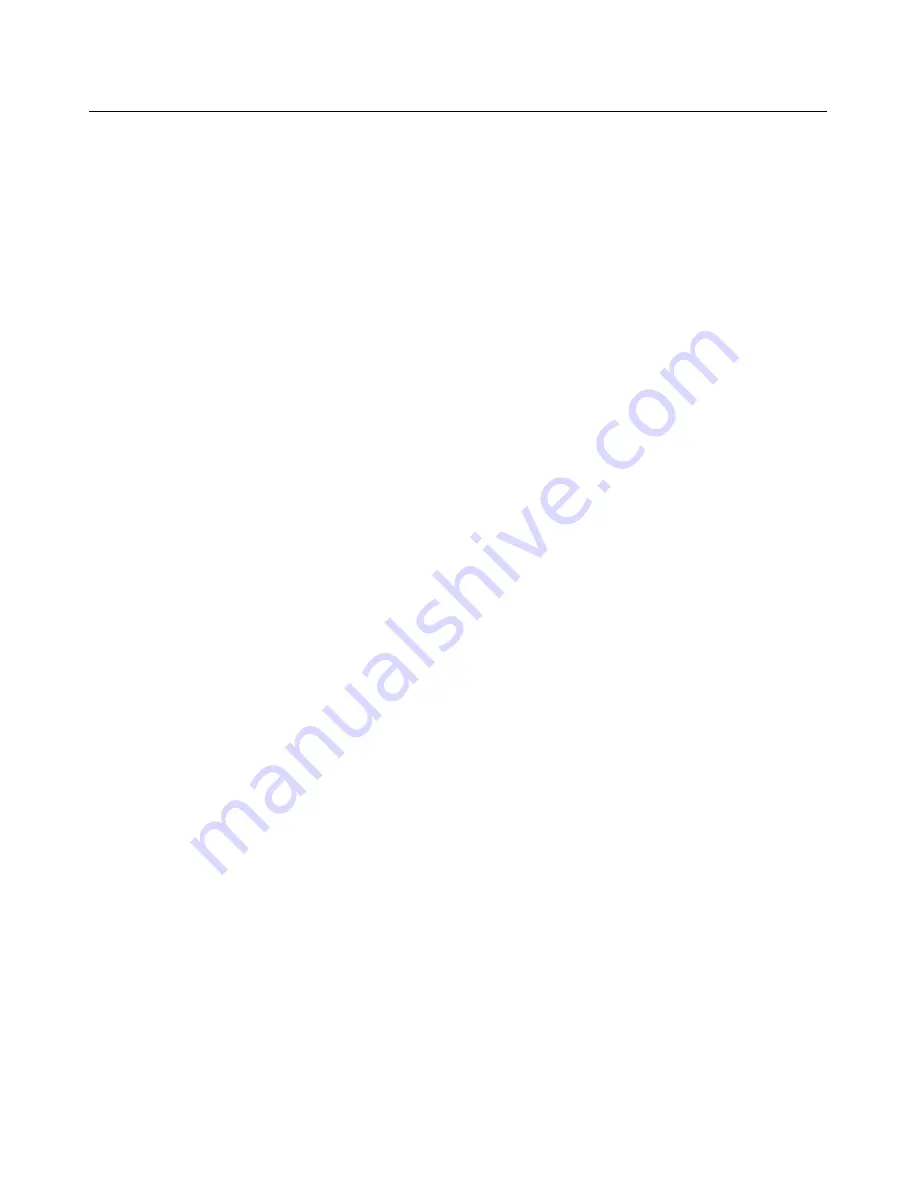
TABLE III-I. INSPECTION REPORT (cont)
NOTES:
1.
Refer to last card of the Piper Price List - Aerofiche, for a checklist of current revision dates to Piper
Inspection Reports and Manuals.
2.
Piper service bulletins are of special importance and Piper considers compliance mandatory. Piper
service letters are product improvements and service hints pertaining to servicing the airplane and should
be given careful attention.
