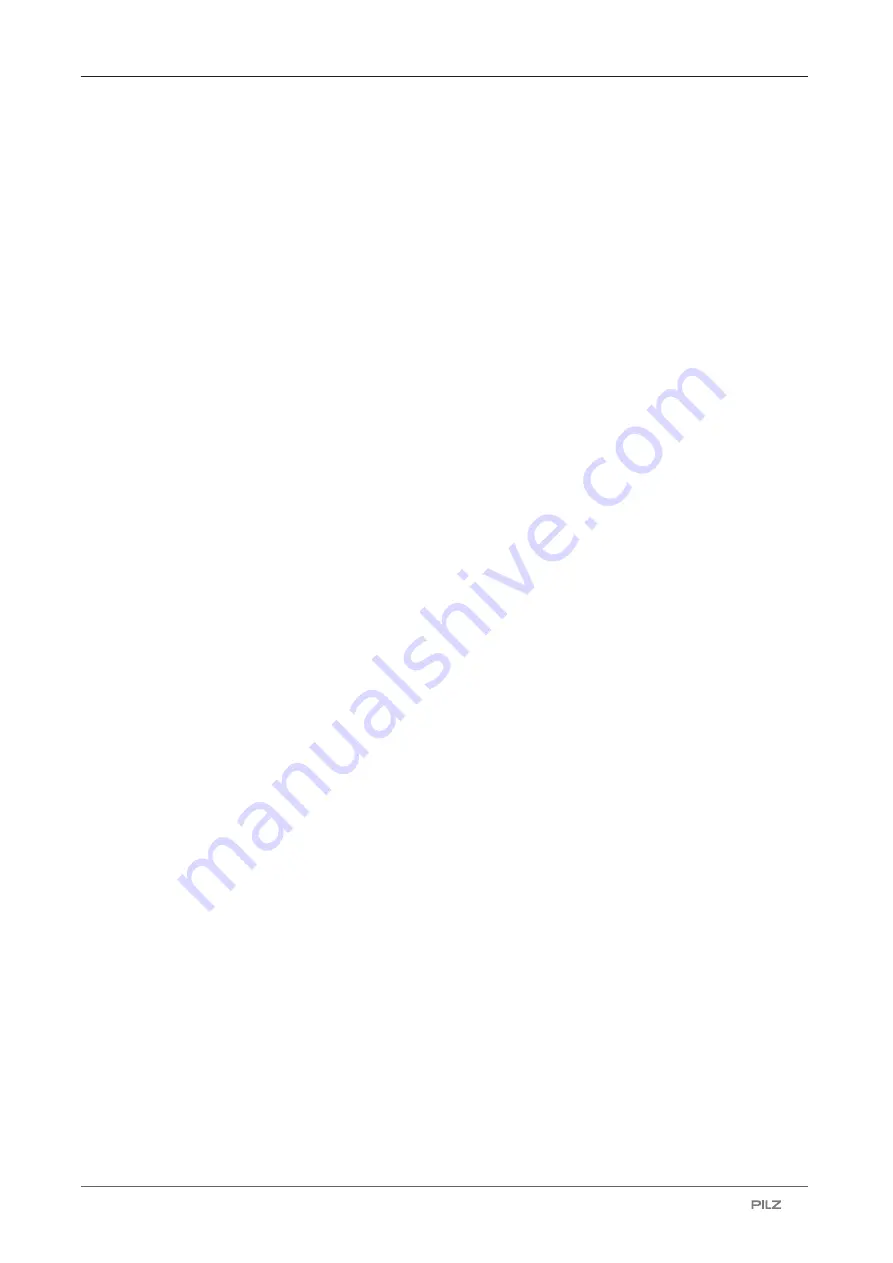
Unit features
Operating Manual PMD s10
22092-EN-05
| 9
3
Unit features
}
Relay outputs:
– 2 auxiliary changeover contacts (C/O)
}
Analogue output for current and voltage
}
Galvanic isolation of analogue outputs
}
Automatic measuring range is set automatically for current and voltage
}
The following unit parameter settings are menu-driven and infinitely variable via a display
and rotary knob with key function (turn and push):
– Maximum true power
– Switching threshold for underload and overload
– Warning threshold
– Monitoring reaction time
– Start-up suppression time
– Allocation of switching threshold to relay
– Hysteresis of the switching thresholds
– Automatic/manual reset
– Range selection for Uout and Iout
– Offset for Uout and Iout
– Relay function norm. on/off
– CT 1 : 1 … 1000 : 1
– VT 1 : 1 … 100 : 1
}
LED display for:
– Supply voltage
– Switching threshold for overload
– Switching threshold for underload
– Output 1
– Output 2
– Error
}
Display for measured value indicator, diagnostics and menu navigation
}
Operating cycle counter for K1 and K2
}
Diagnostics: Umax and Imax
}
Display of operating hours and load hours (resettable)
}
Device parameters can be saved to chip card (write)
}
Device parameters can be restored from the chip card (load)
}
Suitable for use with frequency-controlled drives
}
Suitable for current transformers
}
Suitable for voltage transformers