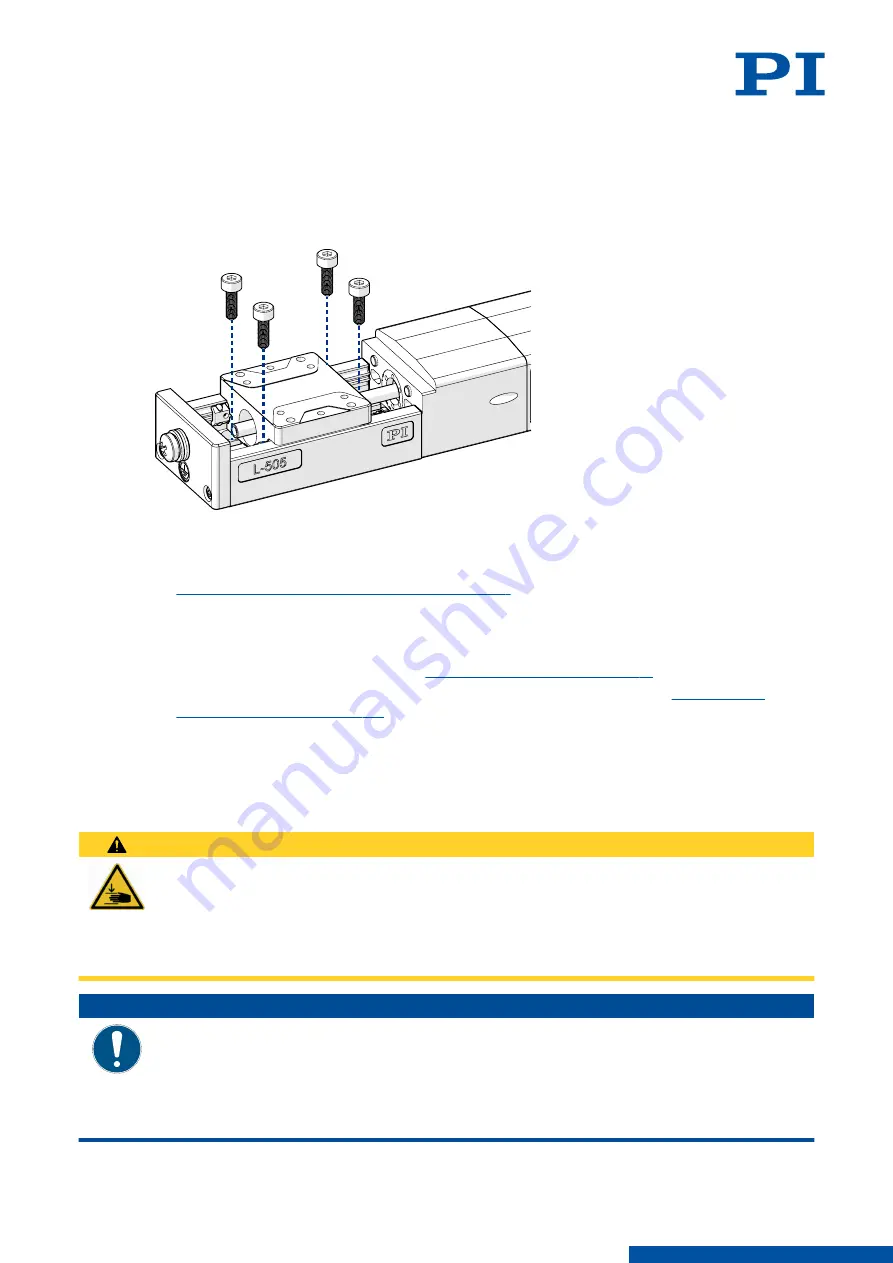
6
Installation
6.1
Mounting the L-505.021212
Overview
Figure 4: Mounting the L-505.021212 onto an underlying surface
Tools and Accessories
■
Screw set for mounting the L-505.021212 (p. 10)
■
Suitable screwdriver
Requirements
✓
You have read and understood the
general safety instructions (p. 8)
✓
You have provided a suitable surface with the holes necessary for the
required, locating pins (p. 35)
■
The flatness of the surface is
≤
10 μm.
■
For applications with large temperature changes: The surface should have the same or
similar thermal expansion properties as the L-505.021212.
✓
You have accounted for the space required to route cables without bending and
according to regulations.
CAUTION
Risk of crushing by moving parts!
Risk of minor injuries from crushing between the moving parts of the L-505.021212 or the
load and a fixed part or obstacle.
►
Use safeguards to protect limbs in areas where they could be caught by moving parts.
►
Maintain the safety distances according to DIN EN ISO 13857 when installing protective
structures.
NOTICE
Damage due to collisions!
Collisions can damage the L-505.021212, the load to be moved, and the surroundings.
►
Make sure that collisions are not possible between the L-505.021212, the load to be
moved, and the surroundings in the motion range of the L-505.021212.
►
Do not place any cables or other objects in areas where they could be caught by moving
parts.
6 INSTALLATION
L505M0015EN
‒
3/18/2020
14
M O T I O N | P O S I T I O N I N G