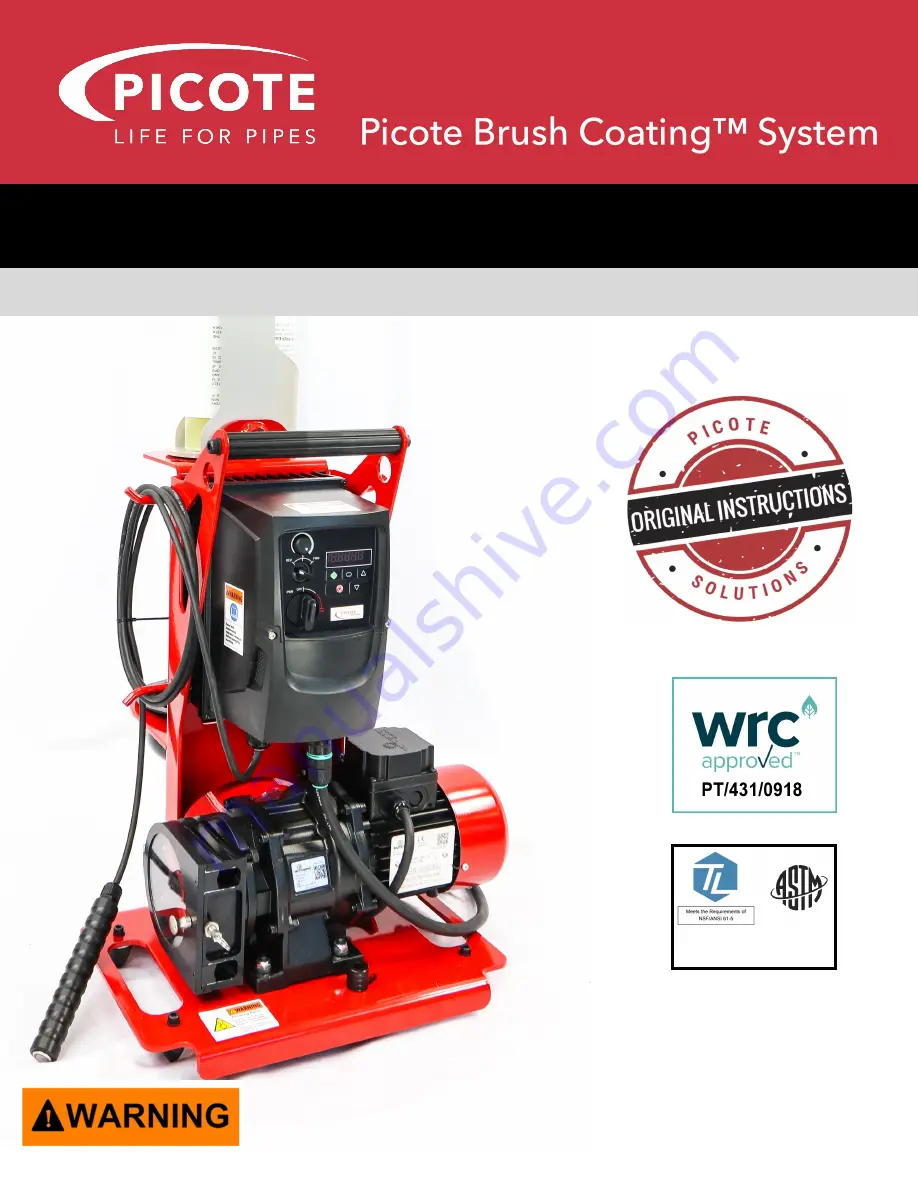
Picote Solutions Oy Ltd
www.picoteinstitute.com
MINI CLEANER
MINI MILLER 8/16 | MINI C 8/16
MINI CLEANER
MINI MILLER 8/16 | MINI C 8/16
MINI COATING PUMP
OPERATION, SAFETY & INSTALLATION MANUAL
This operations manual is for the Picote Brush Coating
™
System using the Mini Coating Pump and covers the
equipment as well as the application process including the DC1000E 100% Solids Epoxy and Fast Cure Resins.
These instructions are for your personal safety. Always ensure that you have
read and understood these instructions before using the Picote Brush Coating
™
System.
DC1000E Resin Certifications