliers and/or professional engineers. For detailed
information, please follow local structural code or
contact your professional structural engineer.
1. To fix the wire between the
flat washer and cup washer,
place the cup washer
(concave side up) between
the frame and the wire.
2. Then tighten the bolt
using the toothed nut.
•
Use appropriate corrosion-proof fastening materials.
All mounting hardware (bolts, spring washers, flat
washers, nuts) should be hot dip galvanized or stain-
less steel.
•
Use a torque wrench for installation.
•
Do not drill additional holes or modify the module
frame. Doing so will void the warranty.
WHEN CLAMPS ARE USED AS FIXING MATERIAL
•
Install and tighten the module clamps to the mount-
ing rails using the torque stated by the mounting hard-
ware manufacturer. System designer and installer are
responsible for load calculations and for proper de-
sign of support structure. It is recommended to use
a torque wrench for installation. Tightening torques
must respectively be within 16~20 Nm (11.8~14.75 ft-
lbs) for M8 x 1.25-Grade 8.8 (5/16”-18 Grade B7) gal-
vanized or A2-70 stainless steel coarse thread bolts,
depending on bolt class. The yield strength of bolt
and nut should not be less than 450 MPa.
•
Clamp material should be anodized aluminum alloy
or steel of appropriate grade.
•
Clamp positions are of crucial importance for the re-
liability of the installation, the clamp centerline must
only be positioned within the authorized position
ranges indicated below, depending on the configu-
ration and load.
GROUNDING METHOD:
BOLT + TOOTHED NUT + CUP WASHER