3.
Inspections given for the Lycoming powerplant are based on the engine manufacturer’s operator’s manual
(Lycoming Part No. 60297-12) for this airplane, dated August 1973. Any changes issued to the engine
manufacturer’s operator’s manual after this date shall supersede or supplement the inspection outlined in
this report.
4.
Inspections given for the (Continental Part No. X-30512) for this airplane, dated June 1976. Any
changes issued to the engine manufacturer’s operator’s manual after this date shall supersede of
supplement the inspection outlined in this report.
5.
Replace as required or at engine overhaul. (Refer to latest revision of Hartzell Service Letter 61.) For
engine overhaul, refer to latest revision of one of the following: Lycoming Service Instructions No. 1009,
for commended engine overhaul period, or Continental Service Bulletin M86-6 Rev. 1 , for
recommended engine overhaul period.
6.
Replace flexible oil hoses at three calendar years or 1000 hours, whichever occurs first.
7.
Check throttle body attaching screws for tightness; the correct torque for these screws is 40 to 50 inch
pounds
8.
Rotate spark plugs form upper to lower positions and vice-versa to lengthen plug service life.
9.
At every 400 hours of engine operation, remove the rocker box covers and check for freedom of valve
rockers when valves are closed. Look for evidence of abnormal wear or broken parts in the area of the
valve tips, valve keepers, springs and spring seals. If any indications are found, the cylinder and all of its
components must be removed (including the piston and connecting rod assembly) and inspected for
further damage. Replace any parts that do not conform with limits shown in the latest revision of
Lycoming’s Service Table of Limits No. SSP1776.
10.
Check cylinders for evidence of excessive heat which is indicated by burned paint on the cylinders. This
condition is indicative of internal damage to cylinder(s) and, if found, its cause must be determined and
corrected before the aircraft is returned to service. Heavy discoloration and appearance of seepage at the
cylinder head barrel attachment area is usually due to emission of thread lubricant used during assembly
of the barrel at the factory, or by slight gas leakage which stops after the cylinder has been in service for
awhile. This condition is neither harmful nor detrimental to engine performance and operation. If it can
be proven that leakage exceeds these conditions, the cylinder must be replaced.
11.
If the altimeter is damaged, defective or inaccurate, work must be done by an FAA approved instrument
repair facility only. A logbook entry must be made.
12.
Refer to latest revision of Continental Motors Service Bulletin M84-17.
13.
The compressor oil level should not be checked unless the system has been opened, or a Freon leak
occurred which requires an addition of Freon to the system.
14.
Aircraft must be blown to check the landing gear system in accordance with instructions outlined in
Section VI, of the Service Manual. (Refer to latest revision of Piper Service Bulletin 810).
15.
For operation above 12,000 feet, more frequent ignition system maintenance is required. (Refer to latest
revision of Continental Service Bulletin M78-8).
16.
On Continental installations check torque of mounting bolts.
17.
Maintain cable tensions specified in Section V of this Service Manual.
Revised: 2/13/89
1D15
* CHEROKEE ARROW III SERVICE MANUAL
INSPECTION
Summary of Contents for ARROW III
Page 4: ...THIS PAGE INTENTIONALLY LEFT BLANK 1A4...
Page 12: ...THIS PAGE INTENTIONALLY LEFT BLANK 1A12...
Page 94: ...Figure 4 2 Wing Installation Revised 2 13 89 1D22 CHEROKEE ARROW III SERVICE MANUAL STRUCTURES...
Page 171: ...lH3 INTENTIONALLY LEFT BLANK...
Page 172: ...lH4 INTENTIONALLY LEFT BLANK...
Page 286: ...THIS PAGE INTENTIONALLY LEFT BLANK Revised 2 13 89 2A8...
Page 528: ...INTENTIONALLY LEFT BLANK 2K10 THRU 2L24 2K10...