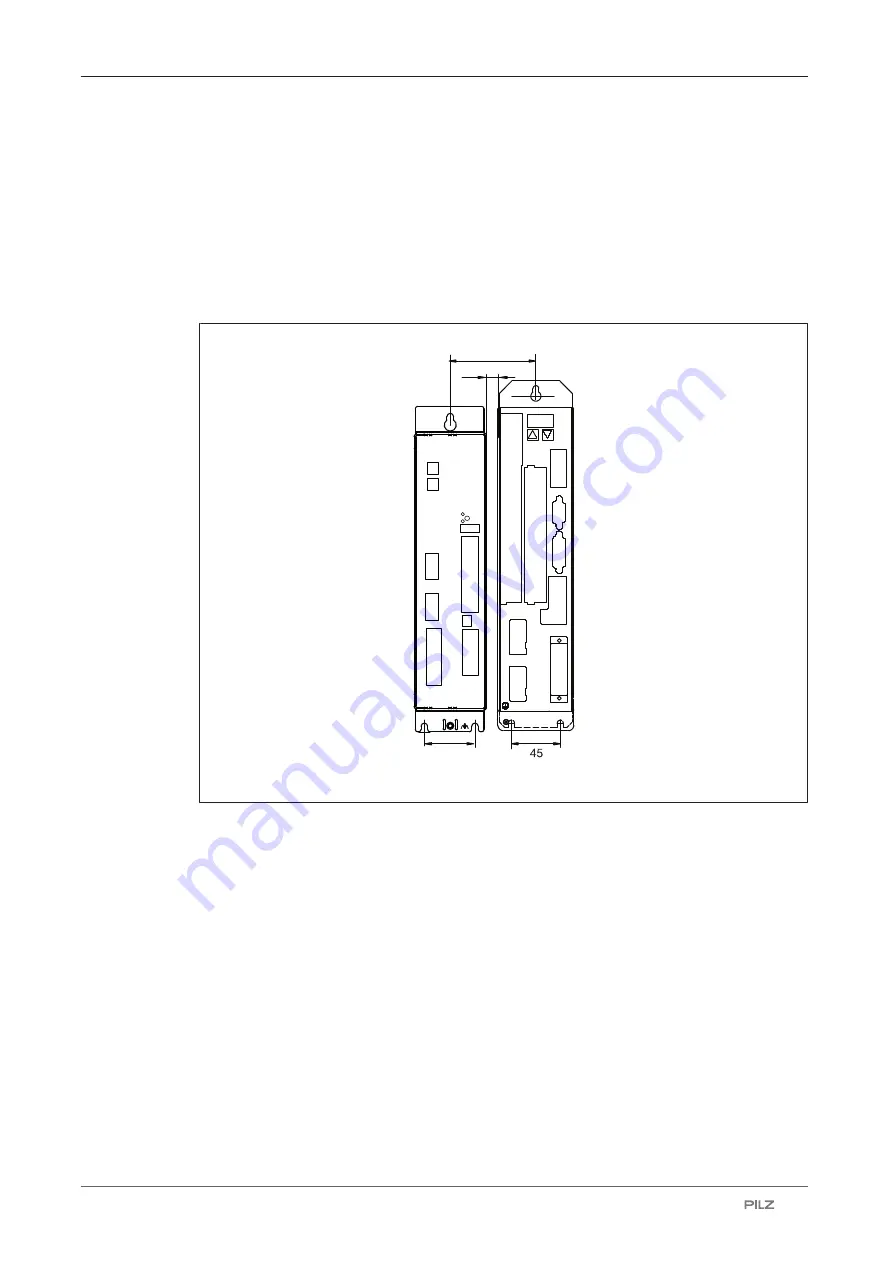
Installation
Operating Manual PMCprimo MC
1003813-EN-03
| 27
5.3
Installing the unit
}
Installation materials: 3 hexagon socket cylinder head screws DIN 912, M5
}
Required tool: Hexagonal wrench 4 mm
Follow the instructions below:
}
Drill M5 holes in the control cabinet's mounting plate, as shown in the illustrations.
Attach the device to the control cabinet's mounting plate with a minimum distance of >5 mm
to the adjacent servo amplifier.
42
>70
>5
PMCprimo MC PMCprotego D.01
Fig.: Installing the motion control system next to a servo amplifier