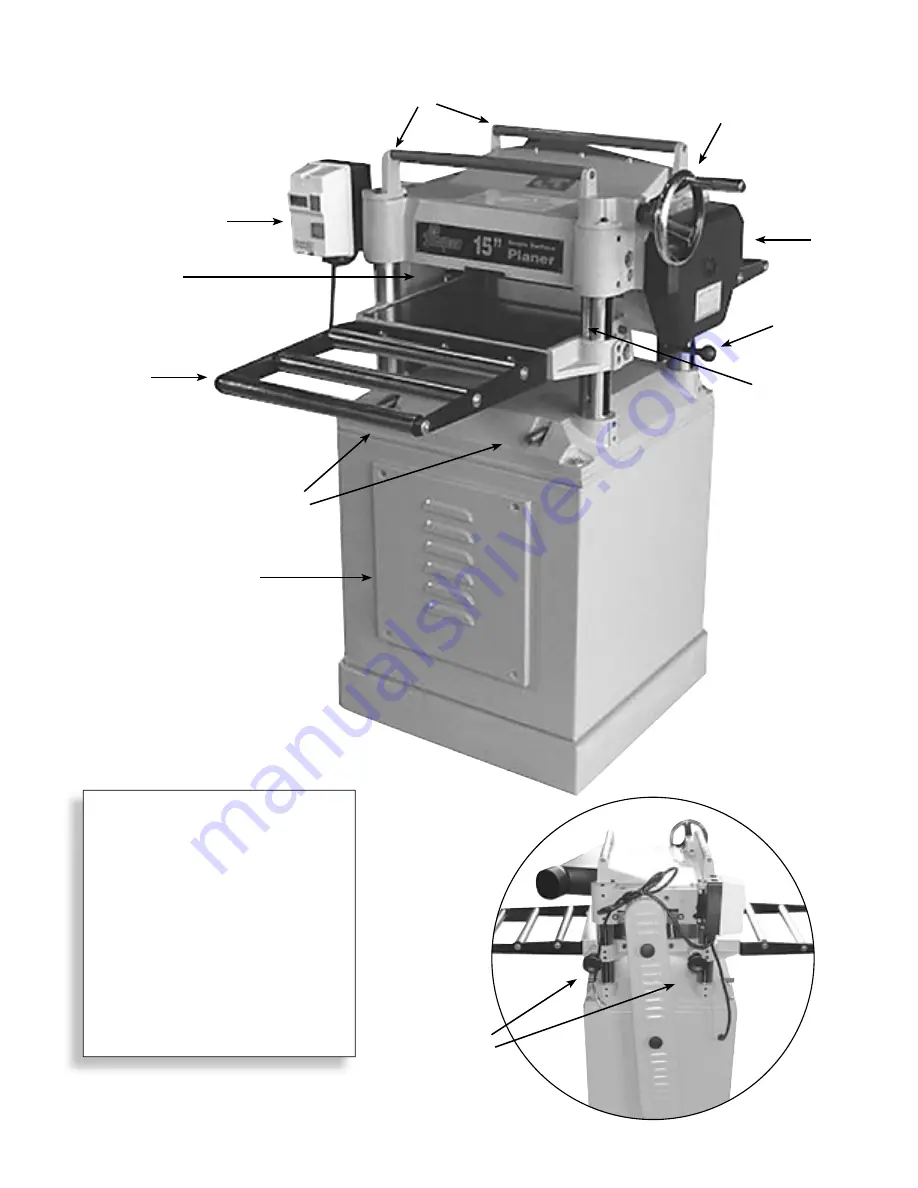
8
© 2006 Pioneer Supply International
8
© 2006 Pioneer Supply International
© 2006 Pioneer Supply International
9
A Magnetic Switch
B Return Rollers
C Table Height Hand wheel
D Gearbox
E Extension Wing
F Table Height Scale
G Speed Control Knob
H Table Locks -
Figure 2
I Lifting Bars
J Motor Access Cover
K V-Belt Cover
A
B
C
D
E
F
G
H
I
J
K
Parts Identifi cation - PNR 14-150
Figure 1
Figure 2
Summary of Contents for PNR 14-150
Page 4: ...4 2006 Pioneer Supply International 4 2006 Pioneer Supply International ...
Page 5: ... 2006 Pioneer Supply International 5 ...
Page 6: ...6 2006 Pioneer Supply International 6 2006 Pioneer Supply International ...
Page 28: ...28 2006 Pioneer Supply International 28 2006 Pioneer Supply International ...
Page 29: ... 2006 Pioneer Supply International 29 ...
Page 30: ...30 2006 Pioneer Supply International 30 2006 Pioneer Supply International ...