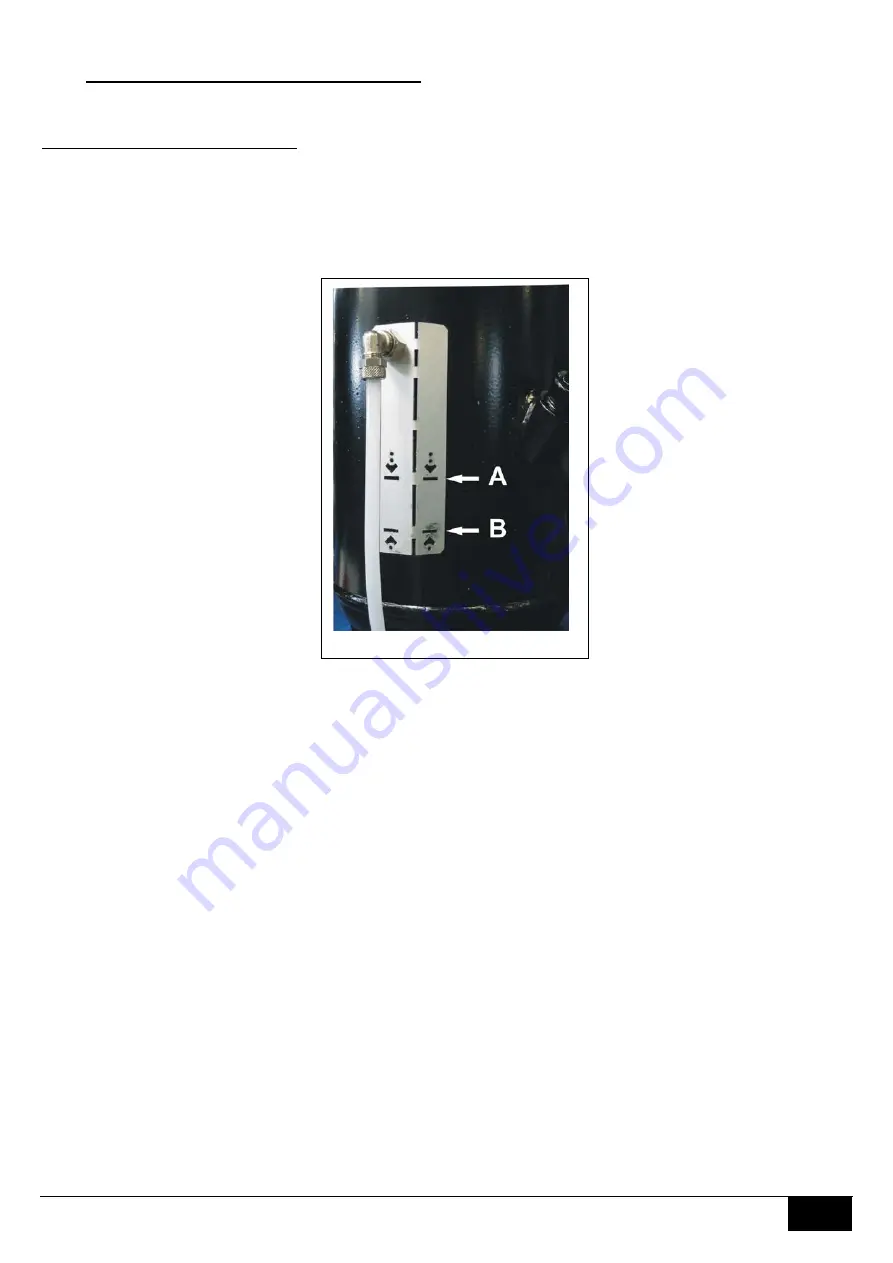
Operating instructions (translation from original IT)
Cod. OQ7_5ARG078EN
Emiss. 18-07-08 Rev. 5- Agg. 20-04-16
47
25.2
CHECKING AND TOPPING UP THE OIL LEVEL
N.B.: If the oil level is below the reference mark “B”, top up the oil.
Always check the oil level with the machine switched off.
Procedure to be followed to top up the oil:
1)
Top up with 0.5 litre of oil
2)
Start the compressor and let it run for sufficient time (5 minutes)
3)
Switch off the compressor and check the oil level. The oil level must be between the 2 reference marks. If the oil level is still
below the reference mark “B”, top up with another 0.5 litre.
4)
Start the compressor and let it run for sufficient time (5 minutes)
5)
Switch off the compressor and check the oil level. If the oil level is still below the reference mark “B”, repeat phases 1, 2 and
3.
NOTE
:
Each time you check the oil when the machines is stopped you may see that the level varies. The important thing is that
the variation must be between the 2 reference marks (“A” and “B” fig.11).
Fig.11