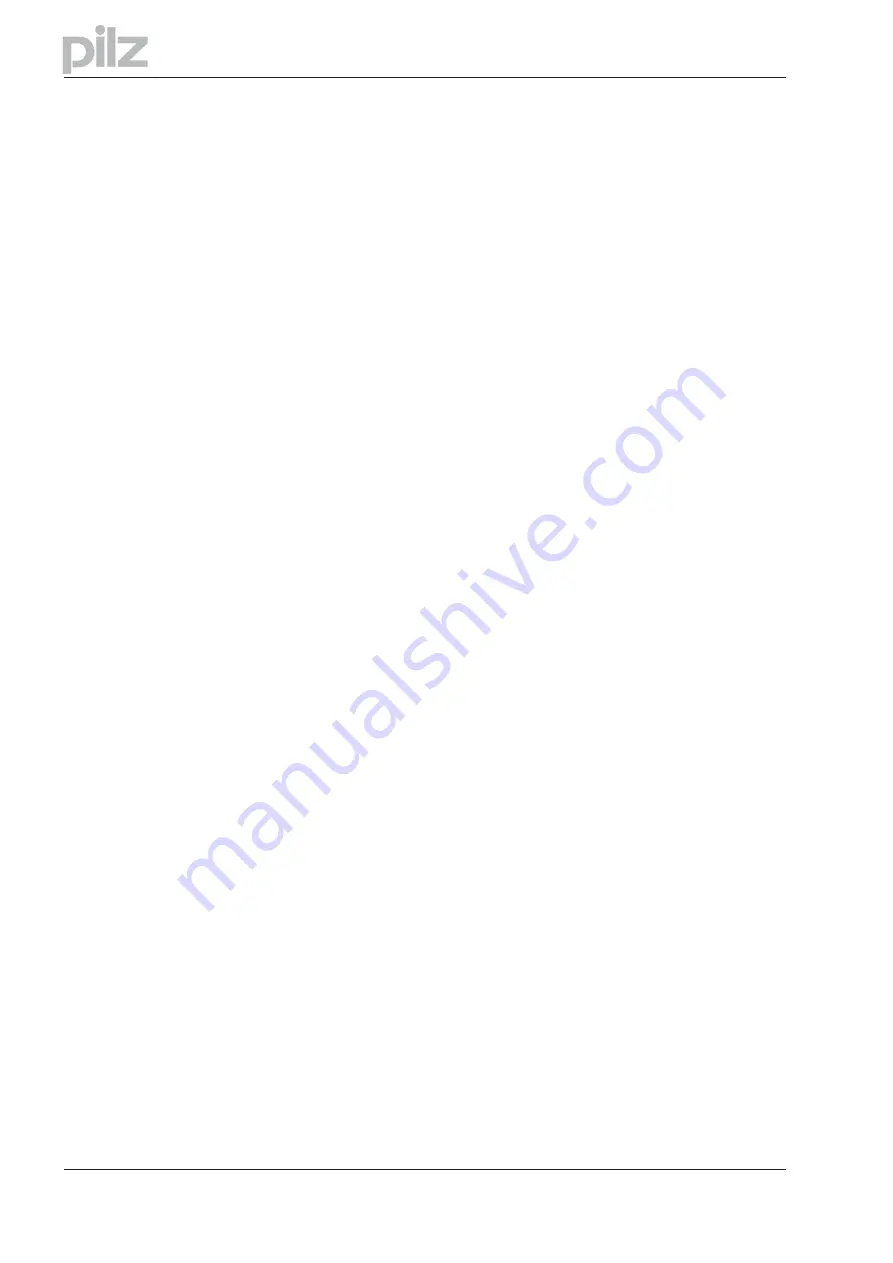
5.2.2
Profile parameters
5.2.2.1
PNU 904/911: PPO-type write/read
These parameters describe the numbers of the supported PPO-types write und read.
Since only PPO-type 2 is supported (see Chapter 4), this parameter is always set to 2.
5.2.2.2
PNU 918: PROFIBUS - node addresse
With this parameter the PROFIBUS - node address of the drive can be read.
You can alter the node address (station addres in a PROFIBUS network) in different ways:
l
With the keys in the front panel (see installation manual)
l
With the setup software PDrive on the screen page "Basic setup"
l
Via the serial interface with the sequence of ASCII-commands:
ADDR nn
Þ
SAVE
Þ
COLDSTART (mit nn = Adresse)
The range of addresses can be extended from 1..63 to 1..127 with the ASCII-command MDRV.
Page 22
User manual PROFIBUS DP PMCtendo DD4
5 Using the parameter channel